Data collection ushers in a technology revolution in roadbuilding
The data revolution will benefit those who embrace the changes – and leave behind those who don’t
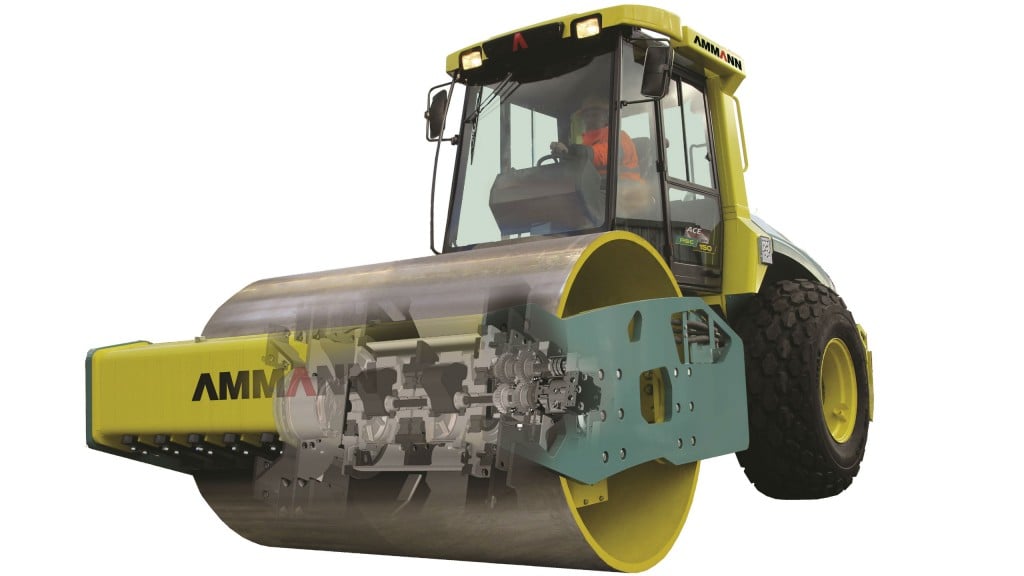
If the technological revolution could be described in a single word, it would be “data.” More jobsite information is being gathered, stored, documented and analyzed than ever before. Adding a bit more description beyond “data,” the phrase “real time” would be most appropriate.
We have hard information on what is happening right now. That knowledge enables jobsite adjustments that lead to better machine utilization, reduced fuel consumption and dramatic quality improvements.
The associated cost savings are enormous, and those who don’t take advantage of the opportunities will increasingly be unable to compete in the construction industry.
This particular transformation is the result of combining advances in telematics (the use of data) with machine control (real-time response to that data on the jobsite – in particular, machine positioning).
What machines does this apply to? In road building applications, we’re typically talking about soil and asphalt compactors. Yet other machines – pavers, graders, dozers, excavators, haul trucks and more – are now playing a role. Their emergence is yet another significant development.
Currently the data is transmitted, stored and analyzed elsewhere – typically in the cloud – and used to optimize machine utilization. To be more specific, let’s now define telematics as collecting data, then organizing it for site management and machine monitoring, and finally using it to optimize the working machines.
Machine control, meanwhile, is defined as monitoring and controlling machines and processes “locally,” which means on the jobsite.
Local control means machines can ‘talk’ to each other
Communication is essential to local control. The machines need the ability to talk to one another. As they gather the data, it is processed and its relevance quickly communicated to the adjacent machine, which can adjust based on the success (or failure) of its neighbours.
For example one roller can tell another, “I’ve already covered this area, but no one has been over there.”
This communication is done in real time, which is significant. Adjustments can be made immediately, instead of having to go back to the office and dump data into a spreadsheet to spot trends and opportunities. Those adjustments aren’t just for tracking machine movement but also to position the blade, bucket, screed or drum.
It began 40 years ago with such things as compaction meters
It took decades to arrive at such an advanced stage of telematics and machine control. Many consider the mid-1970s launch of compaction meters as one of the first key compaction control events. Entering the market a few years later were products that could print and analyze data to improve processes.
While this documentation was a big step, the information was gathered on the jobsite and reviewed much later. It was helpful in determining best practices for the future, but of limited immediate value.
There were some tiny steps forward, but a leap occurred in the late 1990s with the launch of measurement and control systems like Ammann Compaction Expert (ACE). This was significant because it provided indications – though certainly not proof – that compaction had been achieved. It also led to adjustments that could be made more quickly than before and provided a host of cost-saving measures.
The real-time feature was not yet present. It is a relatively recent addition, having arrived with mobile phone and GPS technology. The mobile technology made it possible to have remote access to a moving machine, while GPS improvements could precisely locate a machine in real-time.
Now simpler to use and maximize production
Today we are in a later stage of adopting the technology. Now, for example, the technology can be modified to precisely fit customer needs; previous technology was too inflexible. Today’s systems are easily adjusted yet bring new levels of consistency, too.
The interfaces also are important. Previous technology often overwhelmed operators with information. Now it shows only what is needed. In some cases, it’s amazingly simple with a green light meaning “go.”
What’s essential is that the operator remains the master of the jobsite. He or she is now able to maximize productivity and make sure the machine and the technology are working in unison. This is easier than ever to accomplish, but certainly maintains the relevancy of operators. They are the ones who turn the technological investment into cost savings.
Useful for small contractors
Not too many years ago smaller contractors saw the technology as something meant only for larger businesses. The theory went that bigger jobsites and fleets were required to make the technology worth the investment.
It was a different story for smaller contractors.
They were less likely to pay for “experimental” technology that would require lengthy training and, as some initially believed, few quantifiable benefits.
Improved telematics once again changed that by providing hard numbers on fuel and labour savings, passes avoided, and a host of quality control efforts. Those matter every bit as much to small contractors, too.
Companies like Trimble realized this from the start. They spent a significant amount of time and money developing products for smaller contractors. The theory was that the percentage of savings mattered more than the dollar amount, and it made sense. A savings of, say, 20 percent makes a difference whether you’re operating a single skid-steer machine or a fleet of rollers and pavers.
Trimble also understood that local (on the jobsite) control and real-time communications come into play for smaller contractors, too. General contractors increasingly will want subcontractors connected to the larger fleet.
The percentage of smaller contractors using the technology is rising, and that number will continue to grow. Governments are slow to adopt change, but some are beginning to require the use of this technology. It eventually will become the norm when bidding on jobsites, whether you’re a large or small contractor.
What to expect in the future
Machines will continue to improve their data gathering, which ultimately will lead to process improvements that will make the industry even more efficient. Data on how machines previously performed in certain applications and conditions will be readily available, from the initial bidding through the final production on the jobsite.
The communication between the machines will improve as well, which will be necessary to take advantage of all the data being gathered in real time.
It stands to reason that machines lacking this communication capability will be phased out of jobsites.
This need for communication creates another significant requirement: machines built by the fiercest manufacturing rivals will need to talk to one another.
The reality is jobsites feature contractors who prefer varied brands. If machines aren’t able to communicate across brands, the benefits will be minimized.
Such a communication problem also would make some contractors less competitive. For example, if a contractor used Brand A, and can only talk to Brand A machines, his bid might be passed over in favor of a contractor who uses Brand B, which can communicate with any and all machines.
Data is most helpful when used across multiple phases of a project
A grader needs to talk to a soil compactor, and a paver to an asphalt compactor – and many other combinations including excavators, motor graders and even skid-steer loaders. The use of all these various machines, and their need to communicate, makes it even less likely that only one brand would be represented.
It then follows that the tools for collecting this information will become standardized. The devices on each machine might be a bit different, but all will collect similar data and communicate in real time. That means the hardware will be mostly standardized as well, and integrated into the machines.
Hardware integrated into machines by the manufacturer
The first of the three components to telematics is a machine with the proper hardware to collect the data. (The second is the communication of the information to the cloud, and the third is the cloud itself – including the interface that makes that information useful.)
At the moment, many machines utilize hardware from Trimble or Topcon. We see the future as having the hardware integrated into the machine by the manufacturer. Ammann hardware will be built into every Ammann machine.
This evolution is actually good for companies such as Trimble and Topcon. They will continue to partner with manufacturers to develop the hardware. But the biggest opportunities lie in the processing, documenting and analyzing of the data – the parts of the equation that come after the hardware.
All data will go to the cloud, and how it is made useful from there – in the easiest manner possible – will be how these companies thrive in the future. The real opportunities for companies such as Trimble will be developing the interface that makes the raw data useful.
Contractors shouldn’t expect to see dramatic cost savings from standardized hardware. Yes, the hardware likely will cost less, but the customer will pay more for data-related services. Think of your mobile phone: over time the purchase price is much less than what is spent on monthly service.
Governments will have a role in the future as well. As they catch up to today’s technology, governments are likely to increasingly require the use of telematics for a contractor to participate. Once again, we’re in a situation where various brands will have to set rivalries aside.
There have been some starts and stops. Some governments began such a process and took a step back, often for legal reasons. But rest assured, these mandates are coming. Governments want to have the information, such as compaction data, to improve their processes and increase the life of roads.
Even further down the road
At Ammann, we see the future as connecting more steps of the process, particularly asphalt plants. For example, if an asphalt compactor was falling behind, it could communicate to the paver – and ultimately the plant – that mix production should be adjusted.
Autonomous machines – essentially those that don’t require an operator – are on the horizon, if still a bit of a distance from arriving. There are many interesting developments but a safety hurdle – sometimes real, sometimes more a matter of perception – will remain for some years to come. Yet progress has been made. Ammann has developed a prototype for an autonomous plate compactor. It is only logical to expect such technology be extended to other compactors.
Get on board
The good news is that the hardest challenges already have been overcome. It is our belief that now is the time for all contractors to embrace the technology.