Sodextra S.A. recovers 70 percent of waste with new CD&E recycling plant
Wet processing solution from CDE a first for the French waste management company
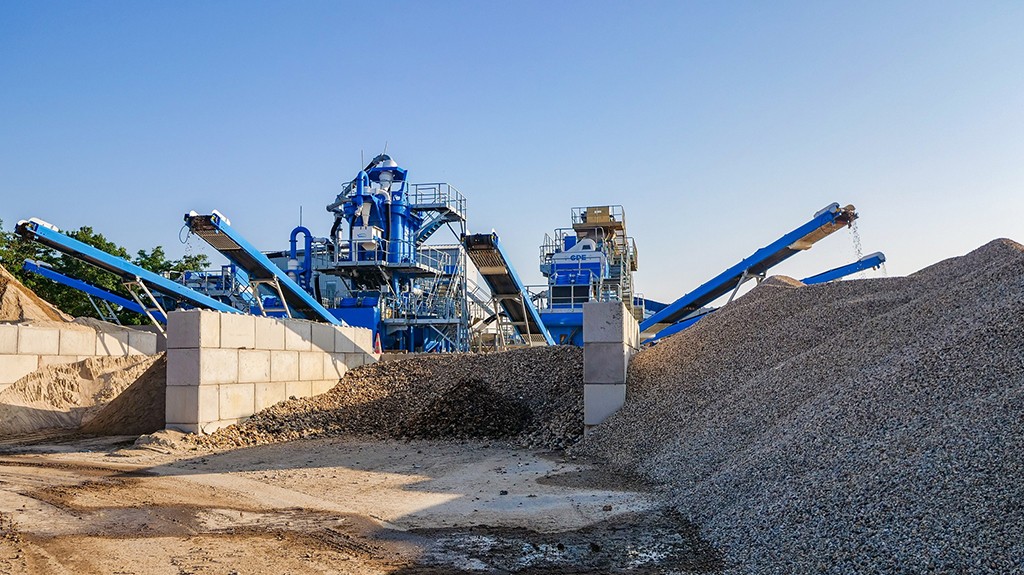
French waste management company Sodextra S.A. has invested in a made-to-order construction, demolition and excavation (CD&E) waste recycling plant from industry experts CDE, marking its first venture into the wet processing of materials and enabling the recovery of up to 70 percent of incoming inert CD&E waste. The new plant is currently processing material at a rate of 135tph, producing six sand and aggregate products, and opening up new markets for the family owned and operated business.
Based along the Plateau de Saclay, 15km south of Paris, Sodextra operates a major construction waste recycling treatment facility, situated on an eight-hectare site, that supports construction professionals to deposit and process waste and rubble in the Paris region.
Established in 1975, the business has, for over 45 years, facilitated the diversion of significant tonnages of CD&E waste from landfill, assisting in the recovery of a variety of high-value construction materials, including recycled sand and aggregate products, and returning them to the sector for use in major public works and infrastructure projects.
Its primary market sectors are the recovery of deconstruction concrete, the recovery and treatment of industrial waste and the sale of ready-mixed concrete.
Maximizing recovery from inert soil
Currently, the third generation family business recovers one million tonnes of material from waste per year, a substantial volume it hopes to increase further as a result of its latest investment in CDE technology which is now enabling the recovery of inert soil.
Sacha Bottemanne, Directeur Général of Sodextra S.A. and son of its owner, Christian Bottemanne, said the company's biggest challenge was treating highly variable waste coming into the facility.
"We used to screen the soil and we could recover about 20 percent of the pebbles which were reused in our crushing plant. The remaining 80 percent was dumped. We realized that in this 80 percent there were still materials with high added-value which today, with the CDE installation, we can recover."
Based on the analysis of the soil from around the Saclay plateau, CDE's Business Development Manager for France, Marc Sopransi, quickly realized the challenge presented by the processing of the very heterogeneous and heavily clay-bound material.
"Sodextra approached us to find out how to further recover their inert soil, to find a way to recover more sand and gravel and turn them into high value-added construction materials," said Sopransi.
He added that going from "a wide spectrum of multiple raw sand feeds to be processed to a regular spectrum, as narrow and as stable as possible, of clean 0-4mm sand, was at the heart of the problem."
CDE's solution
To demonstrate the potential for CDE technology to support Sodextra to recover high grade and high value products from its waste, the Sodextra team were invited to a CDE reference site in Germany to see the technology in action.
"We saw the materials that went into these installations, which were of very poor quality, very sticky and full of diverse contaminants such as plastics or roots...we really saw the process and the quality of the materials coming out. That's why we decided to go with CDE," said Sopransi.
Samples of feed material to be processed by the plant were tested and analysed by CDE process engineers in its laboratory to determine the reclamation potential of the incoming waste stream and the quality of its output.
The plant incorporates a combination of CDE signature modular technologies, including the AggMax modular logwasher setup for scrubbing and sizing and EvoWash sand classification and dewatering systems with integrated patented technologies, including CDE's Infinity Screen and Counter Flow Classification Unit (CFCU) for density separation, which efficiently separates materials of differing specific gravity to maximise the quality and value of feed stock.
Commenting on sand treatment, Sopransi said the solution engineered for Sodextra is unique. "It consists of a first cyclone pass, attrition cells, a second cyclone pass, a hydraulic classifier, and a third cyclone pass with two major classification points placed at 250 microns and 2mm. This sand treatment provides a dynamic response to a dynamic problem.
"The type of sand treatment in this application is a first in Europe," he added. "It originality lies in the fact that the solution uses technologies usually used in the treatment of industrial sands."
Effective water management
The solution designed for Sodextra not only allows for the recycling of CD&E waste, but it also maximises water efficiency with CDE's AquaCycle, a single, compact, and user-friendly unit that can be applied to high and low tonnages across many markets.
An alternative to water extraction and the costly process of pumping water to the plant, CDE's AquaCycle is a highly efficient water management solution that minimises costly water consumption by ensuring up to 90% of process water is recycled for immediate recirculation.
Delivering competitive advantage to its customers, CDE's AquaCycle accelerates return on investment by maximising production efficiency, minimising the loss of valuable fines, and reducing water and energy costs.
After feed material has been washed and classified, the waste water is sent to the AquaCycle thickener system. Here, a small amount of polyelectrolyte flocculant is added to the water via an automatic dosing station which forces fine particles to settle on the bottom of the thickener tank. The clean water on the top overflows the weir and is stored in the AquaStore tank before being re-circulated around the plant. The result is a highly efficient water recycling system that requires only a 10% supply of top-up water.
Waste sludge is discharged into a buffer tank where agitators in constant rotation ensure the material does not settle and solidify at the bottom.
For Sodextra, the high quantity of sludge generated by the raw material process meant that the use of a Filter Press was necessary in order to avoid settling ponds. Its integration also facilitated the recycling of even more water from the process. Filtrates recovered and redirected to the company's new AquaCycle have enabled Sodextra to achieve a water recycling rate of approximately 96%, significantly reducing the need for top-up water supplies.
70 percent material recovery
Sodextra's new plant is processing material that was once destined for landfill and producing a range of products, including three different sands: a fine sand 0-250um, a 0-2mm and a 0-4mm; and three different aggregates: a 4-10mm, a 10-20mm & a +20mm aggregates, all ready for use in construction projects in the Paris region.
"Our CDE installation produces high quality aggregates that we now call ‘eco-gravel' or ‘eco-sand'. These are very high-quality materials that are similar to natural materials," explained Bottemanne.
A filter cake product from the integrated CDE Filter Press can also be reused as a waterproofing layer or for pipe bedding and landfill capping.
"Today, the CDE installation allows us to recover 70 percent of the waste and to create new materials that are reused in construction sites throughout Greater Paris."
Bottemanne added that Sodextra was established when his grandfather recognized the need for C&D recycling in the Greater Paris area. "Sustainability is in the very fabric of our business. It was founded on the same principles it operates today and we remain committed to closing the loop. Our customers are increasingly concerned about the environment. With these new materials, we are contributing to the circular economy and to sustainable development."
Sodextra's new plant is the culmination of over two years of site audits, lab-based research on materials and collaborative design workshops, whereby the CDE co-created the engineered-to-order solution with the Sodextra team.
"Between the beginning of the project to the final phase, we were in touch with our ProMan who followed us throughout, who supported us and who also guided us," explained Bottemanne. "Today the relationship we have with CDE is going very well because we've really entered into a partnership."
Sopransi said the plant has now been operational for a full year and has successfully met all of Sodextra's objectives. "To further revalorise inert soil, to provide aggregates eligible for concrete specifications, and to realise an installation that took the minimum of space."
He added CDE is committed to the region and has recently expanded its CustomCare team locally, which provides after sales support to guarantee customers get the maximum performance from their CDE equipment.
"CDE has set up a support and services engineer in France who will be available to provide responsive, boots-on-the-ground support to our customers in the region, including Sodextra as they continue to provide a valuable service to the local construction industry."