Large Screener Crusher Attachment Turns Loaders And Excavators Into High-Efficiency Processing Machines For Mining Applications
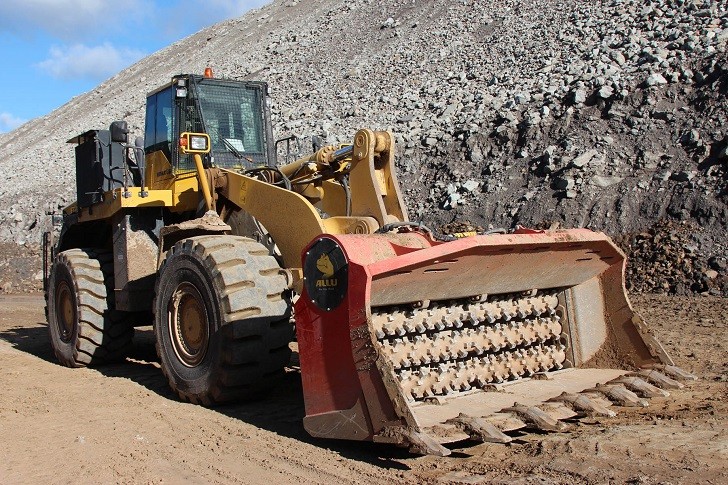
As costs for fuel, personnel, equipment and regulatory compliance rise, the extraction of resources from the ground in North America is becoming more expensive and complex. Inefficiency in the mining process adds to the cost of doing business, and often is a result of unnecessary processing steps, extra handling and wasted material.
Just about any mining application will follow many of the same traditional processing steps, whether it is hard rock mining, soft rock mining or quarrying. After blasting or excavating, large trucks transport the material to primary and secondary crushing and/or grinding and screening stages. Although the processes have remained the same for decades, this practice of taking the rock to the machine typically results in capital expenses from equipment purchases, as well as wasted material, time and fuel – ultimately resulting in unnecessary cost. It stands to reason, therefore, that anytime you can reduce processing steps in mining, you also are reducing time and cost.
The influx of track-mounted crushers and screens into North America has allowed some operators to let the machine follow the material in a number of applications, reducing haulage costs. But the technique still requires machinery to load, and additional machinery to crush and screen the material, which adds to fuel, personnel and capital expenditures.
Taking the concept of bringing the machine to the material one step further, there is an option for soft-rock mining that has been developed by ALLU Group. The ALLU M-Series Screener Crusher attachment, for use on excavators from 50 tons to 160 tons or wheel loaders from 30 tons to 90 tons, is allowing some mining companies to reduce from three or four separate processing steps – crushing, screening, mixing and loading – combining them into one step. The result is a loading/processing machine that also is highly mobile.
A large screener crusher attachment (sizes range from 5 cu yd to 11.1 cu yd) allows the operator to excavate and/or scoop ROM or blasted soft rock material – falling between 1 and 4 on the Mohs scale – and crush it to desired size as it is being loaded onto a truck, conveyor or stockpile. At the same time, the screener crusher attachment can screen out harder rock impurities or fines, which are then dumped into a waste or separate material pile.
Powered by the carrier hydraulics through an auxiliary circuit, the attachment requires no additional fuel source to operate, and generates no emissions of its own. Different processing drum configurations allow the attachment to be adapted from crushing to screening to a combination of both, producing fragment size configurations of 50, 75, 100 and 150 mm. The attachment can be utilized in open pit, open cast and underground mines.
By screening, crushing and loading in one step, the screener crusher attachment allows mining companies to reduce capital expenditures by reducing the amount of equipment needed onsite. Fewer machines and at-the-face processing also mean that haul fleet and processing machine wear and personnel costs are reduced. And with production rates up to 650 TPH, the one-step processing also is a time saver.
In North America, the M-Series is viable for a number of soft rock applications, including coal, gypsum, salt, phosphate and oil shale/oil sands, as well as for some aggregate applications.
Coal Processing
The screener crusher attachment is used to crush coal ROM at the same time that it loads the material into trucks, eliminating the need for more costly crushing and screening equipment. Because the coal is being crushed prior to haulage, it improves hauling efficiency by eliminating air voids in the truck bed. At the secondary stage for coal, the attachment can be used to crush and feed at power plants, harbors and depots.
Gypsum
Gypsum, mined from quarries or underground mines, is typically hauled to a stationary processing plant above ground. A screener crusher attachment can reduce the material size at the source, eliminating a processing stage and also increasing hauling efficiency. Set up as a fine screener, the attachment can further break down the product and separate any hard impurities from the material.
Salt
In underground rock salt mines, screener crusher attachments are used to crush material directly as it is loaded onto a conveyor. By completing one processing step at the loading stage below ground, it eliminates a separate processing step at the surface.
Phosphate
In eastern U.S. phosphate mines, the screener crusher attachment can be used at the secondary stage, crushing the overruns from the primary stage. The 4-inch-plus overrun material is typically considered to be a waste product. But there is enough phosphate within the rock to make it worth liberating using the large screener crusher; the leftover rock (generally limestone) can be sold as a secondary product. In the Western U.S., the phosphate mined in Idaho and Utah requires extensive crushing, screening and grinding to liberate the material from the rock, also providing opportunity for the screener crusher attachment to eliminate a step.
Oil Shale/Oil Sands
The first North American oil shale operation has only recently received permission to go online and produce 300,000 barrels as a demonstration of its capabilities. In other parts of the world, the mine-sized screener crusher attachment has been found to be especially well-suited for processing oil shale in the production of kerogen. Because it can screen out the harder limestone that often is found with oil shale, the end product that is loaded into haul trucks has already been refined and requires less processing.
Additionally, more efficient loading of the desired material allows the mine owner to reduce the number of trucks in the fleet.
Aggregates
While the large screener crusher attachments are capable of crushing softer aggregates, such as limestone and dolomite, for more efficient loading at the face, they also have possible use as a pre-screener of fines in harder stone such as granite, trap rock and basalt.
In North America, the M-Series is viable for a number of soft rock applications, including coal, gypsum, salt, phosphate and oil shale/oil sands, as well as for some aggregate applications.
Coal Processing
The screener crusher attachment is used to crush coal ROM at the same time that it loads the material into trucks, eliminating the need for more costly crushing and screening equipment. Because the coal is being crushed prior to haulage, it improves hauling efficiency by eliminating air voids in the truck bed. At the secondary stage for coal, the attachment can be used to crush and feed at power plants, harbors and depots.
Gypsum
Gypsum, mined from quarries or underground mines, is typically hauled to a stationary processing plant above ground. A screener crusher attachment can reduce the material size at the source, eliminating a processing stage and also increasing hauling efficiency. Set up as a fine screener, the attachment can further break down the product and separate any hard impurities from the material.
Salt
In underground rock salt mines, screener crusher attachments are used to crush material directly as it is loaded onto a conveyor. By completing one processing step at the loading stage below ground, it eliminates a separate processing step at the surface.
Phosphate
In eastern U.S. phosphate mines, the screener crusher attachment can be used at the secondary stage, crushing the overruns from the primary stage. The 4-inch-plus overrun material is typically considered to be a waste product. But there is enough phosphate within the rock to make it worth liberating using the large screener crusher; the leftover rock (generally limestone) can be sold as a secondary product. In the Western U.S., the phosphate mined in Idaho and Utah requires extensive crushing, screening and grinding to liberate the material from the rock, also providing opportunity for the screener crusher attachment to eliminate a step.
Oil Shale/Oil Sands
The first North American oil shale operation has only recently received permission to go online and produce 300,000 barrels as a demonstration of its capabilities. In other parts of the world, the mine-sized screener crusher attachment has been found to be especially well-suited for processing oil shale in the production of kerogen. Because it can screen out the harder limestone that often is found with oil shale, the end product that is loaded into haul trucks has already been refined and requires less processing.
Additionally, more efficient loading of the desired material allows the mine owner to reduce the number of trucks in the fleet.
Aggregates
While the large screener crusher attachments are capable of crushing softer aggregates, such as limestone and dolomite, for more efficient loading at the face, they also have possible use as a pre-screener of fines in harder stone such as granite, trap rock and basalt.