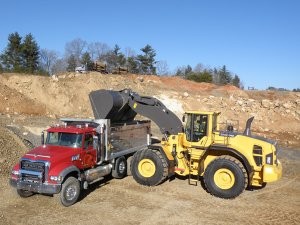
Perfectly matched to on-higway trucks, the L250G from Volvo Construction Equipment is the industry’s first wheel loader in the 39 ton (35 tonne) weight class.
The new L250G wheel loader from Volvo Construction Equipment fills the needs of the market for a machine in the 39 ton (35 tonne) weight category. Designed to match the needs of on-highway trucks, the L250G is purpose built to be a heavy-duty machine with plenty of power and features larger bucket sizes. In North America specifically, when loading triaxle on-highway trucks, a new 9.0 cubic yard rehandling bucket quickly fills the truck in only two passes – two full buckets for one full truck. Add in strength and durability and the result is more loads in less time, meaning better onsite productivity. Volvo’s latest addition to its large wheel loader range combines the optimal mix of lifting force and traction, resulting in high bucket penetration
Part of the prestigious Red Dot design winning G-Series, the L250G has a sleek and modern appearance, as well as a new engine and driveline system for improved productivity, lower emissions, greater smoothness, serviceability and operator comfort. The L250G also features a powerful Z-Bar loader linkage that allows for high breakout force for digging in hard materials. Its heavy-duty linkage, lift arms and cylinders also offer high lift capacity and rapid hydraulic reaction, resulting in faster work cycles.
Lowering emissions – without lowering productivity
First and foremost, Volvo Tier 4i technology found inside the L250G has been proven by Volvo Trucks, NA on-highway applications with ONE BILLION miles since 2007. Volvo Construction Equipment has adopted this same technology and has tuned the D13 specifically for off-highway applications.
The L250G is fitted with a fuel efficient Tier 4i/Stage IIIB certified engine that is married to drive train, hydraulics and lifting systems that are all designed and produced by Volvo to work in perfect, productive, fuel efficient, harmony. The Volvo 13 litre (13 liter), six cylinder turbocharged V-ACT (Volvo Advanced Combustion Technology) off-highway diesel engine features cooled exhaust gas recirculation and a particulate filter with active regeneration. The active-type diesel particulate filter (DPF) temporarily holds the particulate matter and then incinerates it, further reducing emissions. There is no need to stop the machine in order to conduct the regeneration process; meaning no loss of performance or production.
Producing 290 kW (389 hp), this engine provides high torque at low engine speeds. As well as meeting the stringent low emissions requirements of the legislation (which came into force in January 2011), the D13 engine also leads the industry in terms of fuel efficiency. The production of torque and power at low engine speeds removes the need to overrun the engine, which in turn extends engine life as well as lowering fuel usage and dramatically reducing noise.
Powerful hydraulics – but only when needed
Intelligent load sensing hydraulics deliver power to hydraulic functions only when needed, without unnecessary oil pumping which burns fuel unnecessarily. The hydraulic pump designs are coupled with the high torque, low rpm engine, and provide full flow at the engine’s optimal working range, eliminating the need to throttle to max rpm for higher flow, drastically saving fuel. Stronger lift and tilt functions are achieved thanks to Volvo variable-flow axial piston pumps, with higher capacities for accurate control of attachment and load.
All made by Volvo, the powertrain is designed to work in harmony for optimum performance. Engines, transmissions, drivelines, hydraulics – all are optimized to not only match each other, but to ensure maximum performance and reliability. Volvo’s heavy duty wet brake axles promote long service life, while axle housings absorb all loads from the machine, leaving the axle shafts to transmit torque, reducing stress on propeller and axle shafts.
The L250G’s transmissions features the company’s Volvo Automatic Power Shift (APS) concept, which ensures the loader always operates in the optimal gear by sensing engine and travel speed, kick-down, engine braking and other factors. Offering operators a choice of four gear shifting programs, APS results in more efficient work cycles with lower fuel consumption and wear.
Up to 15% fuel savings
Consisting of a new torque converter with Lock Up and free wheel stator, Optishift is a new system that integrates the Volvo patented Reverse-by-Braking (RBB) function – both significantly reducing fuel consumption together – by up to 15% – as well as increasing operator comfort and driveline durability. When changing from forward to reverse (or vice versa), RBB applies the standard service brakes instead of the torque converter, slowing the machine and putting less stress on the converter and transmission. OptiShift can significantly reduce fuel consumption in operations such as load and carry – as well as in short cycle loading. The driveline lock up, meanwhile, improves drive response, rimpull and incline performance, and fuel efficiency.
Industry-leading CareCab
The L250G is fitted with the latest generation Volvo Care Cab. Extending its already legendary status, it is ROPS/FOPS approved and visibility in the spacious new cabin is excellent, to the rear, to the bucket edge – and to the centrally located instrumentation. With controls that fall easily to hand, operators can breathe easily thanks to efficient air-management and filtering systems – and get on with the job in hand in a comfortable, clean, low-noise and vibration work environment. The servo controls are mounted on the operator seat and allow the selection of a number of settings located on the front right pillar that are easily reached, such as Return-To-Dig, Boom Kick Out and Bucket Leveller that allow repetitive machine functions to be made with great precision. To encourage operators to work smoothly, the accelerator pedal applies an appropriate amount of mechanical back pressure, to encourage low fuel consumption operating techniques. An optional joystick steering and gear shift control system called Comfort Drive Control is also available, which eliminates tiring arm movements for the operator, improving productivity in short cycle duties.
Real time information = real benefits
The G-Series comes with advanced electronic monitoring diagnostics that are designed to prolong machine life, enhance uptime and maximize productivity. Contronics monitors information from engine, transmission, brakes etc. in real time and alerts the operator via a bright and easy-to-read information panel if problems occur. MATRIS, meanwhile, charts and analyses data on machine handling and operation. VCADS Pro is a system that allows a machine to be fine-tuned to specific applications. Finally, CareTrack, the Volvo Construction Equipment telematics system, allows machine location and operating data to be securely viewed via the internet from anywhere in the world, aiding fast decisions on maintenance and repairs. CareTrack is standard equipment on the new G-Series, including the L250G and features three free years of subscription.
Servicing is made easy with the G-Series, with daily pre-start items quickly checked and scheduled service items conveniently grouped together. The L250G is fitted with a newly designed engine cover that provides better ventilation of the engine compartment. The cover can be electronically opened in the rearward direction – giving good access for fast and easy cleaning or servicing duties. Centralized, ground level lubrication banks lower the time spent on maintenance. And consumables like filters are easy to reach and replace.
It’s easy to get attached to the L250G
The L250G come with a wide selection of Volvo genuine buckets to suit a range of applications. The new design Rehandling Buckets gives faster and more efficient bucket fill – and up to 10 % better fuel efficiency. All purpose built using the same quality as the rest of the machine. Together with the Volvo ground engaging tools and a selection of machine protection, convenience and safety options give L250G the highest possible production.
Model specifications
Model L250G
Engine D13H-E (Tier 4i)
D13H-F (Stage IIIB)
Max. power at 1,500 rpm (25 r/s)
SAE J1995 gross 291 kW (390 hp)
ISO 9249, SAEJ1349 net 290 kW (389 hp)
Max. Torque at 1,100 rpm (18.3 r/s)
SAE J1995 gross 1645 lbf (2231 Nm)
ISO 9249, SAEJ1349 net 1637 lbf (2219 Nm)
Breakout force 65, 329 lbf (291 kN)
Static tipping load at full turn 51,637 lb (23,422 kg)
Buckets 6.7 – 13.3 yd3 (5.1-10.2 m3)
Operating weight 75,000 – 86,000 lb (34 -39 t)
Tires 29.5R25 L4, 875/65 R29