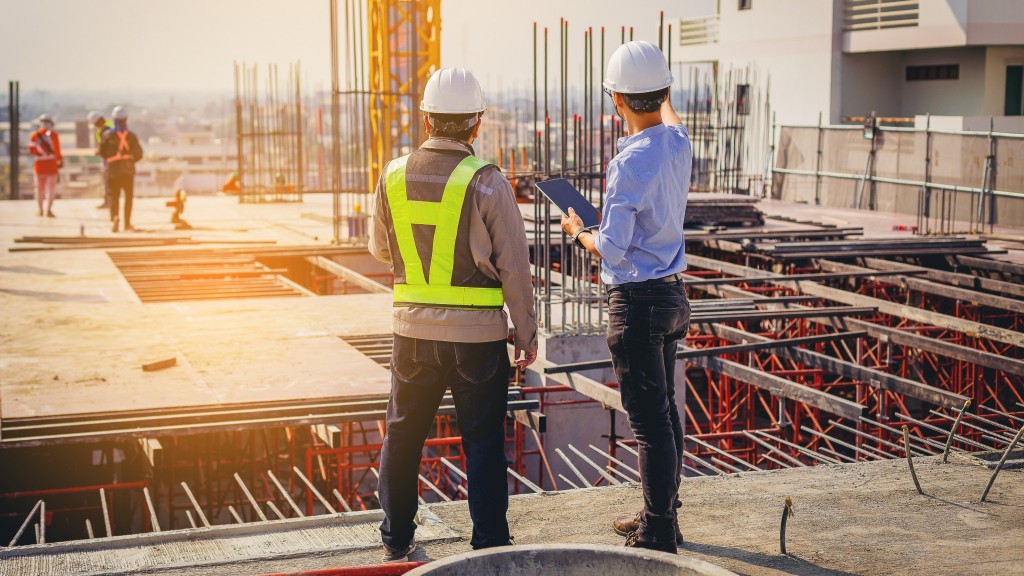
If you've ever wondered what type of data you should be collecting, look no further than the Dodge Smart Market Report. It lists the top five types of field data to collect from jobsites to best manage project performance: man-hours, safety, productivity, asset management and project progress. In the past, companies would rely on paper forms and spreadsheets to get hold of this information, but resource management solutions have made the whole process a seamless one.
These days, the question isn't whether or not construction firms should collect data – it's whether companies are effectively leveraging the live field data they collect. Using WorkMax Complete Suite, a cloud-based resource management platform with individual solutions to track labour, field reporting and equipment tracking all in the same app, businesses can easily collect and share the data for actionable insights. WorkMax integrates with all of the top construction accounting and ERP systems to keep projects on budget and on time. Here are the best ways to utilize the live field data to have the greatest impact on profitability with WorkMax Complete Suite:
Man-hours
Man-hours are the total number of hours it takes to accomplish a task and a key project performance indicator. Man-hour data can be easily collected in real-time throughout the day taking less than five seconds per instance, giving construction companies immediate insights into their team's man-hours per task and per project. This is a stark difference to the reality that almost half of contractors commonly have a 9- to 14-day lag between time entry and analysis.
Real-time man-hours can provide businesses with accurate man-hours that are regularly updated in the ERP with actual labour hours per task. The project budget is updated in real-time, so there is no data lag between collecting data from the field and assigning those man-hours to the right task on a project for analysis in the ERP.
WorkMax TIME is part of the WorkMax Complete Suite that makes it possible to compare man-hours against the total budgeted man-hours for each cost code in real-time to provide an accurate total number of hours spent per project. Regular updates give management the ability to pivot the workforce quickly when a project's man-hours are over or under budget. The sooner contractors know where their man-hours stand compared to the budget, the sooner they can take course corrections if a project is exceeding budgeted hours. Live field data also reveals who the most efficient workers are based on total man-hours. From those most productive members of the team, management can develop best practices for the entire company to follow.
Safety
WorkMax Complete Suite consists of individual solutions for TIME, FORMS, and ASSETS to simplify how contractors collect and share live field data to manage employees, equipment and processes to expedite field safety reporting. Safety information can be collected on easy-to-use forms at clock in/out and during task transitions. Each safety instance can also be associated with a piece of equipment used before being shared in real-time across the organization.
Safety forms collected with live field data gives supervisors and management immediate insight into any safety issues or trends that are happening throughout the company. Using embedded photos with markup, safety issues can clearly be communicated and can also be automatically shared across the company. WorkMax FORMS was built with this in mind, each jobsite safety manager can make sure any risks they encounter aren't repeated on their jobsite. By collecting safety data from individual employees, over time, construction managers can help teams avoid unnecessary injuries and avoid any compliance fines.
Asset tracking
If a piece of equipment isn't available to a team when it's needed, the work doesn't get done. Live field data can track the location and use of equipment on a project or across an entire company. Employees don't have to make countless attempts with phone calls, text messages and emails to locate a piece of equipment. WorkMax ASSETS uses live field data to give supervisors the ability to better coordinate the flow of work so the tasks that need to be completed will match the availability of equipment.
Live field tracking allows for equipment to be transferred between employees without any intervention of an equipment manager or returning the equipment to the equipment yard with mobile-to-mobile transfers. This ensures supervisors and employees always know where assets are and when they'll be available so they can schedule their time and resources accordingly. An accurate asset inventory with live field data also makes sure the asset life is extended by not overutilizing one piece of equipment while others remain unused.
Using WorkMax FORMS and ASSET together will uncover trends in equipment usage. Supervisors will be able to pinpoint when the maintenance of equipment is needed. This data also shows how equipment has historically been utilized, so managers can avoid the risks of unnecessary delays due to maintenance downtime.
Productivity
When it comes to productivity, the insights live field data provides can be used in different ways throughout the company to improve the bottom line. For example, data can show current and historical demands for labour from different tasks and projects.
By utilizing the robust integration between WorkMax TIME and the accounting or ERP system, contractors can mirror the project cost structure, increasing quantities completed report accuracy. The integration of labour tracking, quantity tracking and task tracking can be done seamlessly in one system when workers record their hours. As workers switch from one task to another or clock out they are asked simple questions about the quantity used and the task completion percentage of the job code they are clocking out of. The unit of measure for both can be customized for each task to make sure you're comparing apples to apples between the field data collected and budgeted quantities. Real-time tracking of a project's quantity percent complete in the ERP allows contractors to compare spending to the actual work completed.
Real productivity is tracked by comparing the quantities completed per task compared to the budgeted quantities coming from the integrated ERP system. Understanding any variation between the budgeted labour hours per task with quantities completed and the current productivity rates will help management adjust and pivot resources that cause costly delays that will cut into the project's profits.
Project progress
The overall progress of any given project can be tracked in real-time through live data submitted by workers and shift supervisors throughout their workdays using WorkMax TIME. Employees are prompted to select a task and that task data can then be compared against the job costs on the projected budget so companies get a bird's eye view of where things truly stand.
By using WorkMax, a company can run real-time earned value calculations (EVs). Accurate real-time labour costs and live task completion tracking gives contractors the right data to run EV calculations on projects on a regular basis to know if they've spent more or less time or budget based on how much work is done. This alerts management of any red flags on any projects and identifies positive or negative trends immediately so they may take the appropriate action swiftly.
With today's competitive construction landscape, it's not enough to collect data – companies need to collect the data that matters most, actionable data. Live field data for man-hours, safety, productivity, asset management and project progress can be immediately leveraged. This live field data enables companies to make sense of their situation, understand key patterns and get a window into the future so they may take action and set themselves apart from the competition. As these five areas of live field data increases, so too will the profit margins when you collect and share live field data all in one app with the WorkMax Complete Suite.
Mike Merrill is co-founder and chief operating officer of WorkMax.