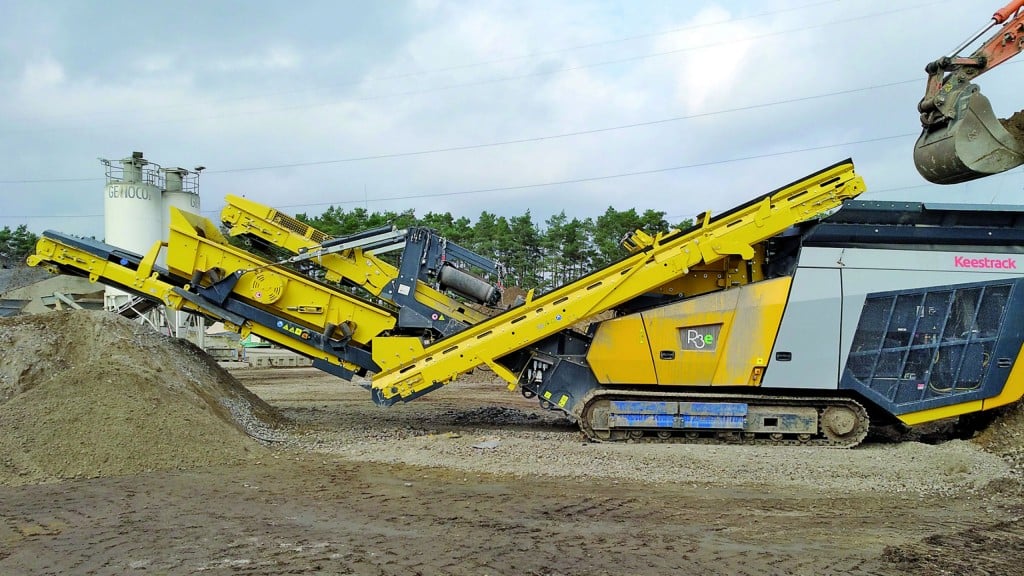
Keestrack will unveil a new innovation at Intermat, in Paris, this spring: a new modern design for its R3 / R3e track-mounted impact crusher. Thanks to its compact transport and operational dimensions, the 30 tonne model offers all advantages of the mature diesel electric hybrid concept, which Keestrack is implementing as an efficient alternative drive system in more and more product ranges of its highly mobile crusher and screening plants.
The R3 (formerly Destroyer 1011) is a highly mobile solution with a broad range of applications from short-term construction-site operations to flexible semi-stationary production in medium-sized recycling and production companies. The new generation is being launched in a modern, attractive design. These plants are also characterized by fast loading, short set-up times on site and a high level of mobility thanks to the supportless frame construction with a rugged undercarriage track frame. Extensive coverings, wide-opening doors and flaps set the standard for accessibility to all operational components and satisfy the requirements for operational reliability and maintainability. The new crusher will be available in a diesel hydraulic R3 version and as a fully hybrid Keestrack R3e with a diesel electric drive and full electric plug-in power supply.
At the heart of both versions is the high-performance 48 ICR 100-00 impact crusher with a large 770 x 960 mm inlet opening, and which has an excellent crushing efficiency up to 250 t/h thanks to the heavy-duty 920 mm rotor (diameter: 1,100 mm, 3,200 kg) and high rotor speeds. Specially adapted crushing tools, a wide adjustment range for both impact aprons (milling beam is optional) and a sophisticated overload system safeguard a broad range of applications from concrete recycling with intensive wear to the production of high-quality natural stone grains.
Thanks to the 235 kW EU IV Volvo diesel engine (option: EU IIIA; 260 kW) and 300 kVA generator as the on-board energy source, the new Keestrack R3e also remains fully autonomous and highly flexible when deployed interchangeably to construction sites. The crusher is powered either by 132 kW or 160 kW electric motors. Exchangeable belt pulleys (375 mm/450 mm) can be used to adjust the crusher's performance characteristics. A 45 kW electric motor with two connected load-sensing pumps provides power to all hydraulic components (drive, crusher control, hub hydraulics, feeder/post screening unit, cooling fans). This extensive use of electric drives in conveyor systems and peripheral units means extensive use of hydraulic lines, among other things, is a thing of the past. New cyclone extraction technology reduces the required volume of hydraulic oil in the system for identical change intervals to 75 litres, decreasing maintenance costs and operating costs decisively.
The R3e has an external 63 A plug-out connection for the economic operation of subsequently connected screening units or stockpile conveyors as well as a standard plug-in connector for full electric operation from the mains or an additional generator. All the system functions controlled via the PLC controller with the new intuitive user console and comprehensive remote control unit remain active without the use of the on-board diesel engine.
The new optional single-deck afterscreening unit offers almost 4.4 m², corresponding to around 30% more screening area than the previous model, thereby considerably optimizing machine performance in the production of high-grade final grains. A recirculation conveyor and optional light-material air separator facilitates production in closed cycle, oversize grains can be optionally removed as a secondary product via a removable discharge side-conveyor. All other conveyors, including the optional fines discharge in the pre-screening unit, can be hydraulically folded for transport purposes. Even when fully equipped (including milling beam), the fully hybrid R3e only has a transport weight of around 32.0 t.
Keestrack predicts immediate savings in energy costs of between 40 and 70 percent compared to conventional diesel hydraulic drives for its diesel electric crushing machines or fully hybrid solutions with optional plug-in power supply. Other advantages include lower maintenance costs primarily for electrical conveyor systems and screening modules and an overall higher service life for drive components that are more uniformly loaded. With regard to on-board diesel operations such as fully autonomus stand-alone solutions for a range of high-grade end products or as all-electric multistage crushers with directly connected electrical screening machines or stockpile conveyors, Keestrack's hybrid units offer considerable cost-effectiveness without compromising flexibility or mobility.