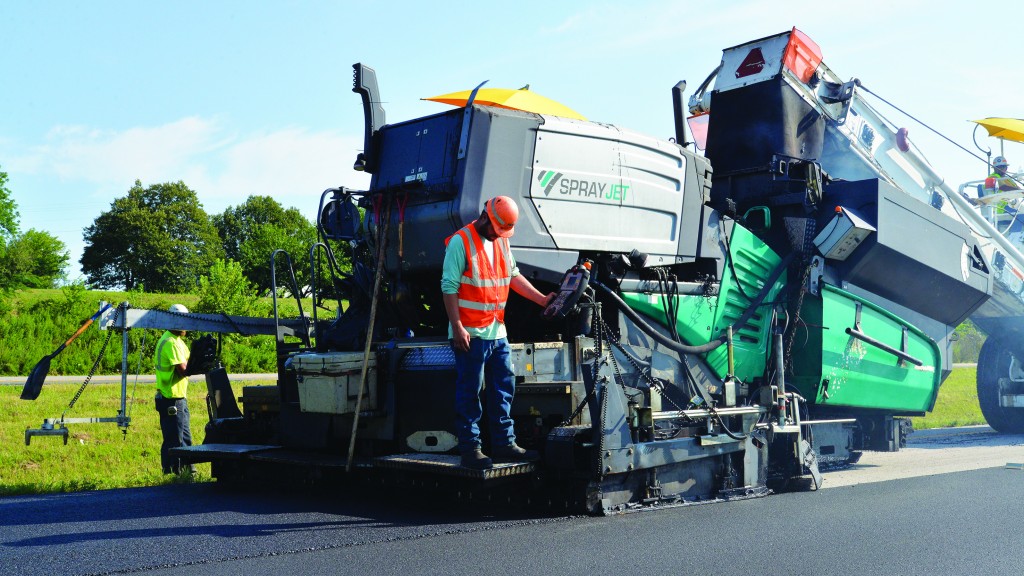
Contractors and government road agencies in North America have been using spray pavers to place ultrathin bonded overlays (UTBOs) for years.
But increasingly, spray paver technology is being used to place standard or conventional hot mix asphalt overlays as well as UTBOs.
Now, departments of transportation are going beyond ultrathin bonded overlays as they consider the benefits of placement of conventional hot mix asphalt (HMA) mats using the built-in spray system of the spray pavers.
Superior bond or "tack" coats
A bond or "tack" coat adheres one layer of asphalt to another layer of pavement, whether bituminous or portland cement concrete. The same way that fragile, thin veneers of wood are glued to each other to form a robust sheet of plywood, research shows layers of pavement perform better when thoroughly bonded to each other.
The benefits of using a spray paver for conventional HMA placements are many, and they all revolve around the bond coat as applied thoroughly by the built-in spray systems.
With the spray paver, eliminating the bond coat distributor truck ahead of the paving train means less congestion in the work zone, providing a safer environment.
Placement of bond or tack coat by a spray paver is generally more thorough than done with an independent distributor truck, at higher rates of application.
With the spray paver, the warm, fresh emulsion is directly overlaid with asphalt as soon as it's sprayed. Like the UBTOs, this hot-on-hot paving results in a superior bond of the conventional asphalt overlay to the substrate. This saves a great deal of time, as there is no longer any need to hold off paving until the emulsion "breaks" (loses its water content, leaving residual asphalt behind). This water from the emulsion is wicked up into the asphalt overlay and dissipates.
Placement of bond coat simultaneous with overlay means there is no way the asphalt can be picked up by haul truck or automobile tires, where it can be tracked onto adjacent roadways, curbs, parking lots or retail stores.
Spray paver for HMA
With their superior means of placing the bond or tack coat - complete, a full lane wide – it's little wonder DOTs are looking at spray pavers to place conventional hot mix asphalt lifts.
"In the three states in which we do business, it's a requirement for some jobs that a spray paver be used to apply the bond coat emulsion and the mix, whether for an ultrathin bonded overlay, or a conventional Superpave mix," said Andy Ernst, vice president for construction operations with Pace Construction. "A competitor could not have bid on this portion of the job with only conventional paver and tack distributor truck, unless he chose to place a chip seal with asphalt overlay, which we chose not to bid."
Spray paver placed conventional overlays are specified at the discretion of the DOTs, according to the job at hand. "I don't ever see distributor tack and paving going away," Ernst said. "Instead, spray paving for conventional HMA is just one more tool in the owner's toolbox they can use for superior pavements. It does a very good job and I see a need for both types of applications."
Nonetheless, Ernst sees more spray paver applied conventional HMA pavements in the future. "Last year we placed two of these applications in Indiana," he said. "They've been doing UBTOs, but 2018 was the first time they placed conventional HMA with a spray paver."
For this work Pace uses its new Vögele Super 1800i-3i SJ SprayJet spray paver, applying both UTBOs and conventional hot mix overlays. As an alternative to spray paving, the Vögele Super 1800i SJ also can be easily adapted to conventional HMA paving following removal of the emulsion spray module.
In late summer 2018, Pace was using its paver to swiftly place a 2-inch-deep conventional Superpave HMA lift, compacted to 1 3/4-inches, on dual-lane U.S. 60 near Mansfield in southwest Missouri. Two breakdown rollers and a finish roller were being used, with a target density of 94 percent.
Missouri DOT provided an option for standard paving with the spray paver. That's because owning agencies like elimination of the tack coat distributor truck for conventional paving, as is possible when HMA is placed with a spray paver.
The spray paver option is clean, cutting down on haul trucks driving through the emulsion, tracking it all over temporary striping, the pavement and the lift placed the day before. Spray paving eliminates all that as the tack coat is placed by the paver immediately ahead of the lift of asphalt.
"I've been with the spray paver for all summer, and this is the first full-depth conventional HMA job we've done," said Bob Needels, project manager for Pace. "The others all have been 5/8-inch UTBOs. U.S. 60 is the first Superpave I've ever seen it lay, and we're getting really good results out of it. It's a very clean process, with no tracked tack. We're getting a good reaction out of the truck drivers, who don't like tack slung all over their trucks any more than we do on our equipment. Using the Super 1800-2i SJ benefits everybody."
Needels said it's actually better not having the distributor truck in the paving train at all. "It's safer because it rules out delivery trucks sliding on the slick tack off into the ditch," he said. "And if a car happens to get into the closed lane, and they slam on their brakes, there is no tack to slide them out of control."
Pace owns three Wirtgen mills: a W 2000, a W 220 and a W 210i. The Super 1800-2i SJ is one of two Vögele pavers owned by Pace, the other being a Vision 5100-2i 8-foot tracked paver. Pace acquired the SprayJet paver in 2015. It succeeded Pace's classic Vögele SF 1800 spray paver, purchased new in 2007 and used through 2014.
"This is our third season with this paver," Ernst said. "The bottom line is that the emulsion the spray paver puts down creates a very, very strong bond with the Superpave mix, or combined with the 5/8-inch-deep thin overlay with its 3/8-inch durable aggregates, makes for a very good wearing surface for higher traffic volumes in lieu of a chip seal."
Built-in spray function
One paver maker offers an aftermarket spray system that must be attached to the exterior of the machine, but this poses significant disadvantages, Ernst said.
"The dedicated spray functions of the Vögele paver work great for us, because we can get those jobs with spray specs year after year and keep it operational all season," he said. "That's why we choose to not remove the SprayJet module for conventional paving, as can be done."
Pace looked at a competing make of spray paver, and even at the paver for which an aftermarket spray system had been devised, but chose to go with Vögele.
"That maker was introducing its aftermarket system and considering it was new technology, we just didn't feel comfortable with that," Ernst said. "They had a different manufacturer making the spray unit to fit the paver, and with it all being so new, we chose not to go down that road," Ernst said.
"And the only other purchase option was a model which could only be fed by a material transfer vehicle, while the Super 1800-2i can be serviced directly by trucks if the insert is removed from the hopper," he added. "That was a feature that was very appealing to us, because we will place the UTBO in subdivisions without much room for an MTV."
Because spray paving was designed and built into the Vögele Super 1800i-3i SJ, spray paving jobs are less problematic than with aftermarket systems. The system is organically integrated into the paver, rather than bolted on as an afterthought.
The SprayJet module is operated entirely via a touchscreen integrated into the spray module, where the entire spraying process can be monitored. The operator can check all settings and values at a glance, such as spray nozzle activity (active/inactive/switched off) and spray pressure.
Also, on the new Super 1800-3i SprayJet, the circuits for spraying and circulating the emulsion - as well as for cleaning the lines – are switched automatically via electronically controlled ball valves, making operation of the individual functions much simpler, and preventing operator errors, such as those associated with manual systems.
Work sequences are set automatically in accordance with the function that has been selected and activated. For example, the control unit for the SprayJet module calculates the maximum pave speed as a function of the nozzle size used and the selected rate of spread and displays this value on the paver operator's ErgoPlus 3 operating system console. This ensures uninterrupted application of the emulsion. The rate of spread can be set and the nozzles calibrated or individually activated and deactivated just as easily on the control panel of the module.
In addition, the handy automatic functions Start of Job and End of Job are activated by the paver operator at the push of a button. This ensures that spraying begins and ends at exactly the desired point over the full pave width.
Tom Kuennen is a technical writer.
Company info
6030 Dana Way
Antioch, TN
US, 37013
Website:
wirtgen-group.com/en-us
Phone number:
615-501-0600