Intelligent Compaction provides better quality control, resulting in longer pavement life
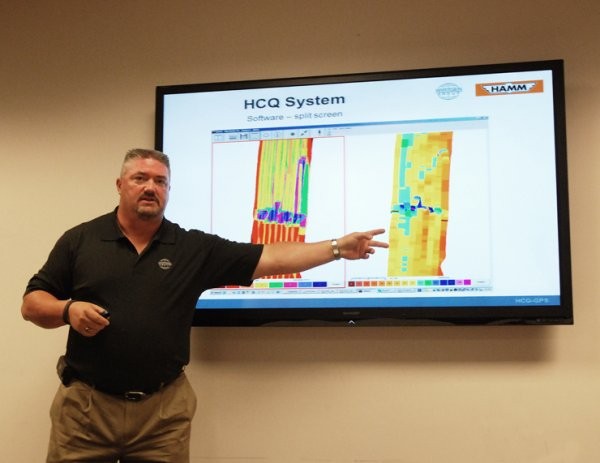
Intelligent Compaction machines are vibratory rollers with accelerometers mounted on the axle of the front drums, GPS, infrared temperature sensors (for asphalt compaction) and on-board computers that display real-time, colour-coded maps to track roller passes, asphalt surface temperatures and stiffness of compacted materials. They are offered by several companies, including Hamm, the compaction division of Wirtgen.
Hamm’s latest intelligent compaction system is HCQ (Hamm Compaction Quality), which provides pre-installation kits for any Hamm roller. This lets the receiver and computer tablet identify the type of roller on which the system is mounted, enabling the HCQ receiver and tablet to be easily transferred from one roller to another, minimizing costs.
“We can transfer the receiver and computer tablet from one machine to the next to identify the size and type of roller to correct the offset from where the receiver is mounted on the roof, to the centre of the front drum,” said Tim Kowalski, Hamm applications support manager. “This provides extreme accuracy for position and better utilization for the contractor, and is a Hamm exclusive for HD+ Series asphalt rollers and all our soil compactors.”
New Hamm rollers can be delivered with the HCQ pre-installation kit. This applies to soil compactors and asphalt rollers, as well as machines with a cabin or ROPS canopy. Retrofitting is also possible for all soil compactors and HD+ machines.
The system is extremely flexible: All of the other HCQ modules can be retrofitted individually and exchanged as required between different machines and construction sites.
Clear dialogues and icons make the HCQ system extremely simple to operate. The plug-and-play solution, with automatic machine detection, eliminates complicated parameter settings. The data provides documentation of the continuous compaction control, with no need for transformation or further processing. Data collection and backup also serve as a basis for individual evaluation and preparation of statistics. Once work is complete, the data can be backed up easily via the USB interface.
The HCQ Indicator enables monitoring of asphalt stiffness. It also measures the asphalt temperature continuously in front of and behind the roller, and shows the temperatures on the display. A split screen capability enables the operator to view two functions at the same time.
At the core of the application is an extremely rugged panel, touch-screen PC with USB interface. This computer provides processing, monitor and data storage. It is based on military standards, has a fully enclosed metal case, and is protected against water and vibrations.
The differential global positioning system (DGPS) receiver in the heavy-duty version has magnetic feet and only takes seconds to mount on the roller, dispensing with the need for a base station. This device receives satellite signals, along with a DGPS correction signal. Licenses for these signals are available in different accuracy classes by subscription.
The HCQ Navigator retains the GPS signal for up to 16 hours even after the machine is shut down. This eliminates wait time for system initialization when starting work, after breaks, at the start of shifts, and so on. When compacting under bridges or in locations with radio shadowing, sensors combine with the intelligent software to compensate for insufficient GPS signals for up to one minute.
A WLAN data network can be used to interconnect a group of rollers so they can exchange measurement results continuously. Each of the roller operators can watch the current progress of the group’s work.
During the compaction process, the panel PC shows the operator how stiffness is progressing. Separate graphics depict, for example, the number of completed passes or the current asphalt temperature, and the operator has the ability to monitor two of these functions simultaneously on the split screen.
For better orientation, guidelines can also be displayed in the system for the operator. During compaction of asphalt, for example, this might be the required pass frequency, the desired compaction result or the temperature window for compaction.
IC is a technology which provides better quality control, resulting in longer pavement life, according to the U.S. Federal Highways Administration, something worth considering when bidding for contracts.