8 stages of risk assessment for safe MEWP operation
Key steps every user needs to follow to comply with new CSA standards
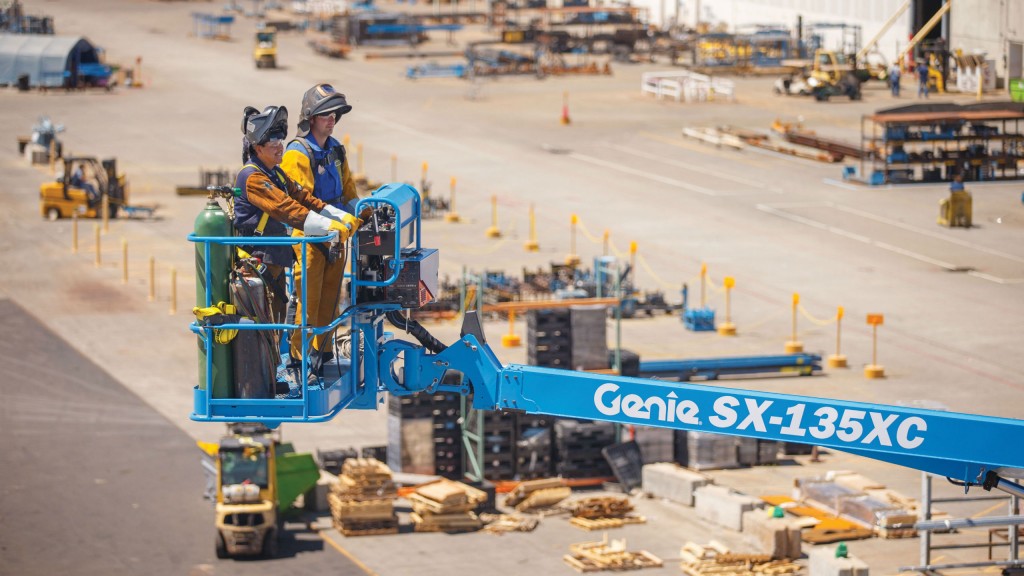
With the so much changing in the updated CSA B354 standards, it is important to call attention to one key item that every user (identified in the standards as employers) needs to be aware of: risk assessment.
Here are the eight stages of risk assessment every user must follow under the new standards:
1. Identify the task to be undertaken
The first stage in the risk assessment is that the task to be undertaken is clearly identified, together with the location and timing.
2. Select an appropriate MEWP
With so many different types of MEWPs available to choose from, ranging in various rated capacities, working heights and reaches, a user must select an appropriate machine based upon consideration of factors, including but not limited to the task to be undertaken, the constraints of the worksite, ground conditions, site access and proximity to the public or other workers.
3. Assessment of the risks associated with the task
The risks associated with the task specific to a MEWP's operations must be identified. These might be associated with the location where the work is to be carried out, the nature of the MEWP or the personnel, materials, and equipment to be carried.
4. Identify control measures
Once the hazards and risks involved in the task have been identified, the procedures and measures required to control them must be identified and implemented.
5. Identify safe work procedures
The risk assessment results are used to plan safe work procedures, including any contingencies required, in carrying out the identified tasks.
6. Rescue from height
Rescue planning is a necessary component of a risk assessment when working at height. Some situations require prior planning to ensure a safe and timely rescue.
A system failure of the MEWPs that results in the loss of the platform control functions may be addressed by the use of:
a) The MEWP auxiliary power function of the controls;
b) The MEWP secondary manual emergency descent controls.
The user must follow the manufacturer's directions in the use of these systems. This plan should be included in operator and occupant training.
A fall from the platform when using a fall arrest system will require a rescue plan to determine how the affected worker will return safely to the platform or ground. The plan must be put in writing and become part of the company's training manual. All occupants must receive training that explains procedures to follow if they fall and await rescue or witness another worker's fall. Ideally this plan will limit the time that an occupant is suspended after an arrested fall.
A rescue plan can include the following:
a) Self-rescue – by person involved;
b) Assisted rescue – by others in the work area; and
c) Technical rescue – by emergency services.
As part of the plan, consideration must be given to the rescue of MEWP's occupants if the machine is unable to be lowered for any reason, such as complete machine malfunction or work platform entanglement.
In the case of platform entanglement, the operator and occupants must be removed from the platform prior to attempts being made to free the platform. A MEWP which has tipped beyond their centre of gravity must be stabilized and secured before attempting rescue. Technical rescue might also be necessary in the event of illness, injury or risk of exposure. Any rescue procedure must take into account the reasons why the platform may be stranded at height and any need for prompt action.
Rescue should always be carried out by appropriately trained personnel, using the machine's ground controls or secondary lowering system when feasible. All rescue procedures near electrical conductors must comply with section 6.8.11 of the Standard.
7. Communicate the results
The user must communicate the results of the risk assessment to all parties involved.
8. Review and adjust
Before a job starts, and periodically throughout a long-term job, the risk assessment must be reviewed to check if any parts of the tasks or the working environment have changed and determine the effect that it could have on the safety of the operation. If any modifications to the risk assessment are required, these must be communicated to all those involved prior to resuming the job.