Port upgrade requires big demolition job
Pacific Blasting & Demolition deconstructs three 100-year-old grain facility structures in Vancouver, B.C.
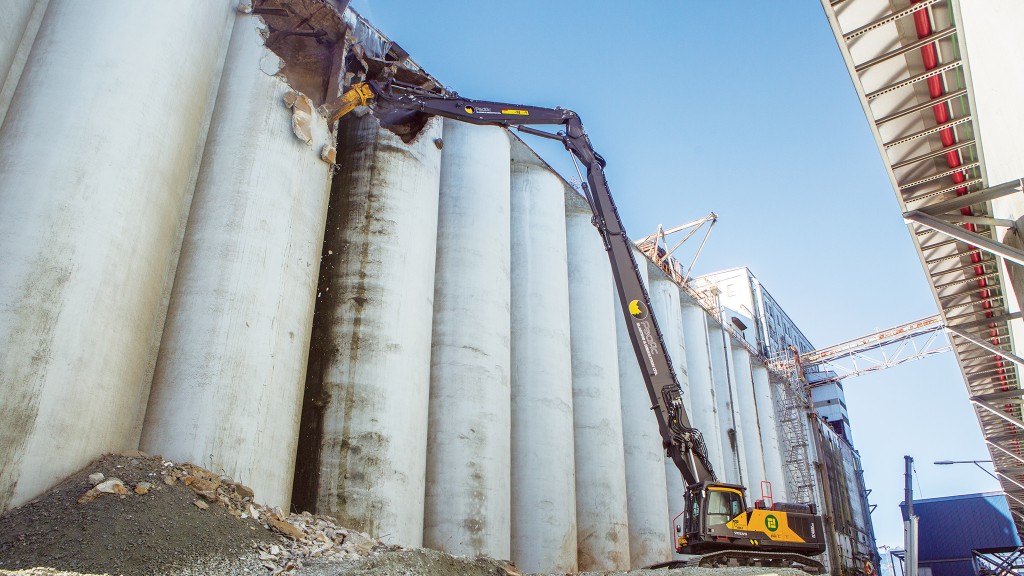
The deconstruction of the Pacific Elevator No. 3 (PAC 3) was required by the owner of the facility, Viterra Inc., as part of an overall upgrade at the Pacific Port Terminal in Vancouver, B.C. The deconstruction included abatement and demolition of three primary structures, including a railcar unloading building (track shed), grain processing building (workhouse) and grain storage silos (annex). The total building footprint was approximately 45,000 square feet.
The PAC 3 was built in 1918 at a time when Vancouver's port was developing as a centre for trade following the opening of the Panama Canal in 1914. In 2010, with the facility approaching 100 years of age, it was deemed unsuitable for upgrade due to building envelope integrity issues and was permanently shut down. To address any potential future safety risks and negative impact to neighboring infrastructure, the environment, terminal employees, the local community and ongoing port operations, Viterra determined that the facility should be demolished.
In 2014, National Demolition Association member Pacific Blasting & Demolition Ltd. was invited to participate in competitive bidding for deconstruction of the facility. A combination of an experienced project team, sound deconstruction methodology and competitive pricing – along with a reputation for successfully completing challenging projects safely and efficiently – resulted in the company being awarded the project.
In 2015, the project was put on hold while other key facility upgrades (including installation of a new, low-emission ship loader and the removal of the obsolete ship loading and conveyance systems) were completed. The project was rescheduled, and Pacific Blasting & Demolition Ltd. mobilized to the site in June 2019, working continuously until the project was completed in November 2020.
The overall strategy for this project was to complete the work safely and efficiently while maintaining the ongoing grain terminal operations. The project work was sequenced to meet these requirements and, where possible, abatement and demolition activities overlapped with the aim of reducing the overall project duration.
What made this project unique was that the demolition approach had to be tailored to address the complexities and characteristics of each of the 100-year-old structures. This included specific health and safety risks, access constraints, a limited working footprint, structural integrity considerations, the presence of basements and associated material management, and adjacent ongoing industrial operations, to name a few.
The demolition process
In advance of project commencement, a comprehensive planning phase was undertaken to establish safe work procedures for mitigating the potential health, safety and environmental risks arising from the abatement and demolition. Development of the detailed engineered demolition plan required extensive investigation, including confirmation of slab thickness and reinforcement bar (rebar) patterns to inform the engineering modelling that was necessary to determine the overall integrity and impact the demolition would have on the structures.
Once the project plans were in place, the on-site work started with the establishment of site facilities and installation of environmental and safety control measures, including safety barriers, fencing, temporary lighting, guardrails and signage as necessary to ensure that the project safety requirements were met.
For all structures, the first step was to complete an initial cleanup to remove residual grain and biological hazards. Abatement followed and included removal of asbestos (in roofing, flooring, gypsum, window mastic, mechanical systems, conveyance equipment, firestops and other miscellaneous materials), lead, mercury and other hazardous materials.
Demolition of the track shed was the first priority for the project, as it had the biggest impact on terminal rail operations, with the existing rail tracks having to be removed as part of the demolition works. The track shed, covering a footprint of approximately 10,000 square feet, comprised a steel structure with interior concrete block walls constructed to a height of approximately 40 feet with a 17-foot-deep basement. The biggest challenge with demolition of the track shed was that one of the perimeter walls was built along the property line of the adjacent busy container cargo terminal. Activities had to be planned around shifting schedules, which required real-time communication between all stakeholders and extensive coordination. Keeping the container terminal operational required flexibility to readjust scheduled activities as needed to maintain productivity. Given the proximity to existing operational rail infrastructure, ensuring that excessive vibration and movement did not occur was also critical. Geotechnical monitoring and survey specialists were engaged to monitor the adjacent infrastructure and ground during demolition, backfill and compaction activities and ensure that the work was completed without compromise to existing facilities.
Upon completion of above-grade demolition and backfill of the basement, two of three rail tracks originally removed to facilitate the demolition were reinstated. One track was located less than 20 feet from the workhouse and annex and had to remain out of service until all demolition was complete. With the two tracks back in operation, the project focus turned to the annex and workhouse areas.
Extending to a height of over 100 feet, the annex comprised a total of 77 concrete silo bins covering an approximate footprint area of 25,000 square feet. The initial project plan (pre-award) had been to use mini excavators and skid steers to complete the removal of roofing materials. Unfortunately, the pre-start engineering investigation determined that the roof structure could not support the weight of even small machines and the abatement and pre-demolition work had to be completed by largely manual means. To minimize the schedule impact from the change of method, a plan was developed whereby mechanical demolition of a portion of the structure could commence once abatement had been progressed past key portions of the structure. Following abatement of designated areas, the structure was demolished to grade using the high-reach excavator working from a stable pad. The presence of a 12-foot-deep basement meant that in order to progress above grade demolition, basement voids had to be progressively backfilled to support the high-reach demolition excavator. Concrete arising from the demolition of the upper structures was directed down the silo bins and into the basement as the interim backfill. Upon completion of above-grade demolition, the concrete was removed from the basement areas and replaced with a select granular subbase, which was subsequently compacted to meet project specifications.
Standing at over 165 feet tall with a 17-foot-deep basement, and an approximate footprint of 10,000 square feet, the concrete and brick workhouse was the tallest structure on-site and presented undoubtedly the biggest challenge to safe project execution. Given the height of the structure and space constraints around the building, a methodology was adopted whereby the upper five levels above the bin top floor had to be deconstructed floor by floor using a combination of manual demolition supported by smaller demolition excavators. Due to concerns with structural integrity, particularly related to the slab, the entire upper workhouse had to be shored, and all work was completed from swamp pads placed over structural beams. Shoring, equipment and tools were flown up and progressively moved between floors by crane.
Scaffolding was installed around the upper elevations of the workhouse structure and covered with debris netting to prevent materials falling from work areas. The scaffolding was progressively dismantled on a floor-by-floor basis as the demolition completed on each level. Once demolition of the upper workhouse was completed, scaffolding was removed and construction of an excavator pad for the high-reach excavator was completed in the footprint of the former annex area. Similar to the annex structure, concrete had to be temporarily placed in the workhouse basement to enable progression of above-grade demolition. Once completed, the concrete was removed from the basement and replaced by an imported and compacted subbase material. The project concluded with the reinstatement of the final rail track that had been out of commission for the demolition duration, thus reinstating the client's full rail capacity.
Expected and unknown challenges
A number of challenges were encountered during project execution, some of which were expected and others unknown when the project commenced. Undoubtedly, the biggest anticipated challenge was managing the health and safety risks to demolition crew and terminal workers. The safety risks to adjacent rail, shipping, grain terminal and container terminal operations had to be constantly managed during all activities. In addition, given the height of the working floors and thin concrete slabs, the potential for fall from height presented a significant hazard to workers. A full-time on-site construction safety officer managed site health and safety risks and ensured overall site safety by writing and reviewing safe work procedures and plans, ensuring equipment inspections were being completed, holding routine daily and weekly safety meetings, establishing heavy equipment exclusion zones, mentoring workers and ensuring training was in place, constantly inspecting work areas, and refining safety control measures as needed.
It was known that potential structural integrity issues were likely given the age and nature of the structure, particularly given that the main buildings had been constructed during World War I at a time when labour and materials, particularly steel, were in high demand. During demolition, cold joints were encountered between some of the working floors, and it was identified that the columns and beams in the upper workhouse levels had less rebar than would be expected for such a structure. As a result, the demolition approach had to be constantly reevaluated by the engineering team to ensure that all methodologies were appropriate and safe for the conditions being encountered.
One of the greatest unexpected challenges presented during project execution was the official declaration of COVID-19 as a pandemic by the World Health Organization on March 11, 2020, and subsequent declaration of a provincial state of emergency in British Columbia on March 18, 2020. As a result of the declaration, crew numbers dropped significantly as workers chose to stay at home and isolate even though the project had been deemed essential work and was able to continue. Health and safety protocols and procedures were revisited and revised to address the new risk associated with spread of virus, and control measures, particularly relating to social distancing and worker hygiene, were implemented. Supply shortages, particularly disinfectant and cleaning materials, provided an added challenge to maintaining project activities. In addition, the emotional impact of the pandemic was not something that had previously been experienced, and crew distraction, fatigue, stress and fear associated with the virus had to be managed constantly to ensure that it was safe for work to continue.
A successful job is ultimately one that is completed safely while meeting the clients' objectives and expectations. Through effective application of sound project plans, team collaboration and proactive communication, the experienced Pacific Blasting & Demolition Ltd. project team safely demolished the PAC 3 structures with minimal impact to the clients' ongoing operations.
The experience of the project team and the positive working relationship with Viterra and its lead consultants, particularly Ausenco Global Consulting Transportation & Logistics, allowed Pacific Blasting & Demolition to successfully navigate the project challenges and constraints resulting in an overall successful project.
Katherine McCann is a project manager with Pacific Blasting & Demolition Ltd.
This article was originally published in the July/August 2021 issue of DEMOLITION magazine. It is republished here with the permission of the National Demolition Association.