Rockster introduces latest mobile impact crusher model R1000S
Compact track-mounted R1000S impactor designed to open up new dimensions in recycling asphalt, concrete and demolition rubble
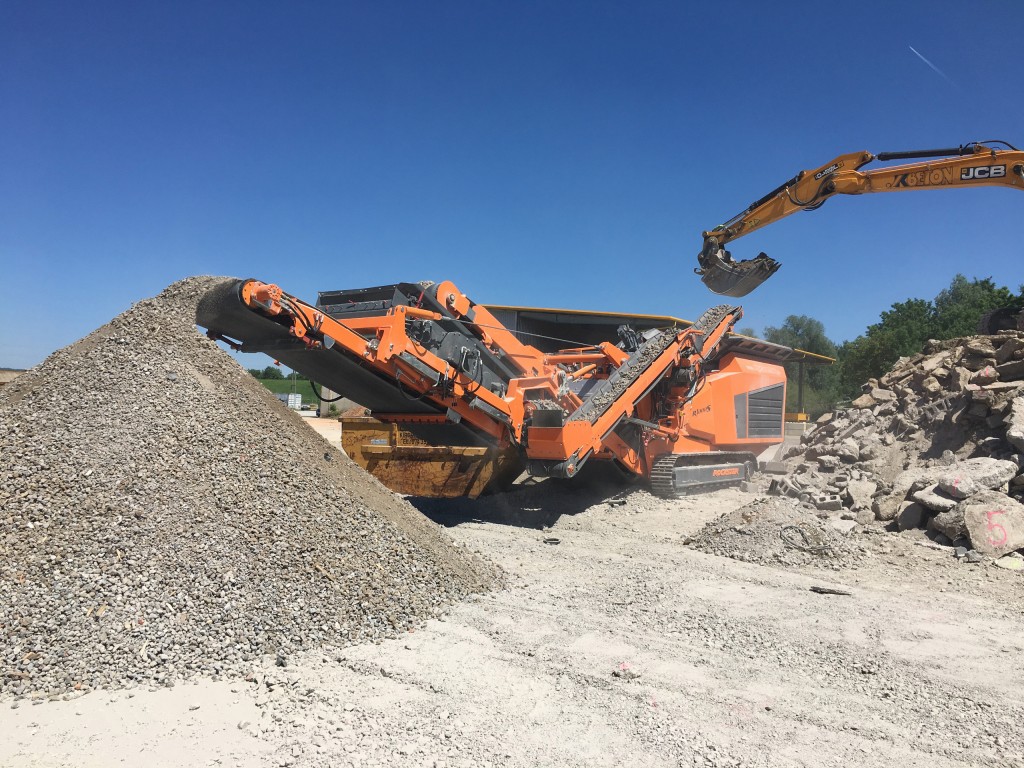
Now available from Rockster, the new mobile, track-mounted R1000S impact crusher is a follow-up to the R900 model, and is designed to open up new dimensions in crushing, in applications including the recycling of asphalt, concrete and demolition rubble as well as the processing of natural stone. This impactor is designed very compact, so most applications will not need special permits for transportation, and units are based on a fully hydraulic concept with a heavy-duty rotor that provides high performance. Plus, an attached screen box guarantees high quality in one work flow. Using it's screenbox and return belt for defined final grain, the Rockster R1000S is ideal for producing concrete with a final grain size of 0/32 mm.
Units include a newly developed multifunctional display, autostart function, stepless, fully-hydraulic gap adjustment as well as load-dependent speed regulation of the vibration feeder as well as a new built-on hammer exchange device that leads to increased ease of use. A versatile setting possibilities and a pre-screen with screen mesh ensure excellent final grain quality.
The optional screening system - consisting of the compact circular vibrating screen RS100 in combination with the patent protected return belt RB92 - is the perfect addition for the track-mounted R1000S for the production of high quality final grain. As a second option the return belt is useable as stock pile belt for the production of three possible final grain sizes, and a hydraulicaly lowerable screen box saves maintenance time and increase the safety of the operating staff.
In addition, the unit's hydraulic vertically adjustable magnetic separator, hydraulically lowerable screenbox and swiveling catwalk make maintenance of the machine easier. Plus, versatile setting options and two-deck pre-screening with a screen mesh provide excellent quality, and an up-and-over lift system of the side and back doors ensures greater free moving space and saves additional space.
The R1000s' vibrating pre-screen chute resonates to stop deposits in the shaft. The vibrating discharge chute transports material on the main conveyor and prevents the wear of the belt, which significantly saves on wear costs. The inlet width of barely one meter and the oversized rotor diameter of more than one meter guarantee the best throughput rates in the different applications. Blow bar exchange is also possible with a built-on hammer exchange device, and an external lifting device is not necessary. The hammers are available in different quality levels, and an optional screening system - consisting of the compact circular vibrating screen RS100 in combination with the patent protected double functional return belt RB92 - is the perfect complement for the track-mounted compact crusher R1000S for creating 100% defined final grain. Furthermore, a hydraulically lowerable screenbox makes maintenance and service easier.
The R1000s also allows users to measure the machine's most important data. Users can check the interaction between the speed of the engine and the rotor, the pressure of the hydrostatic drive, the load of the diesel engine, the speed of the vibrating feeder and gap settings - with everything clearly summarized in one analysis. Specifically, the analysis shows the advantages of Rockster's Hydrostatic Drive. Machine pressure follows the power demand of the crusher, so the Diesel engine stays in its best operation point. The result is a continuous production with exactly definable product quality and an optimization of performance with low fuel consumption. Moreover the hydrostatic system needs no clutch, which reduces wear and maintenance costs.
In addition, because of its compact transport measurements, it is possible to transport the Rockster R1000S without any special permits in most cases. It takes just 10 minutes to unload the impact crusher and to put it into operation. If the transport includes the optional screening system, the dismantling of the return belt and screen box is not necessary. It is also possible to transport the machine with screening system without a specifically required permit.
R1000S transport dimensions:
Length: 10,10 m / 33.2 ft
Width: 2,55 m / 8.4 ft
Height: 3,2 m / 10.5 ft
Weight: 30,4 tons / 67,000 lbs
R1000s key features:
• Gap adjustment with an integrated measuring system for full machine control and analysis
• A sophisticated multifunctional colour display with various quick start functions (different settings for a variety of applications)
• Double deck pre-screen and a vibrating pre-screen chute
• Screenbox and main conveyor are hydraulically lowerable for easy maintenance and change of meshes
• Vertically adjustable magnetic separator (by remote control)
• Hammer changing device for easier replacement of the blow bars
• Swiveling catwalk for easy access
• Double functional return and stockpile belt
Company info
2155 S Amherst Hwy
Amherst, VA
US, 08037
Website:
rocksternorthamerica.com
Phone number:
1-434-381-8881