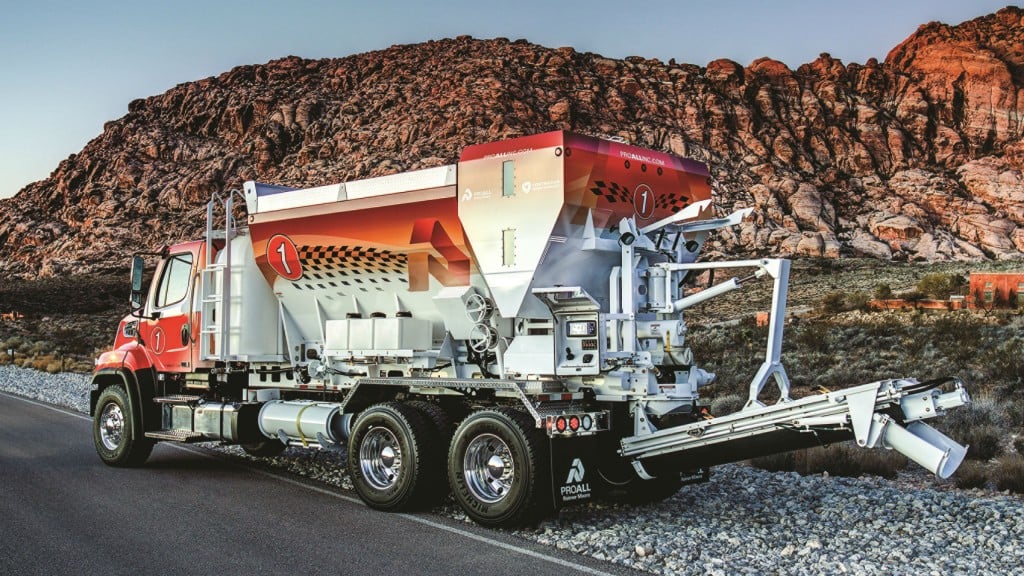
ProAll Reimer Mixers operate on an entirely different principle than the typical concrete truck one might see on the road. Instead of mixing cement, aggregate and water at a batch plant, a Reimer Mixer delivers the constituents to the jobsite in separate bins and mixes them on the spot for a fresh mix anytime, anywhere. The technology offers several advantages, including the ability to deliver concrete over long distances to remote jobsites and the ability to control the composition of the concrete precisely as it’s delivered, including the addition of various other materials for special purposes, such as fibre, colour and many other chemical admixtures.
Adding colourants is self-explanatory, but many other materials are routinely added to concrete to achieve specific characteristics. Adding glass, steel, synthetic and natural fibres, for example, can decrease the permeability of the concrete to reduce water bleeding, help control cracking during drying, and improve pumpability, impact, abrasion, freezethaw and shatter resistance. The fibre component of the fibre/concrete composite must be carefully controlled to achieve the desired properties with fibre typically being 0.1 to 3.0 percent of the total volume.
The proportions of each admixture must be carefully controlled to achieve the desired properties in the concrete. ProAll Reimer Mixers are ideal for these applications because they offer precision control and keep all of the components separate until they are combined on the jobsite.
The need for really effective filtration
Coordinating the motions of the various augers, belts and valves required to achieve the exact mix specified for each batch of concrete requires a sophisticated hydraulic control system with capabilities far beyond the simple directional valve and motor arrangement used on a drum-type mixer. ProAll’s newest model, the Commander, uses a multi-valve manifold to control the belt that delivers materials to the mixing auger in exact quantities according to a program entered into the system’s computer control via a touchscreen.
The hydraulic system consists of a pair of load sensing piston pumps, one supplying 30 gpm for the mix-auger and the other supplying 20 gpm to the belt circuit. A gear-type charge pump is also included in the semi-closed-loop system. Maximum operating pressure is 3,600 psi with the mixing auger typically operating at 2,500 to 3,000 psi and the belt circuit at 1,500 psi. Control is provided by two banks of proportional valves mounted on low-profile manifolds.
The precision valves needed to achieve the level of control required in ProAll’s most advanced equipment require effective fluid filtration to meet the company’s field reliability goals.
“With the sophistication of the automated controls on our new mixer and the use of much more sensitive electro-hydraulic proportional valves, it is extremely critical that fluid cleanliness levels be maintained,” said ProAll engineer Curtis Steele. “If fluid cleanliness levels are not maintained and valve sticking or failure should occur, the equipment can become inoperable or behave erratically, which in the case of producing quality concrete is not acceptable. The control system does monitor and check issues with outputs but when on the jobsite, the requirement for troubleshooting or maintenance can become very costly.”
The first batch of prototype Commander units included a pressure filter at the inlet of each valve manifold. These filters were chosen primarily on the basis of initial cost, and offered a Beta value of 75.
“At first we were just trying to protect the valves from the crud that’s present in a system when it’s first installed,” Steele said. “Diagnosing a valve that’s failed because it’s jammed with metal shavings is costly and time-consuming.
“But as the system got more and more sophisticated it became obvious that we needed really effective filtration and the economy filters just weren’t up to the task. The last straw was receiving a filter with a hole drilled through the threads, which naturally leaked as soon as it was installed.
“So, after about 4 months of less-than-optimal performance, we contacted our local Eaton supplier, HyPower of Fort McMurray, Alberta. We were already using Eaton CharLynn motors for the mixing augers and belt drives, so they were familiar with the system and our needs.”
Eaton pressure filters
HyPower recommended a pair of Eaton HP171- 0011 pressure filters for the ProAll application. These are high-pressure, cartridge-type filters equipped with 7-micron, Beta 1000 elements. HP series filters are rated to pressures up to 6,000 psi and maximum flow rates of 180 gpm.
ProAll selected the Eaton filters in large part because of Eaton’s global network of service and distribution. This was an important consideration because ProAll, based in Olds, Alberta, sells Reimer Mixers in more than 40 countries around the world.
ProAll has standardized the Eaton HP171-0011 pressure filters for the 100 or more Reimer Mixers they build each year.
ProAll also replaced the basic fill-cap style 40μm breathers on the Commander hydraulic reservoirs with Eaton MBR110 Mobile-gate air breathers.
“All of the Eaton filters arrive clean, we don’t find any shavings, and they don’t leak,” said Curtis Steele.