Green Machine bets on battery power
The company retrofits OEM equipment to meet demand for battery-powered solutions
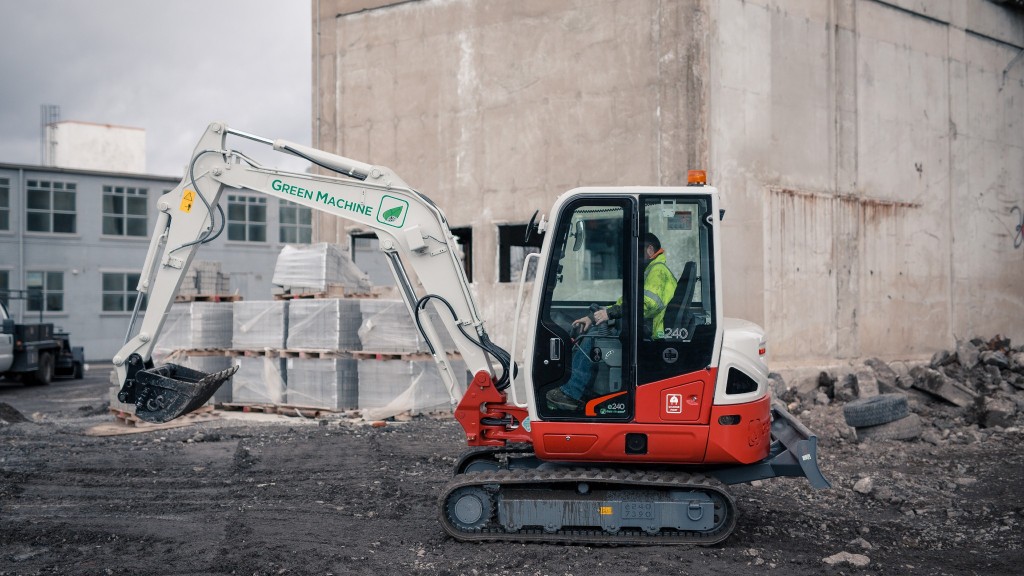
Innovation in battery-powered construction equipment has exploded in recent years, with most major earthmoving OEMs working on prototype or production-ready fully electric solutions for the compact earthmoving market. This can be an expensive, lengthy process involving extensive R&D investment, and these machines then come with a premium price tag, which can be up to double the diesel-powered counterpart.
Buffalo, New York-based Green Machine Equipment, Inc. came up with another approach – on a bet.
Eight years ago, Jon M. Williams, the soon-to-be founder of Green Machine and then-owner of OSC, Inc. and OSC Manufacturing & Equipment Services, Inc., was at a medical campus with the president of the campus and the president of a utility company. There was a diesel machine operating outside; it was noisy and they could see the emissions. On the spot they made a bet. If Williams could build a battery-powered machine to replace that diesel machine, the president of the utility would buy it.
A few months later, Williams returned with the machine, showing that it could run on its lead-acid battery. This proof-of-concept machine, affectionately dubbed "Frankenstein," was the launch pad for Green Machine.
Battery technology has since improved dramatically. Green Machine has switched to lithium-ion solutions and has continued to partner with utility companies to beta test new pieces of equipment. Kirk Durham, vice president of Business Development, said, "We would build to satisfy any problems they [the utility companies] found. We made [the battery] waterproof, we made it crush-proof, and we built this incredible box around it. . . we claim the whole space in [the engine compartment] to get the most energy density to create the longest run time."
The Green Machine process
Green Machine, along with its technology partner Moog, Inc., designs drivetrain solutions for OEMs. Whether that involves batteries plugged into existing hydraulics, smart hydraulics, system connectivity, or fully electric systems, Green Machine delivers OEMs electric solutions. In addition, Green Machine, in partnership with its OEM customers, provides end-users with Green Machine-branded equipment.
The partnership with Moog led to the development of a co-branded all-in-one engine and drive, WhisperDrive. This combined effort acts as a single customer-facing entity for both Green Machine and Moog, delivering innovation and cost-savings to OEM clients.
The machine design process, leveraging the capabilities of both Moog and Green Machine, results in a product that looks identical to its diesel counterpart. However, the Green Machine dramatically outperforms the original machine. Once the design is ready, Moog and Green Machine, through WhisperDrive, provide low-run production and design iteration at its 200,000-square-foot Buffalo facility.
"We design, engineer, build and validate [the equipment] in Buffalo. We do what I call kill testing where we test the drive system to the most extreme conditions and take the data to predict failures before they happen.
"We test all the batteries as far as charge, discharge, and the quality of the cell. . . we have some really good engineers on the electrical side, the chemistry side, and just the experience side that are constantly looking for new chemistries and new thought processes on battery systems and new ways to protect the technology from the rigours of the construction environment."
Green Machine's battery testing, development and technology partnerships have led to some of the largest OEMs in the world working with Green Machine and Moog.
Green Machine's footprint could be found on several introductions and prototypes at CONEXPO-CON/AGG 2020. Green Machine and Moog together partnered with Bobcat to unveil the first 100 percent electric compact track loader.
Bobcat also featured a skid-steer loader and compact excavator powered by Green Machine. In addition, Case Construction Equipment partnered with Green Machine and Moog to debut the world's first electric backhoe loader, codenamed "Project Zeus."
In addition to its work on OEM equipment lines, Green Machine partners with the OEMs to sell some machines as Green Machine-branded equipment, allowing Green Machine to private label some of the most visible and popular models in North America.
Green Machine's fleet includes a full line of mini-excavators in 1.7-, 2.6-, 3.5-, and 4.5-metric-ton sizes, a mini skid-steer, a light tower, and a towable backhoe. Green Machine directly sells, rents or leases this equipment and provides support for end users and dealerships to grow their battery-powered fleets.
The advantage of a Green Machine
Durham said that initially contractors liked to buy Green Machine products for interior demolition work, but began using the equipment outside.
Contractors found that their operators like Green Machine equipment for reasons beyond eliminating emissions indoors.
"It's very low noise," Durham said. "There's no smell or emissions, its very safe, they can talk on the jobsite and they don't have to yell."
He added that these workers tell him that these advantages are important because they significantly reduce the stress levels and dramatically improve safety of construction workers, operators and the general public.
"When you look at the worker, the labourer, the machine operator – it's very important to them – and nobody ever asked them that."
As for concerns about battery life, Green Machine batteries are engineered to last up to 10 years, or 2,200 full charge-discharge cycles (fast charging can shorten that life span). The 10-year life span is calculated based on the machine working a full day for 220 days out of the year. In reality, many machines don't put in that many hours. Some machines may even have a shorter life than the battery, in which case the battery can be removed and placed in a new machine from the same manufacturer.
Green Machine has built up a strong team that, according to Durham, gives the company flexibility that combines with innovation to bring numerous benefits to contractors and industry.
This article was originally published in Heavy Equipment Guide, Volume 35, Number 4.