Hydrocarbon and chemical resistant barrier membrane
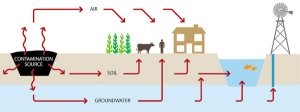
Puraflex is a new hydrocarbon and chemical resistant barrier membrane designed for containment, separation, environmental and groundwater protection projects. Its proven resistance to hydrocarbons and toxic industrial chemicals provides a cost-effective solution for brownfield developments.
Environmental Risk Assessments for brownfield sites require a soil analysis to identify concentrations of hydrocarbon and toxic chemical contaminants. The integrity of any risk assessment therefore relies on the permeation data of separating geosynthetic membranes so that accurate modelling predictions of the migration of contaminants can be made from the source, through the membrane and into pathways to receptors.
Limited chemical resistance data is generally available to environmental consultants and design engineers. Often charts provided by geosynthetic membrane manufacturer’s list chemicals as simply Resistant, Limited Resistance or Unsuitable. Hitherto, material selection for separating membranes has been on a best-fit basis without any significant supporting quantitative data.
Though considered chemical resistant, HDPE and other common homogeneous geosynthetic membrane materials are susceptible to Hydrocarbon permeation due to the limitations of their chemical resistance spectrum. HDPE is a hydrocarbon and because they are the same species, hydrocarbons permeate more readily through HDPE membranes.
Industrial Textiles & Plastics Ltd (ITP) is a manufacturer of chemical protective clothing materials resistant to chemical and biological warfare agents. This technology is incorporated in Puraflex which been specifically formulated to resist hydrocarbons and toxic industrial chemicals commonly identified in contaminated land risk assessments.
The barrier membrane is an extruded composite comprising protective polymeric layers on both sides of a chemical resistant inner core. The outer surfaces of the membrane are Non-Polar polyolefinic polymers and like HDPE, insoluble to Polar chemicals but not to Non-Polar hydrocarbons. It is Puraflex’s Polar core, sandwiched in the middle of the membrane that provides the effective barrier to hydrocarbons and other Non-Polar chemicals.
Puraflex’s multilayer composite construction provides enhanced barrier performance against a wider chemical spectrum for Polar and Non-Polar challenge chemicals. The benefit can be illustrated by comparing the concentration gradients for Benzene, a well known carcinogenic hydrocarbon, across a homogeneous HDPE membrane and Puraflex.
The concentration gradient for Benzene, a well know carcinogenic hydrocarbon, is linear across a generic 1.5mm thick HDPE membrane. At a concentration of 100 mg/kg, Benzene permeates at over 500mg per square metre per annum.
However across Puraflex, there is an abrupt change as the Benzene reaches the Polar core region (shown in blue) of the membrane. This results in a significantly lower Permeation Rate of 0.000352mg per square metre per annum for the same concentration level.
To assist environmental consultants and design engineers, ITP provides Puraflex Permeation Modeller software, a unique and powerful program which makes use of soil contaminant concentrations derived from site investigation soil sampling. Soil analysis data is simply uploaded into the software and key site-specific variables, including soil temperature, moisture and density are entered. The software calculates predicted permeation rates for over 200 hydrocarbons which are then imported directly in to environmental risk assessment models (such as the Environment Agency’s CLEA modelling software) to determine whether the proposed site and the wider environment is suitably protected.
Where risk assessments determine that the best design solution is a separation membrane, whether installed under the entire site or the building’s footprint, Puraflex provides a cost effective, robust and high performance barrier to hydrocarbons and toxic industrial chemicals.