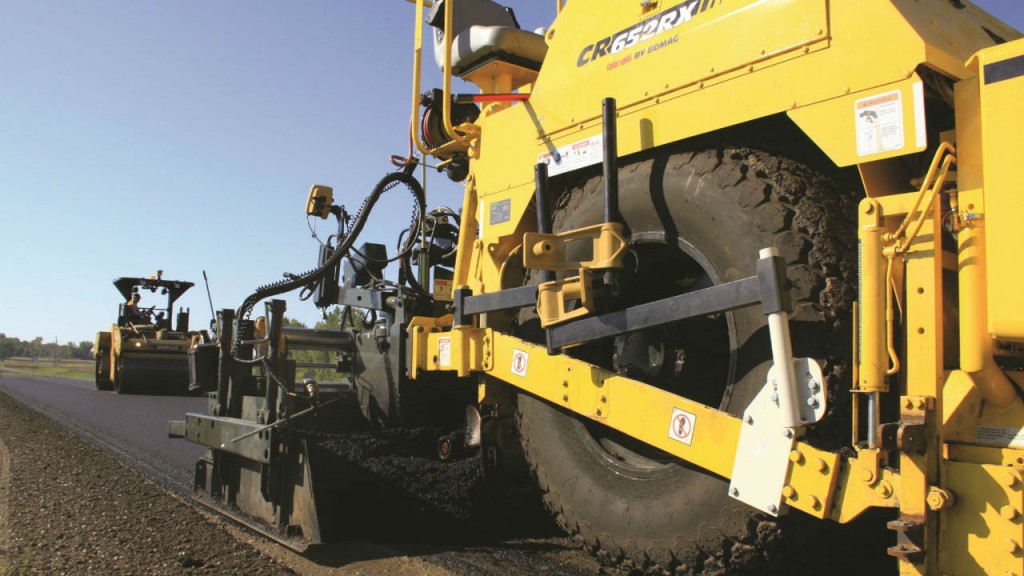
Properly paving and compacting the longitudinal joint has plagued the asphalt industry for decades. If not constructed and compacted properly, it is a weak point in the new road – the first failure point.
However, there is a way to eliminate the cold joint entirely: full-width paving.
“If the right conditions exist, I’m a big proponent of full-width asphalt paving to eliminate the longitudinal joint between the travel lanes,” says Bill Rieken, road building specialist for Bomag. “You are eliminating a potential weak spot in the road and you can significantly improve the mat’s quality, while reducing paving time.”
Full width refers to paving at least 8.5-m wide in a single pass, Rieken explains. This allows for paving of two 3.7-m-wide travel lanes, plus a small shoulder. It eliminates the joints between travel lanes, and between the travel lane and the shoulder.
Removing this cold joint enables the paving contractor to achieve compaction density and smoothness more readily across the entire mat width. Eliminating additional passes with the paver increases paving efficiency, reduces the time required to pave a project and improves the longevity of the road.
Key conditions for full-width paving
While full-width paving offers several significant benefits, it’s not quite as easy as just deciding to pave all roads full width. Certain conditions must exist, like the ability to shut down a two-lane roadway to traffic so it can be paved in one pass. It also requires careful planning.
“You will use more material in the same period of time, so you must first consider your asphalt production needs,” Rieken says. The paving crew will potentially lay in excess of 450 tonnes (500 tons) of asphalt per hour, so the asphalt plant must have the dedicated production and storage capacity required.
“A contractor may have to pull material from two different plants if one plant cannot supply enough material,” adds Tom Kiselica, road building specialist for Bomag. “All the components of the project, from plant production to trucking to the paving equipment to the rollers, must work in concert together to deliver a successful full-width paving project. The paving train must move along consistently. If the plant doesn’t have the capacity to keep up or not enough trucks are planned for delivery, the quality can suffer.”
Trucks
Trucking is the vital link between the plant and paver, and the contractor must have the right number and type of trucks to ensure continuous quality paving. Fortunately with the road closed to vehicles, traffic congestion and truck transit time often isn’t impacted as much as when the trucks have to dodge in and out of traffic to deliver asphalt with partial lane closure projects.
End-dump trucks are the least preferred transport method since they are little more than a rectangular box, allowing the mix to segregate as particles roll to the truck’s sides and ends.
“Live-bottom trucks are preferred for their “V” shape to reduce particle segregation,” Rieken says. “Plus, they offer faster unloading into the hopper of the paver or material transfer vehicle, which helps to increase truck exchange efficiency and improve continuous paving efforts.”
The right screed
A key equipment component to a successful full-width paving project is selecting the right screed. The number of crown points can determine the type of screed required, either hydraulically extendible or inline fixed-width. Typically, there will be different crown points between the shoulder and outside lane, in addition to between the travel lanes.
With a hydraulically extendible screed, contractors must work with the manufacturer to make sure crownable extensions are available to accommodate the crown point at the shoulder.
According to Henry Polk, paving product marketing manager for Bomag, most often contractors will purchase a fixed-width screed specifically for paving full-width projects, “They will often set up an inline screed at the yard to meet the road’s profile and ship it to the jobsite so it can be pulled off the trailer and attached to the paver.” The efficiency gains and cost savings associated with paving in a single pass more than offset the additional cost of having a dedicated screed for full-width paving, he says.
The benefit of a fixed-width screed stems from the variety of attachments offered so that a contractor can configure the paving width to meet specific project needs. It is important to make sure that the manufacturer offers slopeable extensions to accommodate the crown points at the shoulder.
Paving at extended widths exerts more forces on the screed than if the paver were paving at 3.7-m widths; Rieken recommends some adjustments so that the screed will be able to handle these extra forces.
“The manufacturer and/or distributor will work with the contractor to ensure the appropriate bracing and ballast is added, so [that the screed] has the necessary structural integrity and proper ground contact pressure to withstand the added force of paving full width,” Rieken says.
Paver selection
The paver will be pulling a much heavier load when paving at full width; therefore, contractors must select a paver that offers a combination of power and traction to efficiently perform full-width paving. Either track or tire-drive systems can be used. For the latter, Rieken advises contractors to carefully consider drive-tire size to help with traction, such as a Cedarapids CR500 or CR600 Series mainline paver which has the largest drive tire available on a paver. A rubber-track-drive system, as used on the RoadMix, provides the traction required for full-width paving and spreads the weight of the fully loaded paver over a larger area to prevent rutting of the subbase on base course.
Preventing segregation
The RoadMix has two sets of two counter-rotating augers with a variable-pitch design that pulls material from all areas of the hopper and aggressively re-blends 100 percent of the asphalt prior to delivering it to the screed’s spreading augers. The end result is a more homogeneous blend of asphalt delivered to the screed, which is void of both material and thermal segregation.
The slat delivery system of a traditional paver provides asphalt movement from the front of the hopper to the rear, so any form of thermal or particle segregation of the mix in the truck will be transferred to the mat, according to Bomag.
“We are talking about increasing quality and efficiency through full-width paving,” says Kiselica. “While it is possible to pave full width using a traditional paver, why not give your crew the best chance for success by giving the material a final remixing to eliminate any segregation that may have occurred at the plant or in transit to the jobsite?”
Material transfer vehicle
While it is possible to complete a full-width job by using just the paver to accept material from the truck, most contractors will add an MTV to the paving train. This gives extra surge capacity to maintain continuous paving even when there is a transport issue with material to the jobsite or a truck exchange problem. Additionally, some MTVs provide asphalt remixing to address segregation.
“The benefit offered by our RoadMix,” explains Polk, “is that it can be used both as an MTV or a paver, so it gives contractors additional flexibility at the jobsite.
“Its track drive lowers ground contact pressure to less than 21 psi fully loaded as an MTV so it can be used on the critical base lift without the fear of rutting associated with MTVs using a tire drive system. Additionally, the CR662RM delivers the same asphalt remixing benefits when equipped as an MTV as it does as a paver.”
Compaction
Paving contractors may have to anticipate doubling the rolling crew to match the increased mat width.
With the largest mainline rollers offering compaction widths of 2.135 m, contractors will often choose to put two compaction trains – breakdown, intermediate and finish rollers – behind the paver.
“One rolling crew will be dedicated to achieving spec densities for one travel lane and the other will roll the remaining travel lane and small shoulder,” says Bert Erdmann, product manager, heavy compaction for Bomag. “This will allow the rollers to keep up with the paver and perform their compaction tasks at the right temperature range.”
Significant benefits
Full-width paving yields high dividends for the contractor and travelling public. First and foremost, the road is closed to traffic giving the contractor complete control of the construction site. This eliminates car and truck traffic travelling at high speed adjacent to the paving area, resulting in significantly improved safety for the work crews.
Paving full width eliminates the weak longitudinal joint running down the centre of the road, boosting the road’s longevity and quality, and saving the contractor the time and effort associated with rolling an unconfined edge and cold joint. This enables the contractor to achieve smooth profilograph readings across the entire mat width and to better meet compaction densities without the drop-off at the joint.
Finally, full-width paving allows the road to be finished more efficiently, in less time, with fewer passes and lower cost. Reducing the time it takes to pave the road allows the road to be opened to the travelling public sooner, which makes everyone happy.