Economical all-rounder on four axles: Liebherr unveils the new economical and versatile LTM 1090-4.2 mobile crane
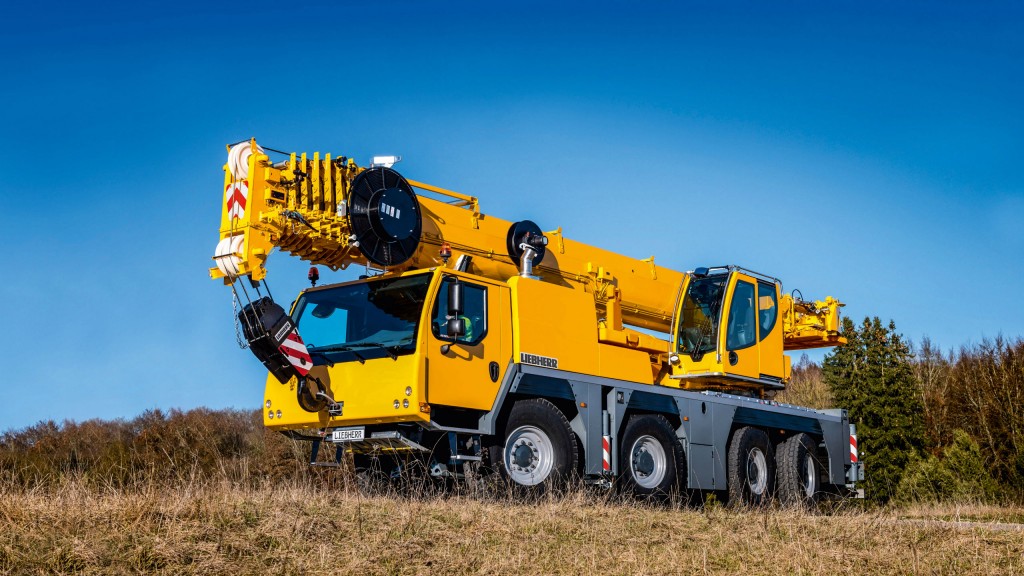
Liebherr has unveiled a versatile, economic 4-axle machine the new LTM 1090-4.2 mobile crane. The crane combines mobility, performance and economy in a one comprehensive package. The new 90-tonne (110 USt) crane is suitable for global economical mobility as it can travel with an axle load of 10 tonnes (22,050 lbs), 12 tonnes (26,400 lbs) and 16 tonnes (35,300 lbs). It features a 60-metre (197 ft) telescopic boom, a whole 10 metres (33 ft) more than its predecessor, the LTM 1090-4.1. The new crane carries 8.8 tonnes (19,400 lbs) of ballast with a 12-tonne (26,400 lbs) axle load, 2.1 tonnes (4,600 lbs) more than its predecessor. In this configuration the LTM 1090-4.2 is now the most powerful 4-axle crane on the market. ECOdrive and ECOmode make the new 90-tonne (110 USt) crane particularly green with lower fuel consumption and noise emissions. Liebherr innovations VarioBallast and VarioBase® also deliver improved performance, flexibility and safety for this new crane model.
Efficient mobility – independent to local axle load requirements
The development of the new LTM 1090-4.2 focused on meeting a very wide range of axle load requirements to enable the crane to deliver low cost global mobility. Even in countries where mobile cranes with a 12-tonne (26,400 lbs) axle load are permitted on the roads, crane operators have for some time been requesting cranes which can be driven with 10 tonnes (22,050 lbs) per axle by simply removing the ballast. This version delivers major benefits for road licensing and route approval procedures.
Although the boom is 10 meters (33 ft.) longer than the previous model, and its weight is heavier towards the front axles, Liebherr engineers created uniform axle loads of less than 10 tonnes (22,050 lbs) for the new LTM 1090-4.2. It does not to exceed a gross weight of 40 tonnes (88,200 lbs). To achieve this, the first axle was positioned in front of the front sliding beam box and the spacing between axles 2 and 3 has been extended. The larger axle spacing also has a beneficial effect on road licenses in many countries.
This also creates more space in the ballast storage area on the undercarriage which allows the ballast radius to be adjusted over a very large range. The new LTM 1090-4.2 also features the innovative VarioBallast which means that it can be operated with two different ballast radii: 3.77 meters (12.4 ft.) or 4.71 meters (15.5 ft.). The ballast radius can be reduced by 940 mm (37 in) quickly and easily using standard mechanically slewing ballasting cylinders to ensure that the ballast radius remains inside the supports. This solution is one of the main advantages of the new 90-tonne (110 US ton) model when used in constricted conditions.
The maximum of 22.5 tonnes (49,600 lbs) of ballast is distributed variably, so that in addition to the 10-tonne (22,050 lbs) and 12-tonne (26,400 lbs) axle load versions, uniform axle loads of 16 tonnes (35,300 lbs) can also be achieved, for example in Great Britain. The greater space between axles 2 and 3 is used to store support timber. This eliminates the need for a box for support timber at the rear of the vehicle. In addition, the new 90-tonne (110 US ton) crane has additional storage compartments for attachment and other equipment on the crane chassis.
Even with 16.00 R25 tires, the new crane measures just 2.55 meters (8.4 ft.) in width. The vehicle width has been reduced by 0.25 meters (0.82 ft.), which is a benefit when driving on public roads, and also makes a difference on constricted building sites.
Great performance with 60-meter (197 ft.) telescopic boom
The ability to carry up to 8.8 tonnes (19,400 lbs) of counterweights with an axle weight of 12 tonnes (26,400 lbs) is a tremendous value for a 4-axle crane. In combination with VarioBallast, Liebherr has managed to make the new LTM 1090-4.2 the most powerful crane in the 12-tonne (26,400 lbs) axle load configuration. This means that crane operators can complete the vast majority of crane jobs at low cost without having to transport additional ballast. Additionally, the optional VarioBase® generates a significant increase in lifting capacity for working areas above the supports. For the very first time, the combination of VarioBallast and VarioBase® provides crane operators with maximum flexibility for difficult sites in the 4-axle class.
Its length of 60 meters (197 ft.) makes the telescopic boom one of the longest in the entire 4-axle class. In addition a 9.5 to 16-meter (31 ft. - 52 ft.) folding jib is an available option, which can also be adjusted hydraulically between 0° and 40°. A 2-meter (6.6 ft.) assembly jib and a rooster sheave - which can be swung to the side - is also part of the equipment list.
ECOdrive and ECOmode reduce fuel consumption and noise emissions
A six-cylinder Liebherr diesel engine in the undercarriage which develops 330 kW / 449 bhp and torque of 2,335 Nm (1,722 lb-ft.) provides the LTM 1090-4.2 with all the power it needs. The engine meets the Stage IV / Tier 4f emissions regulations. Liebherr can also supply the engine in an ECE-R.96 version (which corresponds to Stage IIIa) for countries with less stringent emission regulations.
The new ZF-TraXon gearbox is used to transmit the power to the crane's axles. As with its predecessor - the AS-Tronic - the 12 gears are changed automatically. ECOdrive is a new feature. The add-on eco mode defines enhanced drive properties which save fuel and reduce noise.
Liebherr has continued its single-engine strategy on the new LTM 1090-4.2. The omitted weight created by the elimination of the superstructure engine from the predecessor model has been used to deliver a longer boom and more ballast with an axle load of 12 tonnes (26,400 lbs).
Along with the latest developments from the Liebherr mobile crane series, the new LTM 1090-4.2 also features ECOmode for crane operations to reduce fuel consumption and noise emissions. The complete pump drive can be disconnected automatically when the engine is idling and then reconnected by the intelligent controller in a matter of seconds, when it is required. While the pump drive connections automatically occur, the crane controller calculates the perfect engine speed for the selected work speed by using the control lever to avoid unnecessarily high engine speeds. This process results in reduced fuel consumption by up to 10% during crane operations.
Company info
1015 Sutton Drive
Burlington, ON
CA, L7L 5Z8
Website:
liebherr.com/en/can/about-liebherr/liebherr-worldwide/canada/liebherr-in-canada.html