How to extend the life cycle of your sweeper
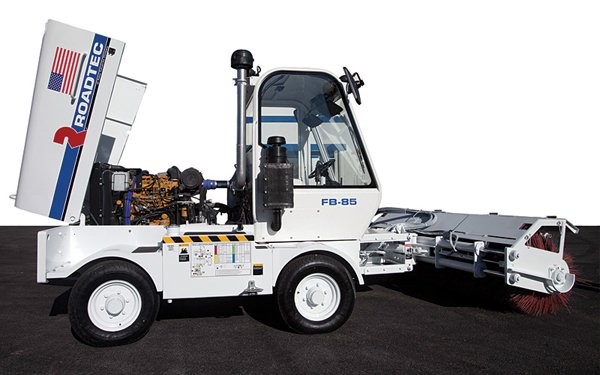
When it comes to rebuilding roadways, sweeper operators play a vital role. Almost every department of transportation requires that newly milled surfaces be cleaned before being resurfaced with hot-mix asphalt. Having a clean, solid base promotes longevity of the resurfaced roads and highways.
During the milling process, particles and remnants of the old asphalt are left behind on the road surface. This debris must be swept away prior to the replacement of hot-mix asphalt. If the roadway is not swept properly, the fine dust particles settle into the milled grooves and prevent a solid bond between the surface and the fresh mix, losing its potential long life.
The leftover millings create a dusty environment, which means regular maintenance and safety checks are vital for keeping the sweeper in good working order and extending its life cycle. (See the check list below for a comprehensive schedule of maintenance.)
Of course, choosing equipment built to handle this dusty work is also important. Roadtec designed and builds their FB-85 Self-Propelled Broom to withstand tough working conditions. It has sealed bushings to keep dust and debris from being collected in the grease and to protect the hinge points from excessive wear due to dirt exposure. The radiator is also 25 to 30 percent larger than the industry standard, the company reports, making it easier for the engine to run cooler.
Some other notable features of the FB-85 Self-Propelled Broom are: a pressurized cab with filtered A/C and heat, creating a better working condition for the operator; left-to-right shift mechanism on the broom for working up against the curb, protecting the front wheels from excessive wear or damaging the side of the machine; speed adjustment for the broom rotation located in the cab; and a manual lift, removable hood that raises up 90 degrees for easy maintenance access to engine, radiator, and cooler.
The FB-85 broom also has a 14,000-pound axle to give the unit longevity, compared to a 7,000-pound axle used by most of the competition, Roadtec says.
At the beginning of every job, Roadtec recommends checking the float or down pressure adjustment on the broom head to ensure an accurate amount of down pressure. If adjusted too high, it will wear the broom heads prematurely. Roadtec’s broom has an in-cab down pressure adjustment, so the broom can be adjusted, as needed, while in operation. Most other competitor’s broom controls are out on the head itself and adjustments need to be done using tools, according to Roadtec.
The maintenance check list shows that the engine air filter should be replaced on a monthly basis for the Roadtec broom. This may be a little more accelerated than the standard engine manufacturer’s replacement time but due to the level of dust the equipment is exposed to over the course of operation, it is best to have a regularly changed air filter for continued long life. Be sure to use the manufacturer’s recommendation for your broom.
A small but important detail makes it easier to track hydraulic oil replacement. Roadtec ships the FB-85 Self-Propelled Broom with blue-coloured hydraulic oil versus the usual tan colour. This allows the service crew to know if the hydraulic oil has been changed, which needs to take place after 1,000 hours of operation – the average usage in one year. Equipment managers may want to alternate colours for the same purpose, a simple maintenance check to make sure the hydraulic oil is being changed on a regular basis.
Maintenace check list for sweeper/broom
Daily safety checks
• Clean all windows, especially the rear windows, for clear visibility.
• Adjust the mirrors for optimal viewing around the machine.
• Check to make sure the strobes are operational so the machine can be seen in traffic.
• Check tire pressures.
• Check tire sidewalls for potential wear from being up against the curb.
• Maintain spare tire on the bottom of the machine (front left tire).
• If not using a cyclone pre-cleaner on the A/C system, check A/C filter and blow it out.
• Check the level of the engine oil.
• Grease the brush shaft bearing.
• If there are no sealed bushings, check all hinge points up front on the broom and grease.
• Check hydraulic oil levels.
• Check radiator coolant levels.
• Check and blow out the radiator.
• Check the brake fluid level.
• Make sure water filter and brush spray bar are clean and operational to keep the dust down.
• Check the float or down pressure adjustment before every job.
Weekly checks
• Check the engine air filter and clean.
• Check the carburetor air filter.
• Check the hydraulic filters.
• Check the engine oil level and filter.
• Grease the axle kingpin.
• Check the battery.
• If the brakes are not sealed, check the brake shoes for debris buildup and clean. Dirty brake shoes can lock up or wear prematurely.
Monthly checks
• Replace the engine air filter.
• Check engine oil and filter.
• Check fuel filter.
• Check hydraulic filters.
• Check drive and steering axles.
• Check A/C system; treat with cyclone pre-cleaner.
Annual checks
• Drain, clean, and refill the 40-gallon hydraulic oil tank.
• Drain, clean, and refill the radiator coolant.
• Drain, flush, and refill the drive axle gear box.
• Drain, flush, and refill the steering axle gear box.