New Cat 16M3 Motor Grader Configures to Meet Engine Standards Worldwide
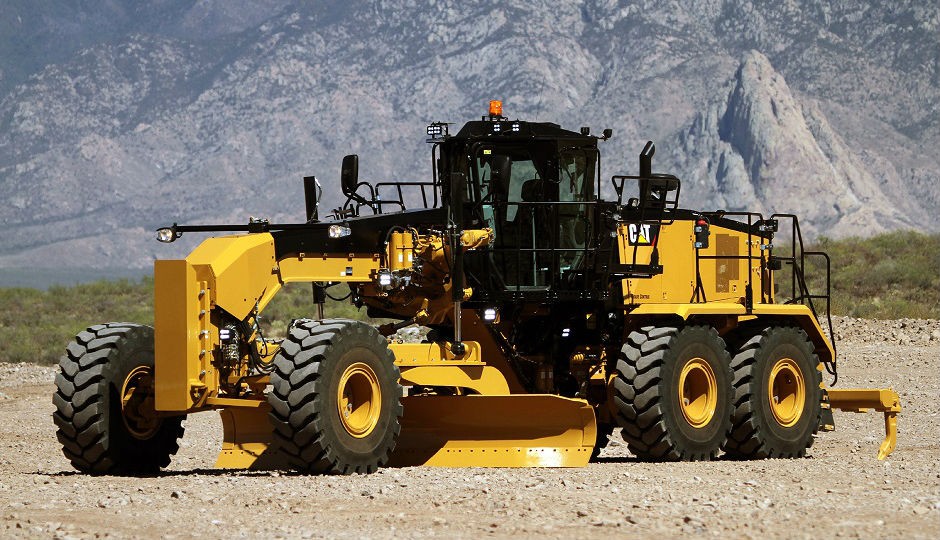
The new Cat 16M3 Motor Grader features engineering enhancements that boost fuel economy, increase structural durability, simplify maintenance, add operator convenience and promote the safety of both the operator and those around the machine. The 16M3 is available in configurations to meet engine emissions standards worldwide.
The 16M3 motor grader is an essential machine for building and maintaining mine haulage roads – to keep trucks running most efficiently and at the lowest cost per ton of material moved. The 16M3 has a 16-foot (4.9-m) moldboard and an average operating weight of 71,454 pounds (32,411 kg). The motor grader is optimally sized for operations using 150-ton (136-tonne) or smaller trucks.
The 16M3 features a Cat C13 ACERT engine with the Cat Optimized Variable-Horsepower system, which provides net power ratings from 290 to 348 horsepower (216 to 259 kW). The engine is available in three configurations to satisfy global emissions standards: U.S. EPA Tier 4 Final/EU Stage IV/Japan 2014 (Tier 4 Final); Tier 3/Stage IIIA /
A new ECO mode, standard for Tier 2 equivalent and Tier 4 engines, is designed to improve fuel economy by optimizing engine speed to 1,900 rpm in working gears when possible with no compromise in performance. This operator-selected feature delivers fuel savings estimated to be as much as 4 to 5 percent, compared with working in comparable light- to moderate-load applications with the system deactivated. An additional engine control system feature provides consistent power to the ground by continually adjusting the engine to compensate for power losses to the cooling fan.
Also new for the 16M3 is the “
Drive train and structures
The Cat direct-drive, power-shift transmission, with eight forward and six reverse gears, incorporates the Cat Advanced Productivity Electronic Control Strategy (APECS) system, designed to smooth gear changes and promote productivity. The modular trans-axle now has a standard automatic differential lock, which ensures appropriate locking/unlocking for optimum traction and maneuvering, thus averting possible damage from ill-timed manual control.
The 16M3 also features nearly 15 percent greater dynamic braking torque at the rear tandems, achieved by enlarging both the brake disc diameter and the piston area. A new manual brake wear indicator simplifies disc wear measurement, eliminating having to remove the brake pods to check wear.
The 16M3 front frame, hitch area, and rear frame have been specifically designed to ensure long-term durability with the added weight and power of the new model. The centre-shift section is now a heavy-duty steel casting designed to effectively distribute stress and enhance durability in this highly loaded area of the mainframe. The rear frame is lengthened, incorporating two bumper castings for added counterweight, and the hitch plates (at the articulation joint) are 50 percent thicker than those of the 16M. The longer frame improves machine balance and steering control and provides easier access for routine maintenance.