Liebherr R 9XX concept crawler excavator: pioneering electric hybrid power train technology
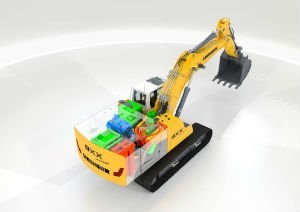
The R 9XX concept crawler excavator that Liebherr is exhibitED at the 2013 edition of Bauma features pioneering electric hybrid power train technology. It is an example for energy recuperation techniques that will be possible in the future and will improve the economy and sustainability of construction machines.
The R 9XX concept is based on the machine structure and system architecture of a 40-tonne excavator and is powered by a Liebherr construction-machine engine which, with a power output of 160 kW (218 hp) is much smaller than the engines normally encountered in this service-weight category. This cuts fuel consumption and emissions by obtaining additional performance from the electric hybrid power train.
The main work areas for crawler excavators in the 40-tonne class are high-volume earthmoving and arduous tasks in quarries and opencast mines. The typical work cycles that these tasks involve are a promising technical starting point for a hybrid energy supply – in other words for a driveline using a combination of different sources of power.
The diesel engine is the main source of energy for the R 9XX concept; it operates together with hydraulic and electrical energy storage devices – components newly developed by the Liebherr Power Train Competence Centre, and comprising the electric slewing gear, the electrical energy store – which uses “Supercaps” – and the electronic control unit. A pressure reservoir and a generator are used to recover hydraulic energy. This combination of electrical and hydraulic power train features reduced fuel consumption, but at the same time increases the excavator’s load handling performance.
The lifting cylinders are controlled without throttle valves, in order to avoid loss of energy before the recuperation stage of the process is reached. When the working equipment is lowered, the energy released by this movement is stored temporarily by way of a hydro-mechanical energy generator in a hydraulic storage unit and the electrical Supercaps. In this way, drive and storage take place without any losses due to the system, and resources are used at maximum efficiency.
The slewing gear is electrically driven and energy is also stored electrically. When braking, kinetic energy is converted into electrical energy in the generator and stored by the Liebherr Supercaps. This energy is released again when the superstructure has to be accelerated as part of the machine’s operating cycle.
The diesel engine’s power output can be supplied directly to a consumer or input to the electrical energy store. In turn, the energy store can supply the slewing gear or the hydraulic pump drive to power hydraulic movements. The system allows energy to be transferred between the various part-systems. This ensures that the diesel engine only supplies the specific amount of energy that is needed. In addition, the load imposed on the diesel engine is much more uniform, with the resulting benefits of reduced component wear and lower fuel consumption.
The R 9XX concept’s hybrid system can make short-term peak power available up to twice the nominal output of the diesel engine. No crawler excavator using this principle has so far reached the market.
Company info
1015 Sutton Drive
Burlington, ON
CA, L7L 5Z8
Website:
liebherr.com/en/can/about-liebherr/liebherr-worldwide/canada/liebherr-in-canada.html