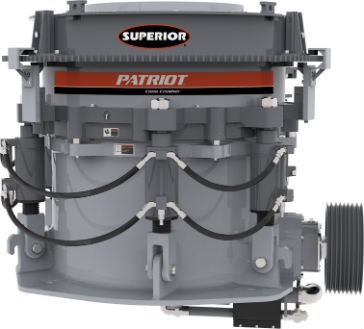
Superior Industries, Inc. has debuted their brand new Patriot Cone Crusher, marking a major milestone for the company’s new crushing and screening division. The high-performance cone is the manufacturer’s first entry into crushing technologies for bulk processing applications.
“In the months leading up to the launch of our first crusher, we have worked hard to arm ourselves with a group of bright, experienced crusher service and parts professionals to provide our customers with world-class support,” said John Garrison, Superior Director of Crushing and Screening. “In addition, each Patriot Cone Crusher will be backed by the industry’s first two-year standard warranty and is manufactured in the United States at our new Pekin, Illinois-based factory.”
Besides a strong commitment to service and convenient access to wear parts, the Patriot Cone Crusher will be recognized for rugged structural integrity and high-grade components to extend service life. Internally, bronze sleeve bearings are used for all moving components that are load bearing or perform load transmission (including counter shaft bushings, thrust bearings, head and eccentric bushings and socket liners). In addition, these critical components are cast of high-grade steel, which typically exceeds standards for conventional cone crushers.
Superior says engineers uniquely designed high throw and high-pivot point crushing performance to achieve strong production rates at a low cost per ton. Mobile applications will appreciate a readily mounted design for transportation on a cone/screen chassis.
For protection from costly structural damage, each Patriot Cone Crusher is equipped with fail-safe hydraulics to defend the unit against damaging mechanical overload. Additionally, standard relief valves within the dual acting tramp release cylinders provide immediate, alternative protection should the accumulator fail. Engineers also developed overload sensing technology. In the event of force overload, a simple alarm can activate or optional advanced sensing technology will automatically take the necessary corrective action. This same automation can control the feed rate to optimize performance, adjust other settings and monitor critical lubrication and hydraulic parameters.
Models include units for 200 to 500 horsepower operating conditions and production rates up to 805 tons per hour (730 mtph).