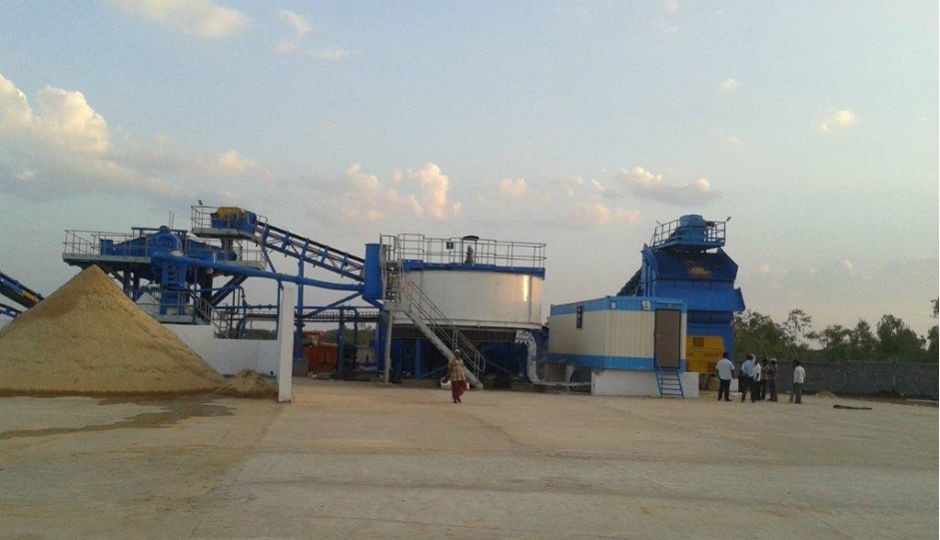
Sand is essential in the manufacture of almost all items we see around us, for example, buildings, roads, glass and cast or molded iron and steel items or glass. It is a compound of iron and silicon, forming almost 70 percent of the earth’s crust. Sand takes different forms in different rock types such as granite, basalt or limestone and thus the sand produced from them have properties suitable for particular applications.
The production of foundry sand requires specialist screening and classification systems and involves detailed analysis of feed material and sand grade specifications. Foundry sand (also known as casting sand) consists primarily of clean, uniformly sized, high-quality silica sand that is bonded to form molds for ferrous (iron and steel) and nonferrous (copper, aluminum, brass) metal castings.
The most common casting process used in the foundry industry is the sand cast system. Virtually all sand cast molds for ferrous castings use green sand. Green sand consists of high-quality silica sand, bentonite clay (as the binder), water and coal (a carbonaceous mold additive to improve casting finish). The type of metal being cast determines which additives and what grade of sand is used.
There is strict specification for the sand to be used in the foundry application and this is given in the table below:
Property | Range |
Silica Content (SiO2) | 90% (Minimum) |
Particle Size | -600 +100 microns |
Grain Fineness | Range from 45 to 90 AFS |
From the table above it is clear that particle size range is the most important criteria for the sand for foundry and also that it should not contain clay. If required the silica content can be enhanced thorough certain processes.
CDE has a high level of expertise in the production of sand for foundry application, developing its own screening and classification technology. CDE have developed a process for accurately separating the oversize particles and removing clay though the hydrocyclone based washing system, which could be either single stage or double stage depending on the level of clay present. Finally the product is dewatered in the highly efficient dewatering screen resulting in a dewatered product having around 12 percent moisture. In most instances scrubbing is also necessary to release the clay which is bound to the ore. This is usually done through drum scrubbers and attrition scrubbers either before or after screening of the raw sand. During these processes the silica levels in the product is also enhanced.
“CDE has supplied a number of plants in India for the preparation of foundry sand all of which are operating successfully. The added advantage of these plants is that the oversize of the screen (+600 micron) can be used for construction sand as all the silt has been removed. This makes our plant highly cost effective. The plants are also highly flexible and could be suitably modified by addition of scrubbing and gravity separation equipment to convert into plants for glass sand preparation if suitable raw material is available,” said Dr Arabinda Bandyopadhyay, President of Technology & Business for CDE Asia.