Innovative Bridge Stabilization Solution
Polyurethane resin injection proves to be permanent and effective
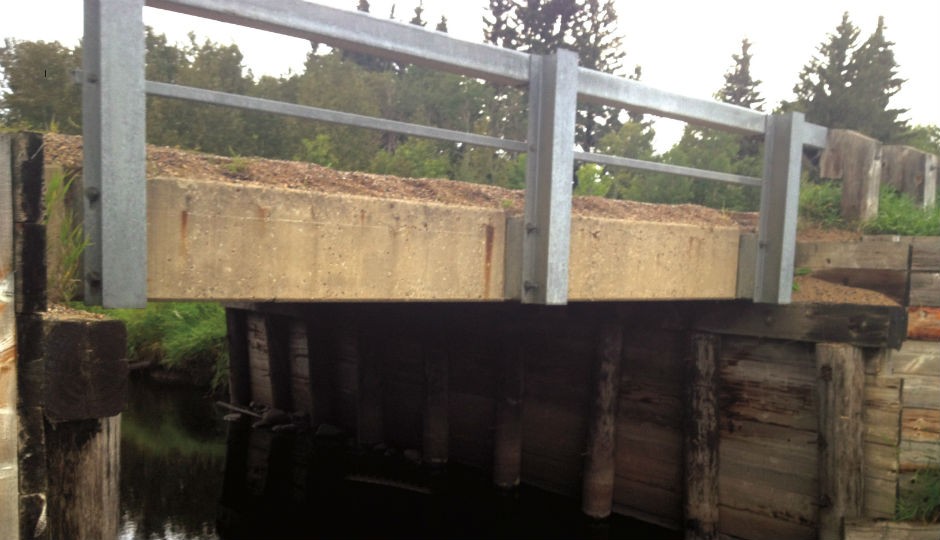
Saskatchewan is a prairie province with open spaces and a widely distributed population that requires a lot of roads. The Dominion Land Survey system, which covers most of western Canada and was initiated in 1869, includes road allowances one mile apart for those running north-south and two miles apart for those running east-west. The province has made good use of these. Its municipal and highway networks now total 190,000 kilometres of roadway. That’s the most of any Canadian province, and may be the most roadway per capita of any jurisdiction anywhere in the world.
So the Saskatchewan Ministry of Highways and Infrastructure is managing a huge amount of transportation infrastructure with a relatively small tax base, and has to be exceedingly smart about maintenance. A new innovation in bridge maintenance is a good example of this. Saskatchewan has many rivers and streams, and so there are a lot of bridges to complement the many kilometres of roadway. Much of this critical infrastructure was built decades ago and is showing signs of age.
Bridges with abutments and wingwalls made of wooden timbers – and there are a lot of them in Saskatchewan – have deteriorated over the years and allowed for undermining of wingwalls and abutment walls. Normally a semi-arid region, Saskatchewan is passing through a much wetter era, and storm events and unusually high water levels have resulted in voids under and around bridge structures that often cause settlement and very uneven pavement transitions. Getting the roadways back to level is not a simple fix.
“Traditionally, we excavate down quite a bit to fix significant settlement in the bridge approach,” says Ministry bridge preservation engineer Brodie Thompson, P.Eng. “We are often dealing with very large voids caused by years of erosion.” Permanently filling and settling the voids usually requires pavement removal, deep excavation, a geotextile fabric layer, rip rap, granular fill, and repaving. And of course, work of this scope requires traffic disruption, at least of alternate lanes, and sometimes complete road closures and traffic rerouting.
Two years ago, the Ministry tried a new repair technique based on the injection of hydrophobic polyurethane resins that expand in moist soils and fill voids permanently. This solution does not require lane closures, and is not significantly more expensive than previous methods. And so far, regular inspection suggests that these repairs are stable and permanent, eliminating ongoing repairs.
What are polyurethane resins and how do they work?
The Ministry’s pilot project was sparked by a conversation with Glenn Votkin, president of Martech. “We’d had meetings with the Ministry of Saskatchewan,” says Votkin. “We introduced a non-invasive repair technology that binds and seals deconsolidated soils to reinstate structure – this addresses several common problems associated with roads and bridges. It was Brodie Thompson at the Ministry who recognized that the application could minimize disruption of service and reduce costs to taxpayers, and so he supported a couple of pilot projects.”
“They mentioned a road stabilization pilot project in Alberta, and that turned on a light bulb for me,” says Thompson. “It occurred to me that instead of injecting resin downward from the road surface, we could work from under the bridge and inject the resin sideways through the abutments and wing walls.”
Injecting resin from underneath bridges would be a big advantage, because traffic disruption wouldn’t be required. “I would say the reason we went ahead with these pilot projects is that the actual construction costs, compared to our typical method requiring excavation, was really about the same,” Thompson explains. “But there was a big advantage to the public – user costs don’t show up on our bottom line, but avoiding traffic closures would save a lot of time and inconvenience for the people we serve.”
Martech is in the business of making connections between progressive infrastructure solution providers and local government agencies that build and maintain infrastructure. The firm works with dozens of companies in the infrastructure and mechanical space, aligned around the idea of non-invasive repair options that offer a better-than-new construction result with reduced costs and timelines.
In this case, Votkin felt that polyurethane resins from Atlanta-based Prime Resins would be a fast way to mitigate the creation of subsurface soil voids behind and below Saskatchewan bridge abutments, and that Larry Graham, president of New Shield Ltd., would be the right contractor to apply the solution.
Polyurethane resins that are injected into voids, for the purpose of stabilization, have been in use for more than 20 years. Basically, polyurethane compounds in a state of low viscosity are injected at high pressure into voids and loose soil. The polyurethane then sets in the presence of water and catalysts, forming a permanent, highly stable mass that fills voids and densifies loose soil.
It’s a flexible process; resin formulation, catalyst selection, and soil moisture can all be managed to match specific resin properties with specific conditions. For example, resins can be selected for foaming and expansion properties that lift slabs, and catalytic reactions can be designed to speed up or slow down the expansion.
In this case, Graham worked with the Ministry and Martech to design a mitigation technique that would fill voids and stabilize loose soil with minimal expansion, and used a hydrophobic formulation (Prime Resins’ Prime Flex 920) that would not degrade when exposed to water – in fact, moisture in the surrounding soil is required for the resin to set, and helps maintain the mass’s flexibility once in place. The idea is to fill voids in such a way that subsequent inflows and leaks are diverted and prevented in ways that eliminate any future erosion.
What’s a typical resin injection project like?
Graham says that in some ways, the resin injection project was straightforward. “I do a lot of specialty work, figuring out sometimes unusual solutions for infrastructure challenges that don’t come up all that often,” he says. “In that context, resin injection wasn’t especially complicated; the drilling and pumping relied on standard tools, and I was able to determine reaction times with help from Prime Resin and a little experience.”
Set up, on the other hand, was a little tricky. Graham needed access to the timber bridge abutments and wing walls facing the water, which meant he needed scaffolding under the bridge, on sloping soil and partially in the river or creek. He did this by hauling in material with a flat-bottomed duck boat, trailers, and a small, four-wheel drive ‘quad’.
Scaffolding in place, Graham then proceeded with injection. This involves drilling small-diameter holes through the bridge structures, inserting a small nozzle, and pumping in catalyzed resin. But there are some tricky aspects.
Drilling, for example, often leads to surprises; “We can’t see through walls, of course,” Graham says. “And sometimes we hit rock. Other times, soil is looser than expected, and we have to rethink how much resin is needed, and how it should be formulated.” One lesson learned from this is to have a rock drill on hand, which is also useful for drilling through pavement when the need arises.
Another detail to account for is soil moisture. “The resin actually needs water to react properly,” Graham explains. “And of course, I do this work under the bridge, where it’s sheltered, so I can’t be sure there’s enough soil moisture even if it’s been raining.” So, Graham always injects water ahead of the resin, to be sure there is enough moisture available.
Several additional improvisations were required during the bridge abutment projects. After working on the site, Graham created custom brackets for scaffolding, for example, and also fabricated custom probes for use at different points along the abutment and wingwall faces. He also developed a feel for the right amount of catalytic ‘accelerator’ to use, given what he learned about soil conditions during initial drilling and probing. On these projects, which were “typical” based on Graham’s continuing experience with resin injection, about 200 gallons of material were injected behind each abutment. Resin is injected with ‘paint sprayer’ type pumps, and is usually forced in until Graham sees excess resin emerging from previously drilled nearby holes. This verifies that he has completely filled voids and saturated the soil as needed.
Each of the pilot projects took four days to complete; “That’s a couple of days for setup, and a couple of days for actual drilling and injection,” Graham says. Inspection is difficult, since visual access is blocked and CCTV isn’t practical. But regular inspections in the two years since project completion, including spot checks after storm events, have shown that the resin mass is staying in place and that soil appears to be permanently stabilized – there are no signs of movement in soil or pavement around the bridges. The Ministry’s goal for the project is to defer major bridge rehabilitation, or replacement, for at least 15 years and this appears to be likely.
And this work was done with no rerouting of traffic. Graham’s work required minimal staging area, was done from beneath the bridge and next to abutments and wingwalls, and in no way destabilized the bridge during rehabilitation. So drivers suffered no inconvenience during the project, and some of them may not even have noticed the interesting infrastructure project taking place beneath them as they drove over the bridges.
Two years later, the resin repairs are holding up well to storm events and spring melt, and Thompson is optimistic. “We’ll be using resin injection again,” he says. “In projects where erosion has caused voids,and traffic disruption would be a big deal, soil stabilization with resin injection appears to be a good solution for us and will likely keep bridges in good shape until we do major superstructure work in 15 years or so. And we’re also looking at a situation where an old cast-in-place concrete culvert was extended with corrugated metal pipe. There is concern that the culvert might be leaking at the interface, and we think resin injection will be a good fit.”
Eliminating traffic rerouting and avoiding ongoing maintenance by the use of bridge rehabilitation, which took just four days to complete, has made the Saskatchewan Ministry of Highways and Infrastructure confident that the return on investment for resin injection technology is good, and inspections in the two years since project completion confirm that. Polyurethane resin injection appears to have a permanent place in the Ministry’s suite of bridge repair solutions.
Angus W. Stocking is a licensed land surveyor who has been writing about infrastructure since 2002.