Cedarapids CR662RM Tier 4 Final RoadMix MTV and paver advances durability, improves operator comfort
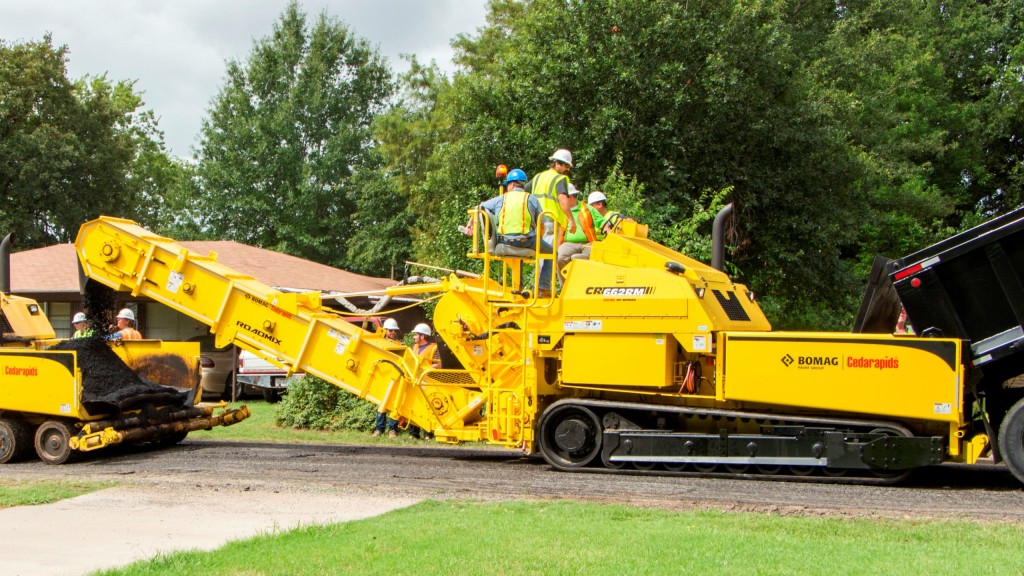
Designed as both a material transfer vehicle (MTV) and paver to significantly increase utilization rates, the rubber track Cedarapids CR662RM RoadMix from BOMAG features a new 260-hp (191-kW) Tier 4 Final Cummins diesel engine that delivers the power needed for high production applications. Boasting a low, 21-psi fully loaded ground contact pressure, the CR662RM can be used on all paving lifts, including the critical base layer, to virtually eliminate all forms of material and thermal segregation. Unlike MTVs with empty wheel loads in excess of 75 psi, the low-psi rubber track RoadMix machine does not cause rutting on the base layer, can cross bridges fully loaded and is transported to the jobsite like a 10-foot paver, so contractors can finish mainline and airport paving applications quickly, efficiently and with high mat quality.
Replacing the traditional in-hopper slat delivery system, the improved Remix Anti-Segregation System delivery augers now feature hard-faced back sides to significantly increase wear life. The two sets of two variable-pitch, counter-rotating augers uniformly draw down material from inside the hopper to aggressively remix 100 percent of the asphalt to combat segregation at the jobsite. Auger pitch spacing transitions from 10 inches (254 mm) at the front of the hopper to 12 inches (305 mm) at the rear to quickly channel material to the transfer conveyor or screed. This design results in throughput capacities in excess of 600 tph (500 t/hr) whether equipped as a paver or MTV.
A new platform design increases the operator’s line of sight to the RoadMix’s sides, enhancing comfort and productivity. The operator’s seat now pivots beyond the machine’s side for unimpeded track visibility, while the revamped operator’s console also pivots to line up with the seat. A sloped engine hood improves the operator’s sightline to the hopper. The generator powering the electric screed is now positioned away from the screed, lowering sound levels to the screed operator’s ears to further improve comfort.
Whereas most MTVs sit idly by more than 75 percent of the time, the unique CR662RM RoadMix design substantially improves a contractor’s return on investment. In less than four hours, crew members can quickly remove the rear conveyor assembly used for transferring material from the tractor and replace it with the screed assembly. “If necessary, a contractor could pave with the RoadMix in the morning and use it as an MTV in the afternoon,” says Henry Polk, product marketing manager – paving products for BOMAG. “This is one machine that will rarely sit in a contractor’s yard.”
The Cedarapids CR662RM RoadMix now comes standard with three years of complimentary BOMAG Telematic service. BOMAG Telematic monitors machine vitals, delivers text and email alerts to key personnel, reminds the dealer and service technicians when scheduled maintenance tasks are due, and offers a number of productivity reports to help maximize machine utilization. “Even at full load,” adds Polk, “Telematic is showing us that the CR662RM uses only an average of 5 gallons (19 litres) per hour.”
Smartrac technology extends the CR662RM RoadMix’s track life, warranted for three years/3,000 hours. Oscillating bogie wheel assemblies combine with the system’s frictionally driven rubber tracks to automatically apply the correct tension to the track, regardless of travelling in forward or reverse. The self-tensioning system does not over-tension the track, significantly prolonging track life.
When equipped as an MTV, the CR662RM’s 30-inch (762-mm) wide conveyor offers a discharge height of 73.2 to 115.8 inches (1,859 to 2,941 mm) for non-contact paving and swivels 55 degrees left or right of centre for off-set paving. For mainline paving, the CR662RM can be equipped with either the Stretch 20 or Fastach 10 screed and is capable of paving at widths reaching up to 30 feet (9.1 m). Two independently controlled, variable-speed outboard drive motors eliminate the need for the spread auger centre gearbox drive to reduce the occurrence of centreline segregation.