Canadian compaction solution shows solid paving potential
AMIR TRAK rubber track asphalt compactor is tested on Canadian highways
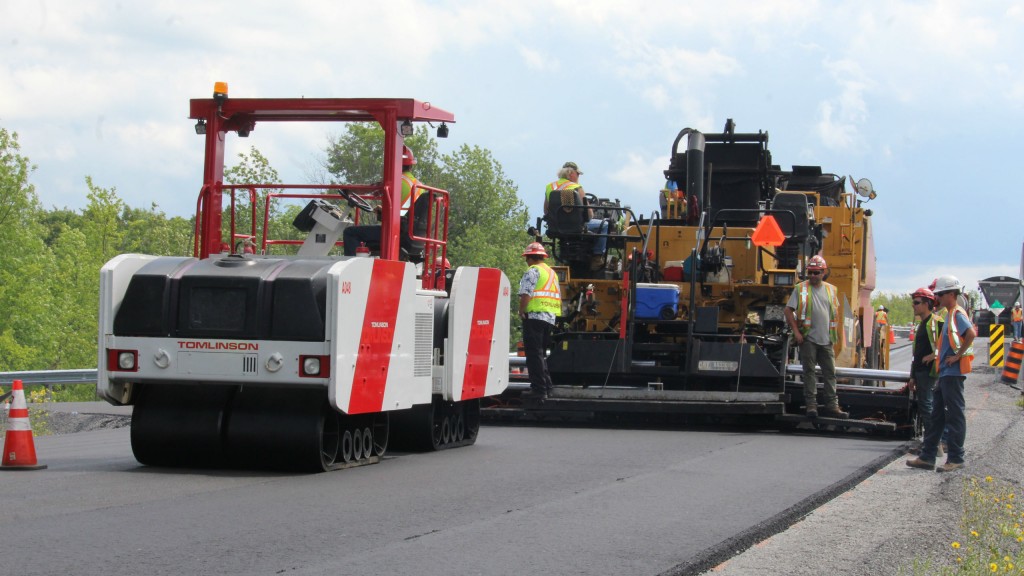
A new asphalt compactor that has been tested on Canadian highways and bridges for years is one step closer to becoming a marketable product. Called the AMIR TRAK, the machine uses rubber tracks instead of steel drums to achieve better densities in less passes and better permeability leading to less aggregate loss.
A new asphalt compactor that has been tested on Canadian highways and bridges for years is one step closer to becoming a marketable product. Called the AMIR TRAK, the machine uses rubber tracks instead of steel drums to achieve better densities in less passes and better permeability leading to less aggregate loss.
Abd El Halim, professor at the Department of Civil and Environmental Engineering and director of Infrastructure Protection and International Security Program at Carleton University, developed a new theory about compaction and worked with the National Research Council (NRC) to develop a prototype with a single track spanning the width of the machine. "The current philosophy of compacting demands a very high load over a small footprint. The steel drum only comes into contact with the asphalt for a few milliseconds. AMIR works the opposite way – with a very low type of contact," he says.
Then he field-tested and results have consistently shown that AMIR-compacted asphalt pavements were free from construction cracks while having equal or higher densities than conventionally compacted pavements. Laboratory testing of cores extracted from the field have also shown that AMIR-compacted pavements had higher indirect tensile strength.
MTO took notice of results reported about the AMIR TRAK and began trialling it in 2011. The machine achieved adequate results but was difficult to operate and suffered from poor maneuverability, among other issues.
"We recognized the benefits of the technology and our main goal was to get trial sections on the road to evaluate the properties of the material and then evaluate its long-term properties," says Frank Pinder, area contracts engineer, MTO.
MTO trialled it again in 2012 on Highway 28 between Peterborough and Bancroft. This time, the Tomlinson Group of Companies served as the contractor, and they have been the contractor on all AMIR TRAK trials since then.
MTO describes this as their first successful trial. They used SuperPaver 25 mixes to pave and compact a 500-metre section of the highway. One lane was compacted with three conventional steel-drum compactors and one side was compacted with a single AMIR TRAK in order to provide a side-by-side comparison.
The AMIR TRAK achieved slightly higher compaction results with just six passes than the three-roller train achieved in six to eight passes each.
The contractor's perspective
After the trial, Tomlinson started tinkering with the machine. "There is a lot of technical data to back up Halim's theory, but the machine needed a contractor to make it a marketable, everyday product," says Ken McIntyre, contract manager, R.W. Tomlinson.
The machine suffered from belt slippage on elevated curbs, some asphalt pickup, and was difficult to turn. To solve this problem, R.W. Tomlinson looked at different tracked machines, such as ATVs, tractors and others. Through a lot of R&D and head scratching with mechanics, they eventually designed and built a new machine. They stripped down a 2012 Cat CB534 roller and installed an AMIR TRAK conversion kit that included two tracks for improved maneuverability, then made it heavier to compensate for the decreased pressure caused by the increased footprint of using two tracks.
The company also solved the machine's asphalt pickup issue. "Tomlinson has a history of innovation, and we were attracted to this technology for that reason, as well as the operational costs savings and taxpayer savings," says McIntyre.
MTO started looking at other opportunities for the AMIR TRAK. Since the machine doesn't use vibration, they considered bridge decks as a possible opportunity for it. They trialled bridges on highways 417 and 34. They conducted the first test in late November of 2014 when the ambient temperature was -1 degree C – much lower than the 7 degrees C required for MTO jobs. The AMIR TRAK compacted an 80 mm lift while the steel drum rollers compacted a 40 mm lift.
The AMIR TRAK achieved 92.6 percent density.
"After nearly five years, [on Highway 417] the side compacted with steel drum rollers is exhibiting moderate coarse aggregate loss, while the side paved by AMIR exhibits only very slight aggregate loss. The difference is dramatic," claims Pinder. "Also, on Highway 34, the side that was compacted using the conventional method is exhibiting moderate coarse aggregate loss, while the side compacted by AMIR exhibits only very slight aggregate loss."
Less heat, less permeability
With the AMIR TRAK, the asphalt temperature doesn't need to be as high as it does for a traditional steel drum rollers, which is 130 to 140 degrees C. In one trial, they began compacting with the AMIR TRAK when the asphalt temperature was just 110 degrees C. By the time the AMIR TRAK completed compacting, the asphalt temperature was 90 degrees C. It achieved better densities than the steel drum rollers in the same trial.
The AMIR TRAK also achieves much better permeability rate – about 1/3 that of conventional compaction. Water that penetrates the asphalt can damage the asphalt, especially during freeze-thaw cycles.
Tomlinson completed a new version of the AMIR TRAK in summer of 2019 and demonstrated it at a pave-in co-hosted by Ontario Road Builders Association (ORBA), Ontario Asphalt Pavement Council (OAPC), the Ministry of Transportation Ontario (MTO), R.W. Tomlinson Ltd. and Carleton University. More than 70 contractors attended.
"ORBA believes that innovation generates value and is continuously devoted to demonstrating technological advancements in specific areas of asphalt paving and road construction," said ORBA OAPC Technical Director Doubra Ambaiowei. "Achieving specified density, resulting in an impermeable surface are recipes for durable and long-lasting pavements. As such, the AMIR TRAK technology is of particular significance and interest to the industry considering its unique attributes and capability to compact the mat to the required density with a tight impermeable surface and no cracking. The pave-in was also an opportunity to see results of the side-by-side comparison of the AMIR and conventional rollers."
"With the AMIR TRAK, you see compression right away, even after just one pass, but conventional pavers seem to just glide across the surface," says Pinder. "In my mind, seeing is believing."
Nathan Medcalf is a freelance writer.
This article originally appeared in the January 2020 issue of Heavy Equipment Guide. Check out the digital edition here.