Atlas Copco launches next-gen bucket crusher attachments at Bauma
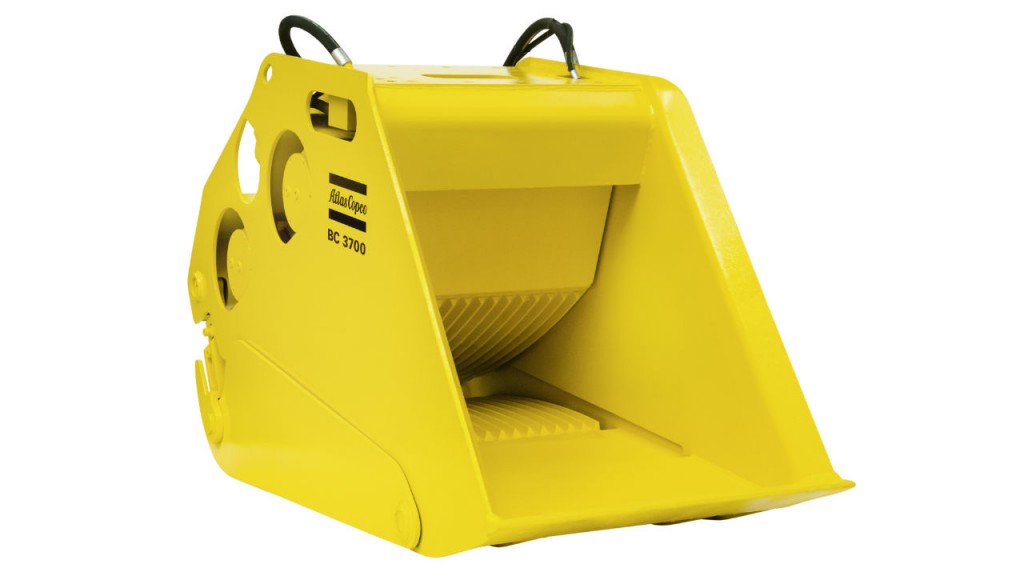
Atlas Copco Construction Equipment has introduced its new generation of bucket crusher attachments that offer higher output and greater reliability than previous models. The new bucket crushers – the BC 2500 and BC 3700 – process about 80 percent more material due to their hydraulic drive system. The BC 2500 fits 24- to 33-ton carrier weight classes, and the BC 3700 fits 30- to 42-ton carrier weight classes.
Atlas Copco debuted the new bucket crushers April 11-17 at booth 1108 during Bauma 2016 in Munich, Germany.
“The new bucket crushers allow contractors to increase the versatility of carriers, especially on demolition, recycling and road construction applications,” said Rich Elliott, Atlas Copco product manager, hydraulic attachments. “The powerful drive systems and high reliability make them an ideal alternative to mobile jaw crushers for cramped worksites. Plus, they can process a wide range of materials, including aggregate, asphalt and concrete.”
The attachments feature powerful components that allow carrier operators to crush as much as 110 tons of material per hour. The drive system – two hydraulic motors and a timing belt – generates the high torque needed for powering the crushing jaw. The attachments also feature a reverse function to easily remove any blockage by pushing material back through the inlet.
Crushing material on site allows contractors to save on transportation costs to a landfill or processing centre since they can fit more material in each truckload. They can also reuse the crushed material on site as backfill, which reduces the costs associated with hauling in material.
Atlas Copco designed the attachments for high reliability and maximum uptime in challenging worksite conditions. For example, Atlas Copco’s internally mounted drive system eliminates protruding components to minimize the risk of dust entering the hydraulic system and to protect key components from flying debris. Additionally, operators can control the diameter of the crushed materials by easily adjusting the jaw outlet without any special tools. This keeps setup times to a minimum and allows operators to create varying material sizes.