Expanding Canada’s Third Busiest Port
Ringer cranes from Manitowoc and formwork from EFCO featured in $220-million multi-user wharf constructed at the Port of Sept-Îles, Quebec
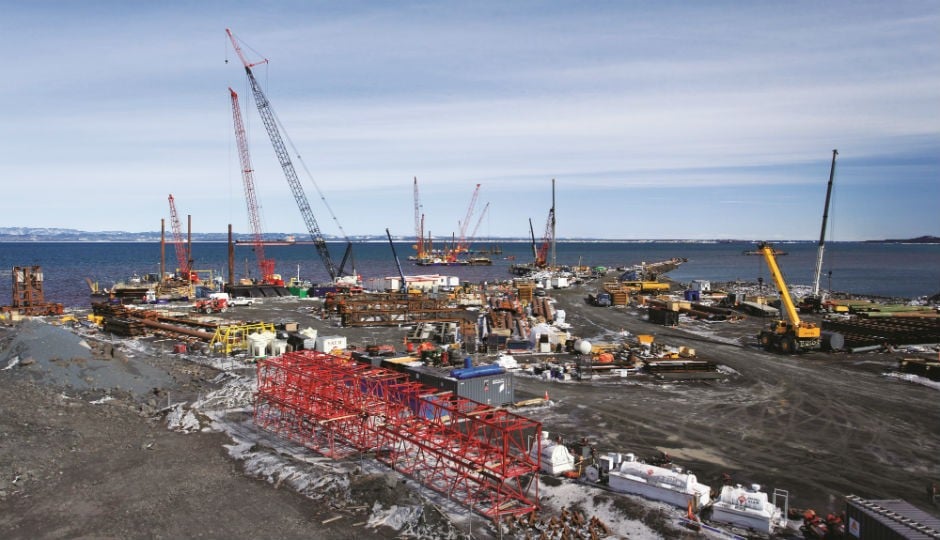
The Port of Sept-Îles, located in Quebec at the entrance to the St. Lawrence Seaway, is the gateway for iron ore shipped from mining operations in the Labrador Trough, a 160- by 1,600-km belt of ore spanning Quebec and Labrador. Along with iron ore, the port also handles aluminum, petroleum coke, limestone and other basic materials. Combined, some 23 million tonnes of bulk cargo move across the port’s 13 berths annually.
Sept-Îles is already the third busiest port in Canada, behind only Vancouver and Saint John. It has recently undergone a significant expansion to accommodate higher volumes of iron ore shipped out from the Labrador Trough, as companies there ramp up operations to take advantage of higher expected demand for the steelmaking ingredient from China and other Asian economies.
The expansion, which is expected to be fully completed sometime this fall, involves construction of a new multi-user dock located across the Sept-Îles bay at Pointe Noire. Building and installing the 400-metre wharf and 560-metre approach ramp, along with conveyors and shiploaders, was budgeted at $220 million. Costs were shared between the federal government and the port, which each kicked in 25 percent, and five iron ore mining companies: Labrador Iron Mines, Alderon Iron Ore Corp, New Millennium Iron, Champion Iron Mines, and Indiamultinational Tata Steel.
There are two principal reasons for the expansion. First, the water depth at Pointe Noire is currently too shallow to accommodate large ships, meaning that cargo must first be loaded onto small vessels, then transferred to larger freighters anchored further out in the bay. The new wharf will be able to accommodate the largest Chinamax freighters, capable of handling up to 400,000 tonnes, and will put an end to trans-shipments, an expensive cargo-loading process estimated to add up to US$5 a tonne for port users (iron ore is currently priced about $100 a tonne). Second, port users will have equal access to the dock and its two shiploaders, instead of having to seek permission and pay existing users Rio Tinto and Cliffs Natural Resources for the use of their cargo-loading facilities. The wharf is also equipped for two ships to load simultaneously, a considerable advantage in the freight-moving business where time and port charges must always be minimized.
Once completed, the multi-user dock is expected to add 50 million tonnes of cargo throughput a year to the Port of Sept-Îles, with the capability of expanding another 50 million tonnes later should a doubling of volume be warranted.
Manon D’Auteuil, director of engineering and sustainability at the port, said the project is the biggest expansion in the port’s history. A phased build-out of dock infrastructure began in 2004. Those improvements included a $20-million cruise terminal built in 2009, a new alumina silo constructed for $30 million, and an increase in the capacity and length of aging docks.
D’Auteuil also said that the cooperation between the five iron ore companies stood out as an anomaly from the port’s perspective. Normally they would compete for wharf space and each pay the full cost of their new facilities.
“We had people from all around the world who came here and asked questions, how we had the possibility to do that, because getting the agreement of five companies is not usual,” she said. “For us it’s a big achievement because it was not very easy. We had a lot of discussions and explained to everybody that they’ll have ‘the best for less.’”
D’Auteuil noted that all the steel and rebar built into the wharf is galvanized, meaning it will last longer in salt water conditions. Also, to protect the environment, conveyors are housed inside an enclosed gallery, preventing spillage of material into the water.
Getting to that stage of completion, however, has not been without its challenges, according to the project’s general contractor, Pomerleau. The Quebec-based company has multiple offices across Canada but does most of its business – predominantly building construction and heavy civil work – in Eastern Canada.
Pomerleau was awarded two separate contracts for the Sept-Îles port expansion: the structure including pilings, concrete forms and marine accessories such as bollards and fenders; and the mechanical work, which entailed construction of the conveyor gallery and transfer towers. The structural contract was worth $150 million and the mechanical work had a budget of $45 million.
Normand Fortin, Pomerleau’s project director- civil works, said the dockbuilding project was significant due to the scope of the work performed, and the amount and complexity of heavy equipment involved.
“A project of this size involves several very important pieces of marine equipment that we haven’t seen in Canada for a while, especially in Quebec,” he said. “We needed quite big equipment because of the size of the piles and the weight of the material we had to handle, so there was a big portion, at the beginning, for the mobilization of the marine equipment and sending out the cranes.”
For lifting piles and concrete forms into place, the company employed two Manitowoc 4100 cranes with ringer attachments, mounted on barges, along with four conventional barge-mounted cranes, including a Manitowoc 1600, a Manitowoc 2250 and a Terex crane.
The ringer attachment provides a larger counterweight away from the centre of rotation to allow for greater capacity and increased boom reach.
Along with the crane barges, additional barges were pressed into service as platforms for logistics and storing materials.
Fortin said a challenging part of the operation was lifting, placing and driving 130 caisson piles into the ocean bed, considering their weight and average 55-metre lengths.
“Given the short schedule we had, we were not able to include in our work cycle a lot of welding to drive a portion of the pile, then weld another section to reach the bedrock. So we had ordered all the piling in one length, then we had to lift and install quite heavy and long piles. That was one of the reasons why we had the ringer crane,” he said.
“When you lift a pile that is 55 metres long you always have to take more care than lifting a concrete block of 250 kilos. It was a very sensitive operation.”
For that part of the job, Pomerleau formed a joint venture with Bermingham Foundation Solutions out of Hamilton, Ontario. The work with Bermingham involved installation of the piles and drilling of the rock sockets.
The next stage involved the construction and mounting of pile caps, which provided the base for the concrete deck. The caps were constructed using the Plate Girder system designed by Iowa-based EFCO.
The self-spanning formwork was assembled on shore and then loaded onto barges and transported to the piles, where it was picked up by a crane in one piece and placed on support brackets. According to EFCO, a total of 15 pier caps of various dimensions were required for the approaches, 22 pier caps measuring 21 metres (71 feet) were needed for the main span, and 21 tie beams measuring 17.4 metres (58 feet) were cast using the Plate Girder system.
Fortin said another major challenge of the job was coordinating the logistics of moving so many parts from land to their proper locations on the water. To span the portion that was too shallow for a barge but too deep to work with standard equipment, Pomerleau built a temporary access ramp consisting of a steel structure supported on piles.
“Imagine every element has to move from on land to the water. You think about the workers every day, the boats, the concrete, the piles, the rebar. A big challenge of this job was the site logistics,” Fortin remarked.
A good example was the coordination of cast-in-place concrete forms with concrete pumpers. On shore, concrete pumpers pumped the concrete into buckets, each capable of handling about three cubic metres of material, that were lifted onto barges.
The barges were towed to the proper location on the water, where a waiting concrete pump affixed to a barge poured the concrete into the form. In all, 25,000 cubic metres of concrete was poured during the course of the job.
Harsh winter weather also factored into the operation. The 250-strong workforce consisting of steel erectors, crane operators, carpenters and labourers worked seven days a week for a major portion of the job, to make up for unforeseeable work stoppages due to wind and ice.
As the finishing touches are put on the project, including the installation and testing of two shiploaders arriving from China, Fortin said the job had its challenges, but in the end, was completed to the satisfaction of all parties involved.
“Technically, it’s been very efficient. The template system that we designed, the selection of equipment, I’d say the method’s been very good.”