Large drum diameter on the new BOMAG BW206AD-5 tandem vibratory roller improves surface smoothness
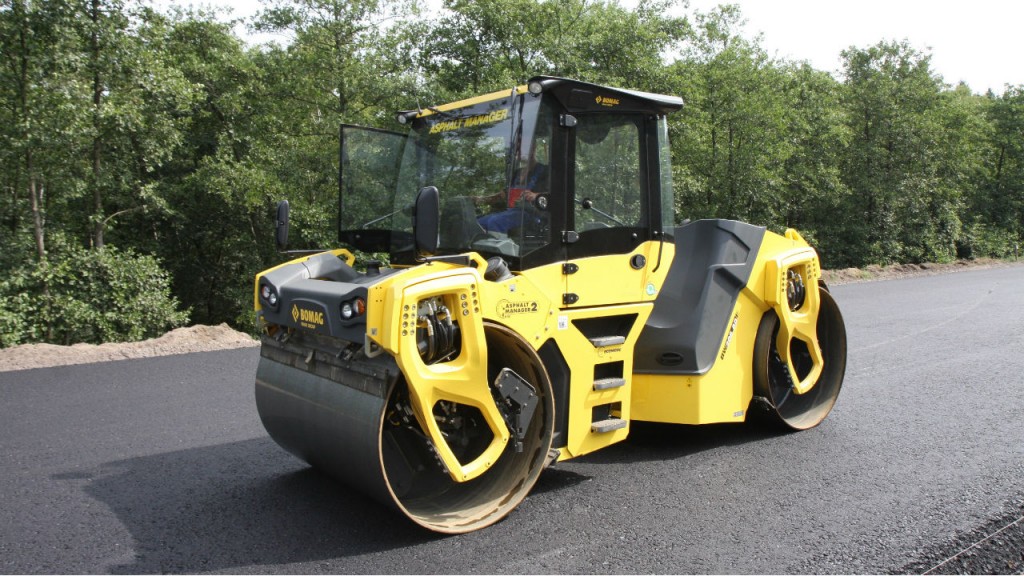
The new highway class BOMAG BW206AD-5 tandem vibratory roller boasts a larger, 55.1-inch (1,400-mm) drum diameter than previous 84.1-inch (2,135-mm) drum models to deliver a smoother finish and improve mat quality. Its large drum diameter puts more impact surface area in contact with the asphalt to help prevent mat pushing and shoving and eliminate the potential for bow waves in front of the drum, even when working at higher speeds on tender mats.
The “leg design” BW206AD-5 roller extends the length between the drums, while reducing overall machine length compared to the perimeter frame roller it replaces in the BOMAG line, allowing operators to work more easily in confined areas. The vibratory roller also offers 66 percent higher curb clearance, increasing flexibility when compacting around obstructions. The roller’s available crab walk steering mode offsets the front and rear drums by up to 6.7 inches (170 mm) to the left or right, allowing the BW206AD-5 to easily compact right up to structures.
The new BW206AD-5 asphalt roller offers two vibration frequencies and amplitudes, significantly increasing flexibility in matching compaction output to the application. Low frequency and amplitude of 3,000 vpm (50 Hz) and 0.031 inches (0.78 mm) respectively deliver maximum compaction output of 39,116 pounds (174 kN). The roller’s high 4,200 vpm (70 Hz) frequency delivers more drum impacts per inch when rolling at higher speeds than the previous model to improve surface smoothness.
The new roller can be economically equipped with BOMAG’s exclusive ECONOMIZER compaction measurement system that delivers real-time compaction progress to the operator’s console. With ECONOMIZER, the operator knows when material stiffness is optimized, saving time, fuel and money by eliminating unnecessary passes. More importantly, ECONOMIZER allows the operator to identify and correct “soft” spots in the mat, and it prevents over mat compaction and aggregate fracturing.
Powered by a fuel efficient, 140-hp (105-kW) diesel engine using a combination of EGR and SCR emissions reduction technology, the BW206AD-5 tandem roller meets stringent Tier 4 Final standards.
Exclusive ECOMODE operation allows the new BOMAG BW205AD-5 tandem vibratory roller to offer 8 percent higher engine horsepower than the roller it replaces, while significantly saving on fuel consumption. When set to ECOMODE operation, the engine reacts to low load situations and automatically de-rates engine output to match need, and it automatically shuts off the engine after a pre-assigned period of idle time. With BOMAG’s ECOMODE operation, the roller delivers up to 30 percent fuel savings over full power mode and offers quieter machine operation to boost comfort.
The new BW205AD-5 roller is built with a larger platform for increased legroom and greater operator comfort than with the previous model, and an optional ROPS cab with heating is available. For increased visibility to the machine’s front, rear and sides, the roller features a single sliding, swiveling operator’s seat. The suspended seat with integrated travel lever slides effortlessly along a back rail, while it swivels 180 degrees to give operators direct line visibility to the drum’s edge. The console swivels along with the seat, so the controls and display are always in the same position relative to the seat.
Designed with the service technician in mind, this new BOMAG roller minimizes maintenance to maximize machine uptime. A no-grease zerk design eliminates the need for daily lubrication, and all maintenance points can be easily reached from ground level. A departure from typical “leg design” rollers, the engine compartment is located on the rear frame, offering unobstructed access to service components.
Two independent pumps operate the interval-timed and pressurized water spray system that extends operating time required between refilling the polyurethane water tanks. Visible to the operator from a seated position, the system’s spray bar and nozzles are wind-protected to ensure uniform coverage, while a quick disconnect nozzle design helps to quickly clear plugging. Two spring-loaded flexible polyurethane scrapers per drum evenly distribute water across the drum and keep the drum clean.