Terex Minerals Processing Systems to launch ‘Making New Tracks’ large mobile plant strategy at MINExpo
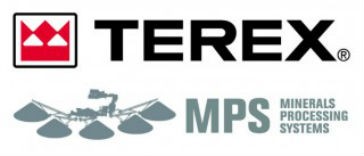
Terex Minerals Processing Systems (MPS), will launch its ‘Making New Tracks’ large mobile plant strategy in North America at the forthcoming MINExpo International Show in Las Vegas, on 26 – 28 September 2016 at Booth 3379.
Terex MPS Market Area Director for Americas, David Quail, commented: “We are excited to be able to launch this new product strategy at MINExpo. We have three new large tracked mobile plants which enable Terex MPS to diversify further from our modular, portable and static offerings. With over 100 years in the industry we now have a strong product portfolio offering customers from a wide range of industries, cost effective solutions for the long term”.
LJ5532 – large tracked jaw plant
The LJ5532 has the world renowned Terex JW55 single toggle heavy-duty jaw crusher mounted on a tracked chassis. This hydraulically adjusted jaw crusher, requiring no shim packing, allows the CSS of the jaw to be adjusted in a matter of seconds.
This highly mobile jaw crusher boasts an advanced, user friendly, control system and an efficient hydrostatic drive, which allows the end-user to vary the jaw speed on the fly and even run the jaw crusher in reverse as per particular application demands, such as recycled asphalt. The powerful hydraulic drive can also be used to unblock the jaw if the plant has been shut down fully loaded.
The LJ3255 features an independent prescreen, located before the crusher, which helps bypass or remove any undersized material or feed material that has a high content of dirty fines, thereby promoting maximum throughput performance from the jaw crusher as well as enhancing the heavy duty manganese wear life.
This impressive tracked plant is run by the proven Scania DC13 Tier 4 water-cooled diesel engine, and is transported in one load. Below are just some of the key optional features available with this plant:
- A hydraulically folding, telescopic bypass conveyor, which is mounted below the independent prescreen. This conveyor, which has an exceptional discharge height, allows the prescreened material to be stockpiled off the side of the plant.
- Heavy-duty, high-strength, cross belt magnet conveyor. Which helps remove any steel contaminants from the discharge conveyor before the material is passed onto the next processing stage.
- A radio remote that can be used to track the plant as well as starting and stopping the crusher feed from the cabin of the feeding excavator.
LC450 – large tracked cone plant
The LC450 incorporates the world leading Cedarapids MVP450X all roller bearing cone crusher. The MVP450X cone crusher is well known in the industry as being unmatched when it comes to producing high spec products, with exceptional shape, with output capacities that leave all competition in its wake. The cone crusher also includes a hydraulic, maintenance-free, anti-spin device that helps improve cone liner wear life, as well as a hydraulic tramp overload protection system, TIR, that helps clear the crushing chamber of any potential tramp metal that may have entered the crusher with the feed material.
The LC450 tracked cone crusher also incorporates an automated metal detection system, located on the heavy-duty feed conveyor, which stops the conveyor before the metal contaminant reaches the crusher. The plant also has the patented metal purge system that dramatically reduces downtime when removing the metal contaminate from the feed conveyor.
The MVP450X Cone crusher is driven via V-belts by the powerful Caterpillar C18 Twin Turbo engine. The crusher eccentric speed can be adjusted, via the engine rpm, to best suit the given application and feed material.
The plant also features a cone hopper level sensor, which can be controlled via the plant control system, which is used to regulate the speed of the feed conveyor to ensure that the feed hopper above the cone crusher is kept consistently full. The process is made far more convenient with the onboard video camera, mounted above the cone crusher, giving live images of the material entering the chamber.
LV2050 – large VSI tracked plant
The LV2050 is a high capacity tracked Rock on Rock, ROR, Canica 2050 VSI crusher, which features the new patent pending hydraulically controlled dual flow system. The Dual Flow system helps elevate the crusher’s throughput capacity without increasing the overall drive power.
This large tracked Vertical Shaft Impact Crusher utilizes the same chassis and powerunit as the LV450.
The New Canica 2050DF VSI “broke the mold” when it comes to throughput capacity, superior product quality and all-round product control. The heart of the VSI is the 6 port heavy-duty closed rotor. The rpm of the rotor is controlled by changing the engine speed. The crushing chamber’s rock shelf is easily accessed through the side door, which also helps speed up maintenance checks on the rotor.
This impressive tracked VSI is ideal for applications that demand the best product shape and quality, with a throughput capacity that can only be admired.
Quail added: “The new product lines being launched in North America will serve an increasingly diverse range of materials handling sectors. The AggreScalp unit brings operators a well-proven, cost-effective and durable machine in a modular all-electric format. This is ideal for C&D recycling applications as well as quarry and mine overburdens and integrates seamlessly with other key TWS systems including AggreSand and AggreScrub. The UltraFines will tackle the increasing demand for fines recovery within numerous facets of the washing industry.”