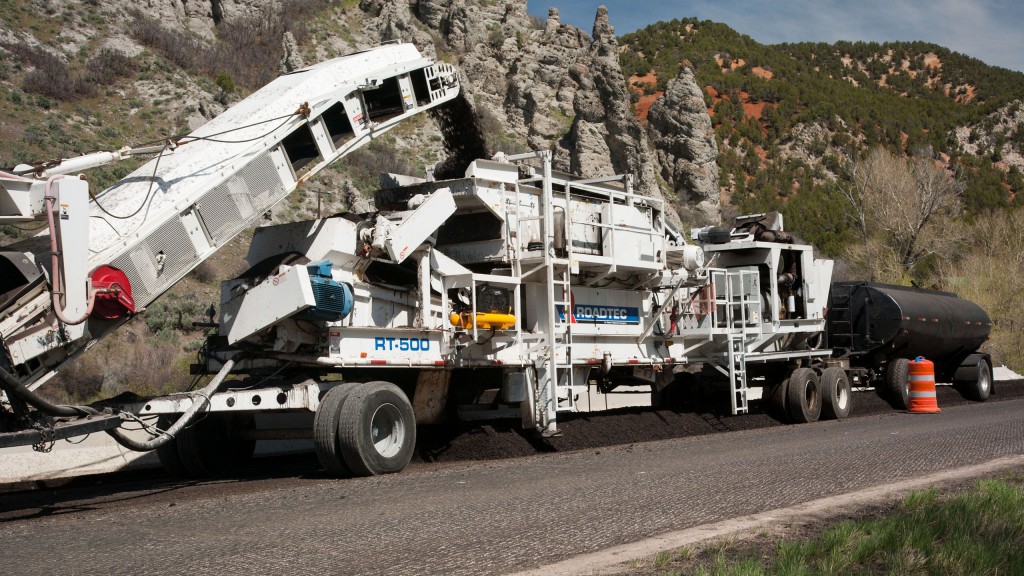
The Roadtec RT-500 is a mobile recycle trailer that can either be pulled and fed by a Roadtec RX-900 milling machine for cold in-place recycle (CIR) or set up on a site as a central cold-mix plant. The RT-500 is designed to process 500 tph.
The machine features closed loop sizing with an onboard vibratory screen and horizontal shaft impact crusher. The process is designed to prevent having to pre-process RAP when the RT-500 is used as a cold-mix plant. The RT-500 also has a weigh bridge on board which is designed to ensure accurate additive injection in the pugmill.
The RT-500 mobile recycle trailer is suited for use in a cold-in-place rercycling production train. CIR makes it possible to repair damage to a roadway in one single pass, while reusing up to 100% of the existing material. Savings potentials are not only through material reuse, but also by reducing equipment requirements, and through time savings. With CIR technology, the paving mix is made right there at the job site. No haul trucks are needed to run back and forth to the asphalt plant since very little virgin material, if any, is used.
The basic concept of CIR is to remove damaged layers, to process the removed material, and then to place it and compact it to make the new structure. A thin layer of hot mix asphalt or other preservation treatment is placed to serve as the new surface course, which completes the CIR process.
After the cold planer has milled the damaged, old pavement layer, it feeds this material into the entry chute of the RT-500. From there the reclaimed material moves onto the double deck screen, which separates reclaimed material by size. The screen is a 5' x 14' (152 cm x 427 cm) low-profile flat screen with fully adjustable amplitude and frequency, and can handle all kinds of materials. The springs and vibration isolators are designed to help make the operation run smooth and quiet. Material of proper size is allowed to pass through and any oversize material will be routed to the Horizontal Shaft Impactor (HIS) Crusher and then recirculated to the top deck of the screen. All reclaimed material ends up in the 48" (138 cm) diameter twin shaft 6' pugmill mixer.
The 3048 HSI Crusher features a heavy-duty main shaft and bearings. Four rows of hammer bars are part of the patented hammer and wedge design used in the crusher. The AR400 liners are designed to provide wear protection in the crusher. There is a hydraulic access door for maintenance. The shaft and rotor assembly can be removed without press fits or keys.
The finished mix is either discharged into a windrow or conveyed straight into the paver hopper.
The computer-controlled additive system meters up to three additives, such as emulsion or foamed liquid asphalt cement, slurry, and water, depending upon the mix formula. Data flows from the belt scale located between the screen and the pugmill mixer to the emulsion metering system, which is designed to ensure that correct amounts of additives are mixed in the aggregate at all times. Spray and return valve operation is also computer-controlled.
The RT-500 computer will log all production data at desired intervals. The data then can be downloaded for a complete history report, which includes rates of all materials used, date, time, distance (or station), and speed. Data can be shown in either Metric or English units.
A larger 8' pugmill is available as well as various options to customize the Roadtec RT-500 mobile recycle trailer to fit a contractor's needs.