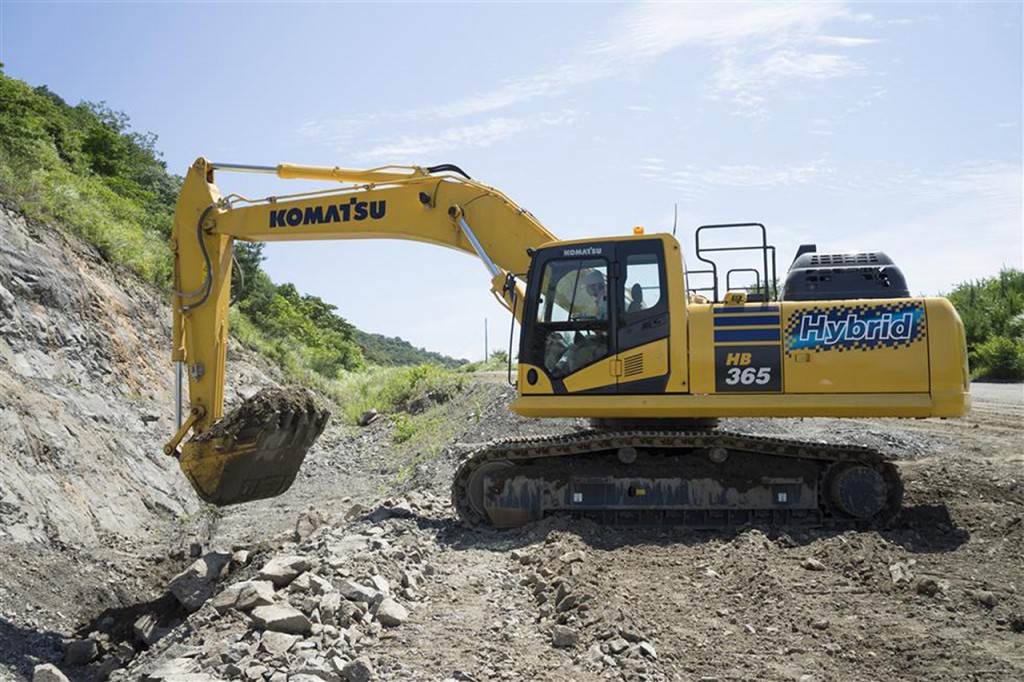
Komatsu America Corp. introduced the new HB365LC-3 hybrid excavator at CONEXPO-CONAGG 2017. It features improved hybrid and total-vehicle-control systems, to help reduce fuel consumption by up to 20 percent – depending on application – while maintaining or exceeding operating performance compared to 36-ton, non-hybrid excavators.
“The new 36-ton-class HB365LC-3 excavator is built for power and production first, with the considerable fuel savings an added benefit,” said Kurt Moncini, Komatsu America senior product manager. “We applied everything we learned when we debuted the HB215LC-1, the world’s first fully-electric hybrid excavator in 2011. Now, we have the perfect balance of performance and fuel efficiency,” Moncini said.
Komatsu’s unique, fully electric hybrid system uses an electric swing motor, which captures swing deceleration energy that would normally go unused, and makes it available to do work. The energy captured during each swing cycle is stored in an ultra capacitor, which provides energy for the swing system. The diesel engine also has a motor/generator for fast charging the capacitor when required, and to rapidly increase engine RPM from an ultra-low idle, for quick hydraulic response when boom, arm and bucket controls are activated.
What makes the Komatsu system unique is the 100 percent electric swing system. The hydraulic power normally needed by the swing system is now completely available for boom, arm and bucket power, helping to improve digging cycle time and production.
To meet EPA Tier 4 Final certified requirements, the SAA6D114E-6, 269-hp engine combines a Komatsu Diesel Particulate Filter (KDPF) and Selective Catalyst Reduction (SCR) system with Diesel Exhaust Fluid (DEF) to meet NOx emission aftertreatment requirements.
Features and benefits of the new HB365LC-3 include:
Tier 4 Final Certified Engine Technology:
- A powerful and fuel efficient 8.85-litre, Komatsu SAA6D114E-6 engine, with 269 Net horsepower and the following technologies to meet EPA Tier 4 Final emission requirements:
- Komatsu Diesel Particulate Filter (KDPF) aftertreatment system to reduce particulate matter.
- Selective Catalyst Reduction (SCR) system, with Diesel Exhaust Fluid (DEF) injection, to help reduce NOx emissions. The SCR catalyst has no scheduled maintenance, and the same life expectancy as the engine.
- Auto idle and auto idle shutdown systems to reduce fuel consumption and provide better management of nonproductive extended idle time
New Performance Features Include:
- The revolutionary Komatsu Hybrid System, using swing energy regeneration and an ultra-capacitor to provide fast energy storage and instantaneous power transmission.
- Special hybrid control logic helps increase boom up and arm out multifunction speed, for improved productivity.
- New temperature-controlled viscous fan clutch helps reduce parasitic load on the engine and lowers sound levels.
- New KOMTRAX 5.0, shown on a large, 7-inch colour screen, relays vital machine data, for easy monitoring and quick operator action.
- New Operator ID system records KOMTRAX machine operation and application data for up to 100 individual ID codes.
- Six working modes (P, E, L, B, Att-P, Att-E,) provide a wide range of performance and fuel efficiency, with energy-saving guidance incorporated into the monitor.
- Optional auxiliary hydraulic attachment circuit, with return filter, accumulator and programmable flow through the monitor, which can store up to 10 individual flow settings and customizable attachment names. Two-way attachments can also run in economy mode.