Sidewalk Success with a New Zero-Clearance Paver
Folding conveyor on GOMACO GT-3200 makes paving around obstacles easy
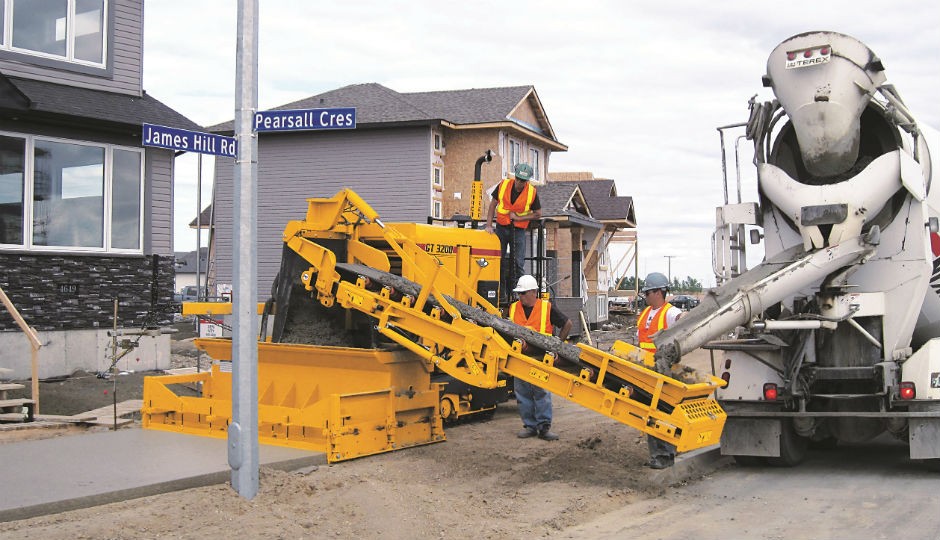
On June 12, 2013, at 8:30 in the morning, the first concrete went through Loewenhardt Construction Ltd.’s new GOMACO GT-3200 sidewalk paver on a subdivision project in Regina, Saskatchewan. At the end of the day, the company had slipformed 175 metres (574 feet) of 1.5m (5-foot) wide sidewalk, switched molds on the paver and then slipformed an additional 130 metres of 2.4-metre-wide sidewalk. By six o’clock that night, they were washing down the new machine and Jorg Loewenhardt, President of Loewenhardt Construction, had a big smile on his face.
“Jim Hayward, GOMACO’s Western District Manager, was with us that day and he said to me, ‘You look happy,’” Loewenhardt said. “I said yes. He asked if I had made money that day and after doing some quick calculations in my head, I again said yes. I actually turned a profit on the maiden voyage and that’s unbelievable. There wasn’t a bigger smile around than the one that was on my face.”
The company had been looking for a high-production sidewalk paver, one that could work within the limited and tight-clearance working conditions found in Canadian subdivisions. They had been handforming all of their stand-alone concrete sidewalk, but were falling further behind with their schedule and were having to sub out some of the work. Loewenhardt’s business partner took a trip to World of Concrete in 2013 and had the chance to look at all the options available for sidewalk paving. It was during that trip that the decision was made to buy the GOMACO GT-3200 sidewalk paver.
“My partner phoned me from Las Vegas and said, ‘This is the one Jorg,’” Loewenhardt explained. “We placed the order and the rest is history.”
The GT-3200 sidewalk paver has several features that make it the ideal machine. At only 2.6 metres wide, it’s able to get into and maneuver through tight-clearance conditions. All-Track Steering (ATS) also offers enhanced steering and mobility. For grade preparation, the sidewalk paver can be equipped with an aggregate base mold with a spreader auger or a trimmerhead for fine grade trimming. Loewenhardt’s is equipped with a 1.8-metre-wide trimmerhead.
His new zero-clearance sidewalk paver also has a 50mm-wide, 4.3m-long, hydraulic pivoting and folding conveyor with extra-long reach that allows ready-mix trucks to discharge from the street instead of having to drive over the existing curb. The conveyor can rotate 180 degrees to allow for easy loading of concrete into the hopper from either side of the machine. Then, when the GT-3200 paves up to obstacles such as light poles and trees, the ground person can swing and fold the conveyor to slipform past the obstacle. The conveyor can also be raised without being folded to avoid smaller obstacles like fire hydrants and utility boxes.
“You couldn’t ask for anything more ingenious than that conveyor belt,” Loewenhardt said. “This way the concrete truck can stay on the road and doesn’t sink out of sight into the mud. We’ve got light standards and fire hydrants in the way and if we didn’t have that conveyor belt that swings back and forth and folds up out of the way, we’d be messing up about 10 to 12 metres of walk that we’d have to come back and form by hand. We come up to an obstruction, fill up the hopper, move the conveyor belt, collapse it, move ahead past the obstruction, down goes the conveyor belt and we keep on going. It’s wonderful.”
The sidewalk mold has hydraulic adjustable sideplates to form the GOMACO edge, while a trailing stainless pan provides the smooth finish to the surface of the new sidewalk. The molds can be equipped with a bar inserter for placing transverse bars into the slab if that is a project specification. Loewenhardt ordered three different molds for their sidewalk paver: 1.2 metres, 1.5 metres and 2.4 metres wide. All of the sidewalk is 127 mm thick.
On their subdivision project in Regina, Loewenhardt has slipformed 1.8 kilometres of sidewalk so far, and soon they’ll be using their 1.2m mold for the first time, simultaneously trimming and slipforming the sidewalk.
“We do our grade preparation ourselves, lay our own subbase and grade it,” Loewenhardt explained. “We’d trim it with the GT-3200 and then go back and pour it, but now with the 1.2- and 1.5-metre sidewalk, we’re going to trim and pour at the same time. My partner went to a GOMACO University class in Edmonton that our distributor Chieftain Equipment Inc. put on. He talked to a lot of operators there who said all they do is trim and pour those widths. We know we can’t trim an awful lot, but 50mm would be no problem.”
The concrete for the sidewalk is specified by the city of Regina. It’s a 32 MPa (4,641 psi) mix design with the slump not to exceed 40 mm. Each ready-mix truck carries a five-cubic-metre load, with five trucks supplying the GT-3200 during the pours.
“I wish we had better concrete supply,” Loewenhardt said. “When we were pouring 2.4 (metres) wide, we could unload a truck in about eight minutes and then we’d have a good 10- to 15-minute wait in between truck loads. That day we slipformed 40 cubic metres of concrete, which was 130 metres of sidewalk in three hours. If we could have had two more trucks and less wait time in between, we could have doubled our production.”
Even with slow concrete delivery, the GT-3200 sidewalk machine’s production easily outperforms anything they could have produced handforming the sidewalk.
“It would have taken forever,” Loewenhardt said. “Forever! You have to set your forms, put your base in and then hand pour it. One hundred metres would probably take two days to form, prep and pour. The machine certainly does pay for itself and with a lot less work and wear and tear on the labour.“
The subdivision work consisted of several short pours, which meant that efficiently moving and transporting the sidewalk paver was a concern. The GT-3200 can be transported fully assembled, with the trimmerhead and mold attached.
“We just drive it right onto a flatbed trailer and away it goes,” Loewenhardt said. “The conveyor belt folds up and swings to the back of the machine over the sidewalk mold, (we) drive it onto the trailer, and off it goes to the next part of the subdivision.
“This machine works really good within the constraints that we have to pour sidewalk under. The sidewalk comes out really nice and there’s minimal handwork to prep it for the actual finish. It can get so close to obstructions and then we just have to move the conveyor belt and pave right past. That’s a huge time and labour savings for us.”
Sequence of photos from another project shows how the conveyor arm is raised (pic 1), folds up and out of the way of the lamp standard (pic 2) and then moves past and down the other side (pic 3).
Sequence of photos from another project shows how the conveyor arm is raised (pic 1), folds up and out of the way of the lamp standard (pic 2) and then moves past and down the other side (pic 3).
Sequence of photos from another project shows how the conveyor arm is raised (pic 1), folds up and out of the way of the lamp standard (pic 2) and then moves past and down the other side (pic 3).