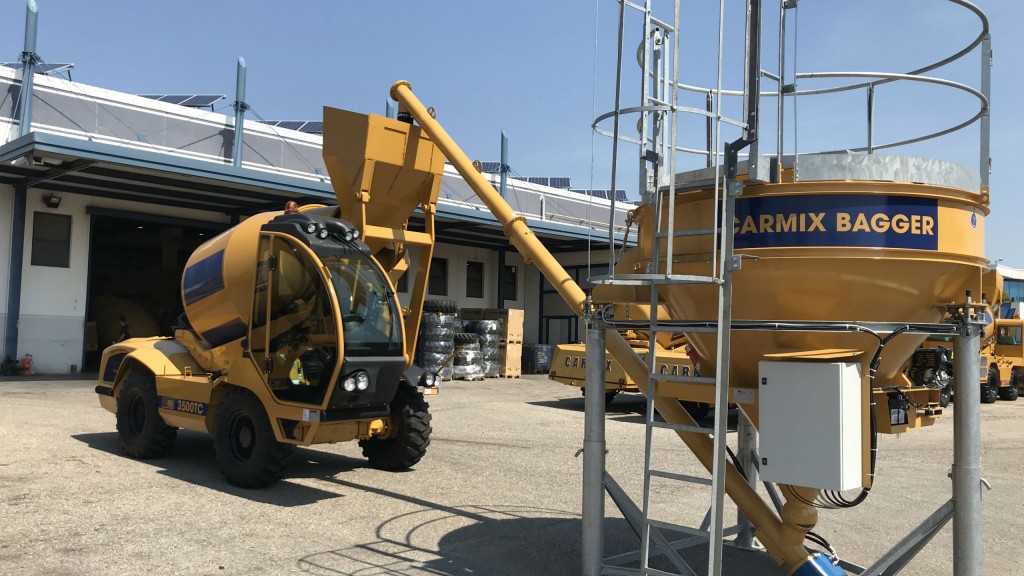
Metalgalante has introduced new Carmix tools for contractors working with concrete on the job site. Carmix Bagger, a tool compatible with all Carmix machines, is set to increase their productivity at the work site, while the new Concrete Lab helps produce high-quality product.
Carmix Bagger is a steel mini-silo with a capacity of 3 cubic metres, speeding up the cement loading process and ensuring a strict accuracy of the mix design. This machine includes a load-cell container that weighs the quantity of materials loaded. Thanks to its special construction, both normal sized cement bags and big bags may be used. After loading, a feed screw carries the content into a Carmix batching plant. The whole process is fully autonomous. Each operation is controlled by a hydraulic motor, fed by an engine: for this reason, Carmix Bagger can be used in worksites where no electric power is available.
Some characteristics of Carmix Bagger are designed to simplify the operators' work, ensuring more productivity and less costs. Carmix Bagger can be easily carried by a forklift and, thanks to its compact size, it only takes up half a 20-box container, minimizing shipping costs. Moreover, the use of cement big bags makes the work environment healthier, reducing dusts to a minimum and cutting operating costs for bag disposal. Finally, loading the big bags directly contributes to reducing raw material costs and raises productivity, as Carmix Bagger can contain up to three 1-cubic-metre big bags on each cycle.
Concrete Lab is a small "analysis laboratory" stemming from the synergistic combination of Promix and Concrete-Mate. These two technologies transform Carmix 3500 TC, Carmix 5.5 XL, Carmix 3.5 TT and Carmix 2.5 TT into real mobile concrete batching plants.
Carmix machines are equipped with Promix, a system measuring all parameters of concrete and immediately reporting its characteristics. This instrument evaluates the concrete mix with a stainless steel probe housed inside the concrete mixer and powered by a solar panel, while a display in the cabin receives information in real time. This sensor detects slump, temperature and speed of mixer rotation and signals when the concrete is ready. All data is constantly updated every ten seconds and sent to a receiver which, through a high-readability display, provides the parameters of the concrete being prepared. This information can also be stored in a PC or sent to other mobile devices via GPS.
Promix technology combines with the technology of Concrete-Mate, a digital Mix Design Manager including an RMC Plant standard level management software that, using four sensors in the mixing unit, guarantees a top-quality concrete mix, in compliance with international concrete production standards (UNI 206-1 - ASTM - ACI etc.) and full control over production costs. Concrete-Mate allows the operator to select up to 15 different mixes and 99 types of materials, to obtain multiple combinations that fit any worksite. When the software has stored a mix design, it suggests the operator the dosage of each element, the sequence of operations and the working time for each process step. Moreover, at the end of the process, the system issues a report containing all analytical data of the mix design (including the name of the client company, the worksite and operator), as well as the mix processing time, any weight deviations between the charged weight and the theoretical weight and control over the whole operation.