Sheet Pile Walls Drive Hamilton Harbour Cleanup
Randle Reef is one of the most contaminated sites in the Great Lakes; a massive pile driving project is at the centre of cleanup efforts
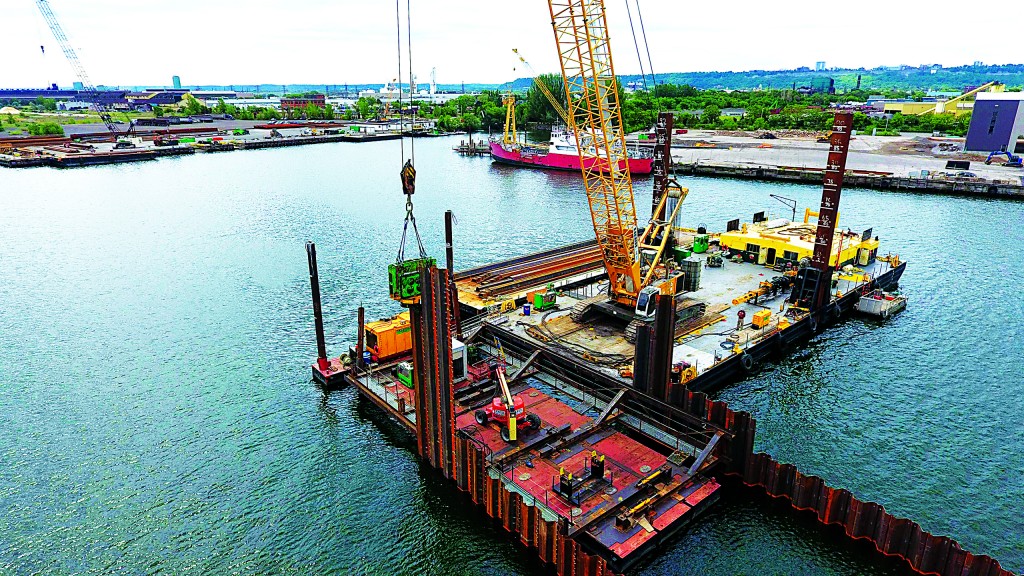
At the western end of Lake Ontario lies Hamilton Harbour, a busy port that has for over a century served shipping and heavy industry in the Great Lakes. For much of that century, the industrial users nearby have released various contaminants into the environment that today are targeted by extensive cleanup efforts.
One of the most contaminated sites in the Great Lakes rests just offshore, next to a steel mill. Randle Reef is around 20 to 35 feet deep and lies at a point that has received much of the runoff from industry, as well as local wastewater plants.
The result has been pollution collected in the sediment of the lakebed that is heavily toxic - to the point that there are virtually no living creatures in that part of the lake.
As part of a $139-million project, Randle Reef is in the process of being remediated. The centrepiece of this work is an enclosure that will surround the worst of the pollution, then be filled with dredged sediment from around it.
"Stakeholders went through a range of options, everything from dredging it all up and trucking it to a hazardous waste landfill site to incinerating it," explained Jon Gee, the manager of Great Lakes areas of concern for Environment and Climate Change Canada. "They concluded that the best option was to enclose it in an engineered containment facility (ECF). By doing that, the city would be managing the problem within its own boundaries, and it would come at a cost within the range of affordability."
The worst of the pollution is not far from Pier 15 on the Hamilton waterfront, which had to be rebuilt as the first segment of the project; that was done in 2015 to allow construction of the ECF to begin. It's a challenging job, especially for the contractor tasked with driving hundreds of steel sheet piles to create the enclosure.
Bermingham Foundations, as a subcontractor to McNally International, started driving piles in 2016.
Project manager Jeff Thomson said working on the water is unique but not necessarily unfamiliar. "Bermingham has worked on the water throughout the Great Lakes, but this job is a little more unique in terms of how you approach it," he said. "The lakebed material we're trying to contain, that has been highlighted as contaminated material, is not something you want to disturb."
The ECF is essentially a double-wall coffer dam; the interior Waterloo barrier is designed to be impermeable, with the ability to contain both the sediment already within the structure and more that will be dredged from the lakebed later in the project.
Sediment from between the inner and outer walls will be dredged mechanically, then clean crushed rock will fill the space for structural rigidity.
Working on the water adds difficulty to a piling project, obviously, and this is no different. To ensure the piling is installed precisely, Bermingham has had to do some fancy footwork with its falsework.
"We can't put in excessive amounts of falsework because that would disturb the lakebed material. So, we actually implemented a floating template system," Thomson explained. "We mounted our falsework onto a smaller sectional barge and hold that in place with temporary spuds. We can move it along the length of the wall as we install it. That limits the amount of disturbance."
The template system allows for easier handling of the sheet piles, which are on the longer end of the range for such work.
"The sheet piling on the outer wall is around 100 feet long at the longest section - that's getting up there for the maximum length you'd see on a sheet piling installation," Thomson said. "When you're dealing with hundred-foot steel, controlling that leading edge while keeping it in the location and tolerance is a big challenge."
Bermingham is driving piles from barges anchored offshore, using a Terex 165 and Liebherr 895 as its workhorse crawler cranes.
The location means all the necessary tools and equipment have to be on the crew boats and stored on the barges - there's no quick trip back to the yard if anything gets missed. In addition, while Lake Ontario doesn't experience heavy swells like one might experience on the ocean, there are other weather factors to be considered.
"We may have done a little overkill on the equipment barge sizes to make sure we had adequate stability," Thomson said.
"The biggest challenge working on the water is the wind - when we're picking up material that's upwards of a hundred feet long it can act like a big sail. When you pick that up, and you have your tag lines trying to hold it in place, that's a lot of surface area. We get several forecasts through the day."
On the business end of the machines, Bermingham is using a combination of hammers to set the piles. Working with the interlocking sheets of Waterloo barrier means changing the way the material is handled.
"We have to have certain jaws and clamps for the vibratory hammers, to fit them over the different styles of interlocks," Thomson said. "You don't want to damage or crush it, because then you lose the ability to actually seal the structure."
The interior wall has been set with vibratory hammers, but the outer wall requires different techniques. Bermingham has relied on its own in-house Berminghammer diesel hammers to get the piles to grade.
"We have set the face wall and structural piles with larger vibratory hammers, and then pick up some of our diesel hammers to get them to final grade," Thomson explained.
"We have had to fit different driving adaptors so they transfer the energy properly into a corrugated sheet pile section as opposed to a nice round pipe or H-beam. We have developed those adaptor plates and connections in-house for this job. It's a big benefit to be able to modify your own equipment and get it out into the field."
Bermingham expects to wrap up its part of the Randle Reef project this summer.
"There will be some 3,400 pilings that go in," Jon Gee said. "Somebody estimated that if you were to place the pilings end to end it would go from the project site pretty much into Toronto."
After that, stage two of the ECF construction will commence, with dredging of the contaminated sediment into the structure taking place in 2018 and 2019.
From there, stage three will be to dewater the interior structure and build an impermeable cap over the entire ECF.
Once completed, the structure will be handed over to the Hamilton Port Authority, which is expected to pave over the structure for use as a marine facility.
Company info
600 Ferguson Ave. N.
Wellington Street Marine Terminal
Hamilton, ON
CA, L8L 4Z9
Website:
berminghammer.com