Total solution
Interior concrete formwork and rebar had to fit tightly against the wall; any mistake in caisson placement would cause a problem.
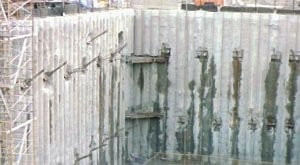
by Dan Brown
Kenaidan Contracting Ltd and its subcontractors were charged with expanding the water treatment plant in Mississauga, Ontario, from a capacity of 347 million litres per day to 500 million litres per day.
The project involved building a walled-off excavation measuring roughly 50 by 55 metres in plan. The perimeter of the excavation was a polygon with 10 sides located near the existing water treatment plant. The depth of the excavation varied, ranging from 5 metres to 12 metres to 21 metres.
A subcontractor to Kenaidan drilled one-metre-diameter caissons side-by-side around the excavation and filled them with concrete. In every second caisson, the subcontractor placed a steel H-pile. When the caissons were all placed, the subcontractor excavated the hole. As the excavation went down, anchors were drilled through the wall into the soil to tie back the secant wall formed by the big caissons.
“The project was going 100 miles per hour and we had this big hole with no access to the caisson walls to measure them,” said Dorin Nita, building information modeling manager. Kenaidan had figured on a tolerance of seven centimetres on the secant wall. Interior concrete formwork and rebar had to fit tightly against the wall; any mistake in caisson placement would cause a problem.
“We use 3D models on the job,” said Nita. “The challenge for us is to secure accurate and representative as-built information that covers the entire area in question. A 3D as-built will do that, so that’s what we need.”
Using conventional surveying equipment would have taken two extra weeks to obtain the detail required, Nita said. The excavation and other ongoing activities would make it difficult for a man in the hole to survey the walls.
Instead, Kenaidan secured a Topcon Positioning System Imaging Station (IS) to shoot the walls and produce 150,000 points on the walls. “It only took us eight hours to produce the 150,000 points,” says Nita.
The Topcon IS is a robotic total station with dual integrated imaging cameras. The Imaging Station automatically takes a series of images defined by the work area, and then goes back to capture shots with precise position within those images, says Greg Kettle, survey and GIS sales representative for Geoshack Canada.
“At first we thought we would scan the caisson walls using a reflectorless robotic Topcon GPT 9000,” says Nita. “Then I talked to Greg Kettle and we decided that the reflectorless station was too slow. The Topcon IS has faster performance with laser scanning. And the built-in digital camera helps you correlate as-built information with a real picture.
“From just three set-ups I shot all of the walls,” says Nita. “On the instrument we set a grid-scanning pattern to 75mm horizontal and 1 metre vertical and we produced over 150,000 points in one day.”
The instrument generated a few point cloud files which were transferred to a computer for further analysis. Nita said he used Topcon ImageMaster software to interpret the results and filter down the information. “Using the Topcon application we were able to see the pictures in the background of the point cloud and eliminate the points that were in question,” Nita said.
Next Nita transferred the point cloud to an Autodesk application where he matched it up with his 3D design model for the structure. That information was used to identify points of conflict between the as-built of the caisson wall and the future concrete structure.
“The caissons were not perfect but they were close,” he says. “We saw very few areas of interference. By having the entire point cloud I could rotate the model and see how it defines the caisson. You can see all of the deflections in the caissons.”
To resolve the interferences, Kenaidan adjusted the location of the interior walls somewhat, and in two locations chipped away concrete from the caissons to accommodate the interior structure.