RFID Tags and Monitoring System Speed Concrete Construction
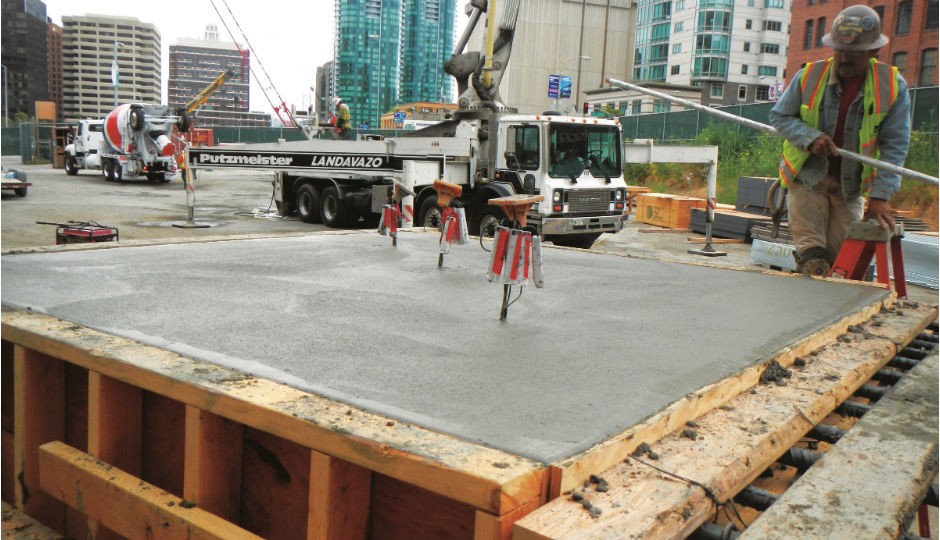
Accurately monitoring the curing of concrete can be critical on large construction projects. If a slab is not given sufficient time to cure, cracks can develop when the next slab is poured, which would ruin that section. Companies have typically used temperature loggers with wires from the device running into the concrete, since concrete gives off heat as it cures. But wired sensors can be too cumbersome for large projects, so in such scenarios, a concrete consultant often sets a conservative estimated curing timeline based on the material being used, as well as other conditions. This often means extra time is built into a project’s timeline, in order to ensure that all concrete poured is fully cured before employees proceed to the next step.
Shimmick Construction Co. preferred not to use wired sensors or build in extra curing time for the construction of San Francisco’s new TransBay Transit Center. Instead, the company chose to deploy an RFID solution provided by Wake, Inc. The system installed on the TransBay Transit Center project consists of active ultra-high-frequency (UHF) RFID tags with built-in sensors, as well as handheld readers and software to interpret the collected temperature data. The tags’ sensor probes are embedded in each concrete slab and the data is read remotely, making the system more nimble than conventional data loggers.
Shimmick is laying 100,000 cubic yards of concrete to build a below-grade substructure for the new transit facility. Next, the company intends to utilize the same Wake Inc. technology – the Wireless Concrete Maturity & Temperature Monitoring Solution, also known as HardTrack – during the building of concrete pilings for a bridge associated with the project.
The project consists of 16 concrete slabs that make up the building foundation. Each slab must be fully cured before the one next to it can be poured, to prevent it from being cracked by any strain from the subsequent slab. The RFID technology provides data regarding the temperature of the concrete after it has been poured, explains Charlie Marrow, Shimmick Construction’s project engineer. Wake’s software then determines the poured concrete’s date of maturity. That data, he says, greatly reduces the amount of time required for the cooling and hardening of concrete before the next slab can be poured.
“We had been looking for options in maturity monitoring,” Marrow says, as the firm prepared to launch the large project. Shimmick Construction needed a way to ensure that the concrete laying stayed on schedule. The company’s concrete consultant estimated the pouring and curing time at a conservative 30 days of curing per pour. Each slab must reach that time requirement before the adjacent section can be poured. However, he notes, this would not have worked with the company’s required project timeline. Therefore, the firm began looking into technology solutions that could track the exact date of curing – which could be considerably less than 30 days – thereby enabling the next slab to be poured sooner.
Curing-time estimates can lead to unnecessarily long waits, Marrow explains, which is why companies often use data loggers. A wired data-logger solution would have been unrealistic for this project though, due to the size of the area and the large volume of concrete being poured – both of which would have required the spreading of many feet of electrical wiring throughout the five-foot-thick concrete laying area.
With the HardTrack system in place, Shimmick can now capture temperature data on a daily basis, and then forward the collected information to its back-end system to be displayed in a Microsoft Excel spreadsheet. Not only can the company monitor curing progress at multiple points within each slab, but it can also share the temperature-based curing history with agencies or the owner. The Wake software uses strength-based differential measurements to determine when the concrete reaches maturity and displays that data for Shimmick on the handheld reader as the tags are being interrogated.
The temperature sensor tags (model i-Q350TL SL) are provided by Identec Solutions. Although they are powered by lithium batteries and were designed to be fully immersed in concrete, Marrow says he opted to pour concrete over each tag’s RFID tags and monitoring system speed concrete construction temperature probe, with the remainder of the tag exposed. This, he explains, allows him to detach the tag once the curing is completed and then reuse it with another probe, thereby lowering costs.
The battery-powered tags collect sensor data and store the information (they come with 10,000 bytes of memory) until Marrow or another staff member walks through the area equipped with an Identec i-CARD CF-350 reader plugged into the CompactFlash slot of a Motorola Solutions handheld computer. According to Marrow, the read range is long enough that he can be located several hundred feet from the tag and still capture its sensor data. Shimmick Construction is using approximately 100 tags, each of which is removed from one slab and applied to another as the concrete is poured.
Following each read event, a worker brings the handheld unit to a PC or a laptop and plugs it in via a USB port. All of the culled sensor data is then uploaded to Shimmick’s server.
To date, Marrow says, the system has been able to determine that concrete has adequately cured within about two weeks after it is poured – approximately half the time the company would have had to wait without the sensor data. Since the solution’s installation at the onset of the three-year project, Marrow says “It’s paid for itself three to four times over” based on the reduced wait times. During the next phase, Shimmick Construction plans to utilize the tags and readers to monitor the curing of concrete poured for bridge support pilings.
Wake Inc. has provided some upgrades to the software since the system was put in place, Marrow reports. Any shortcoming, he says has come from the destruction of several tags that could not survive becoming wet (when it rained, for example) for a long duration. That, Marrow notes, was the result of the tags not being submerged in the concrete, as they were designed to be. Wake now offers a treatment that can be applied to the tags which allows them to be completely submerged in water for an indefinite amount of time.