Solving the biggest problem in asphalt paving
The longitudinal joint problem solved with infrared joint heater
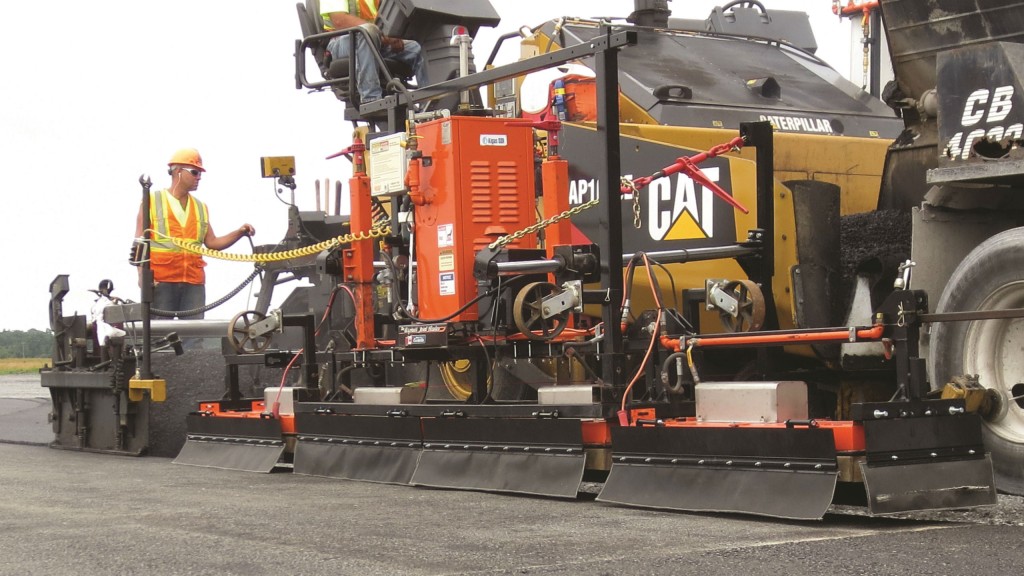
One of the most critical problems in asphalt pavement construction today is achieving a long lasting, longitudinal joint. It is costing pavement owners billions of dollars worldwide in premature repair of the joint. This problem has been recognized for a couple of decades, discussed at many asphalt pavement seminars, and has been the subject of much research, yet there has been little or no progress in many jurisdictions.
The longitudinal joint problem stems from a lack of density on the edge of the first paved lane as the compactor has nothing to compact against. The asphalt is pushed sideways at the edge, resulting in lower compaction density on the outer 3 to 6 inches, typically 4 to 6 percent lower than the density of the mat. This lack of density, according to considerable research, can translate into a reduction of 20 to 35 percent in the life span of pavement because low density means more water penetration, more freeze-thaw action and more moisture deterioration of the bitumen/ aggregate bond. Furthermore, the pavement is not as strong along the joint and is not capable of withstanding today’s heavy traffic loads. Once the crack occurs, a concentration of load on each side of the crack as a wheel passes over it further stresses the joint area.
Historically, paving contractors were able to produce a better joint by limiting the length of a paved lane and moving back to pave along the joint while it was reasonably hot. With traffic control measures making short paved lanes impractical, moving back to pave the warm joint has been all but eliminated on highways. Hence, a lack of density and water impermeability, and early deterioration of the joint.
In North America, some of the best research and reports come from the U.S., such as the Asphalt Institute/ Federal Highways 2012 report Best Practices for Constructing and Specifying HMA Longitudinal Joint. A 2002 quote by the Kentucky Transportation Center in the report illustrates how enduring this problem is as it still applies today: “Many pavements have been, or are in the process of being, resurfaced as a direct or indirect result of longitudinal joint deteriorations.”
While the report covered the United States, the same problems exist in Canada. The report notes, for example, that half the respondents in a Federal Highways Administration (FHWA) Division Office survey said they were not satisfied with the overall performance of longitudinal joints in their states. Thirty-five states said they had some sort of longitudinal joint specification or special provision but only half of those states reported that they had a minimum density requirement at the joint. The minimum density required was as low as 89 percent, which would result in a 35 percent reduction in the life of the pavement. Some states specify that any quality control cores must be taken certain distances from the joint since sampling the joint would not represent mat densities. They have no requirement to test the joint.
It is critical that this longitudinal joint construction problem be eliminated so that our roads can last longer.
The infrared solution
“The infrared heater exhibited the best effectiveness in improving joint quality among all the joint construction techniques used in this study,” said Dr. Baoshan Huang, associate professor, University of Tennessee. He was the lead researcher for the study conducted by Tennessee and Arkansas universities for their DOTs and reported in the American Society of Civil Engineering Journal. It concluded that joint heating produced the highest density and lowest water permeability of several joint making techniques.
In the last several years, contractors have been allowed to re-heat the cold, uncompacted edge using infrared joint heaters to allow for re-compaction, along with compaction of the new hot lane being applied. This has proven to be much cleaner, faster and less costly than removing the edge. Follow-up density testing has proven the joint to be constructed properly.
Airports have extremely heavy loads and cold joints are a serious concern for safety and uninterrupted operation. To address the problem, the Federal Aviation Authority (FAA) specified that six inches of cold, uncompacted asphalt at the edge of the pavement must be removed prior to tacking the edge and matching it with the new hot lane. They then use cores to verify density.
Making progress in Canada
Infrared heating of the joint offers an alternative solution. One of the earliest and best documented airport projects using infrared heating along the longitudinal joint was the 2007 re-construction of the Canadian Forces Base Shearwater Heliport in Halifax, Nova Scotia by LaFarge Construction. The excellent results obtained by using an HDE JMH 400T joint heater manufactured by Heat Design Equipment (HDE) of Kitchener, Ontario, were reported at the 2008 Swift Airport Conference in Calgary, Alberta by the engineering consultant, Hatch, Mott, MacDonald. The contractor reported a saving of 360 tonnes of asphalt on the five paved lanes (without the infrared heater, the contractor would have had to cut six inches off the low density edge of the pavement). The savings in today’s prices amounts to about 40 percent of the purchase price of the joint heater. This does include the additional savings in costs for cutting, removal, cleanup, tack coat and time that would be required to cut off the six-inch edge. The cost to operate the joint heater was just 15 cents per metre.
Since 2007, the technology on the HDE infrared joint heater has been considerably improved to better meet the needs of contractors. Their expandable, paver-attached joint heaters – the JMH300PA, JMH400PA and JMH500PA – include full remote control that allows the paver or screed operator to remotely turn the heaters on or off, or change from high heat to low heat during short delays waiting for trucks. The infrared technology developed by HDE also allows contractors to set the degree of infrared emission to suit daily job conditions – like ambient temperature, wind, paver speed and hot mix temperature – by a simple gas pressure adjustment supplied to the heaters. It is especially critical for the contractor to be able to match the temperature of the hot mix so that re-compaction of the joint area can proceed as part of the normal rolling pattern.
The JMH 300-PA, JMH 400-PA and JMH 500- PA have 3, 4 or 5 infrared heaters, respectively. JMH means it is a Joint Match Heater while the model numbers refer to the BTU/hr output, such as 300,000 BTU/hr for the JMH 300PA. Smaller models can have additional infrared units attached. The number of units used will depend on the paving speed needed and ambient temperature. More units provide faster paving speeds.
Other Canadian airport projects using HDE infrared equipment include runway improvements at Ottawa International Airport in 2016 by RW Tomlinson Ltd, and runway improvements by Pavex Ltée (owned by Béton Provincial Ltée) at Îles de la Madeleine in 2016.
The Ontario Ministry of Transportation adopted an infrared joint heating specification as a special provision to be chosen by district engineers.
Many municipalities, including the City of Hamilton as the leader, adopted a requirement that either echelon paving or joint heating be used to ensure a well-constructed joint. The Region of Waterloo, Ontario, followed suit, as did several other municipalities in South Western Ontario.
At an Ontario Hot Mix Producers Seminar, the county engineer of one of the municipalities reported the cost for echelon paving was about $2 per tonne extra, while joint heating cost only about 25 cents per tonne.
It must be emphasized that adopting a surface temperature specification does not go far enough in striving for a better compacted joint. Reheating the joint for density requires raising the entire depth of the asphalt layer to re-compactible temperatures of 80 degrees C at a minimum, ideally 110 to 130 degrees C. In the Tennessee study, Dr. Huang states: “The air voids distribution obtained from the X-ray CT images show that the effectiveness of an infrared heater in improving joint quality was through increasing the compaction degree of the longitudinal joint deep to the overlay bottom and thus making the joint denser.”
An increasing number of DOTs in the U.S. are adopting joint density specifications with some applying very serious penalty and bonus clauses. One of the leaders is the state of Alaska, which typically applies a penalty of $3 per lineal foot on the entire job if a project’s average top lift joint density is less than 91.0 percent MSG (maximum specific gravity). Alternatively, if the average is greater than 92 percent, they will apply a bonus of $1.50 per lineal foot. This can add up to big money for a paving contractor and as a result, Knik Construction of Anchorage uses HDE JMH 500PA units to accommodate this specification on their projects. They avoided paying $250,000 in penalties and instead made a bonus of $125,000. Since adopting joint heaters, they have received the full joint bonus on 11 of 13 paving projects.
Repairing joints with infrared
A longitudinal joint repair train using hot-in-place recycling is now available from HDE with 64 lineal feet of full-surface infrared. It is powerful enough to heat and soften the asphalt pavement, which is then scarified. Next, an asphalt rejuvenator is added, along with minor amounts of new asphalt. Then the pavement is compacted, resulting in seamless pavement. The speed of the train depends on the moisture condition of the deteriorated asphalt.
The cost of repair is considerably more than building it right in the first place with joint heaters, but it is competitive with standard mill-and-fill techniques and produces watertight pavement along the repair.
Agencies have a tremendous investment in the asphalt concrete pavement they have already bought and paid for. To remove that investment is a costly procedure. Infrared heating equipment allows that investment to be rejuvenated and restructured in place, in much less time. It is the ultimate in sustainability.
Bob Kieswetter P. Eng., is President of Heat Design Equipment Inc. of Kitchener, Ontario.