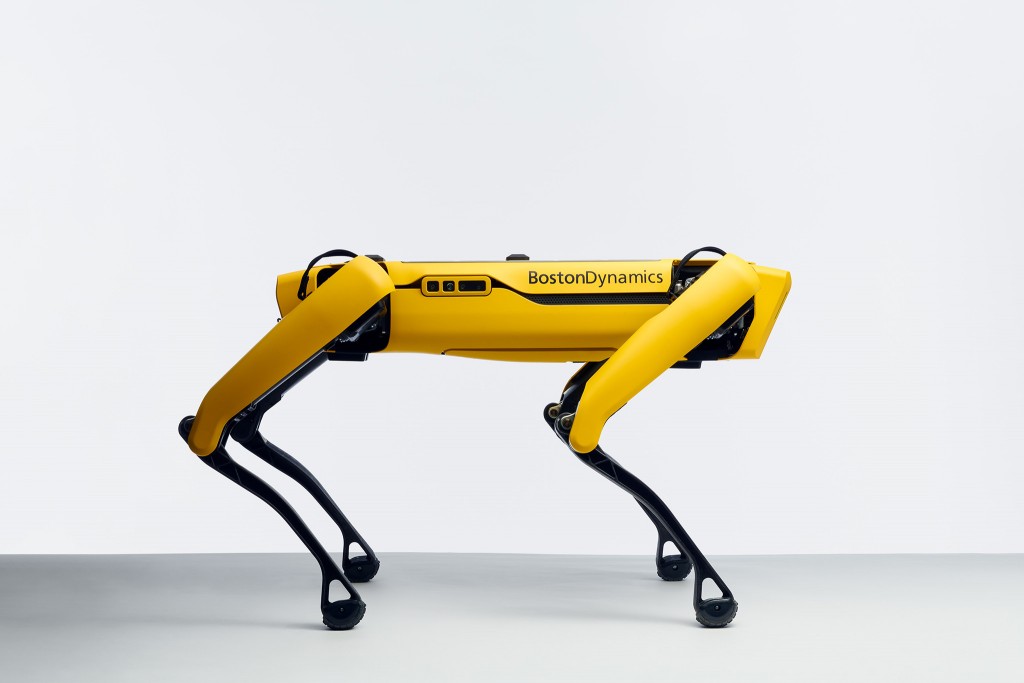
Modern organizations use data to drive their business decision-making. This data can come from a wide variety of sources, and for industries such as manufacturing, energy, and oil and gas, IoT sensors and operators' rounds and readings have long been the leading options. However, in the past couple of years, these industries have started to turn to a third solution, which offers greater coverage at a fraction of the cost – dynamic sensing through agile mobile robots like Spot.
Spot moves from asset to asset across a facility to get real-time information on equipment including pumps, motors, compressors, and more, so plant managers can improve uptime while decreasing costs of downtime and maintenance. With Boston Dynamics' newest software release, Spot Release 3.2, the company has made enterprise asset management easier than ever. This release adds built-in data processing and review, improvements to the data collection pipeline, and a better operator experience.
Built-in data processing and review
In addition to offering tie-ins to third-party data processors, we now offer out-of-the-box processing capabilities for thermal inspections, as well as data plugins through a Scout API.
Thermal imaging – collection and analysis
With the Spot CAM+IR, Spot users can perform detailed thermal inspections during routine autonomous missions. The new thermal inspection capabilities allow operators to get more data on the health of their assets, see results, trigger alerts when assets go out of bounds, and see data trendlines on Scout. New tablet controls allow users to set minimum or maximum temperatures on regions of interest, triggering an alarm through Scout if breached. Users can also adjust span and level and adjust the colormap of thermal images.
Thermal data and trends are then easy to review and manage in Scout and users can select email or mobile alerts when equipment goes out of set bounds. These new data processing features will be key to enabling users' asset maintenance programs.
The Scout API
In addition to providing thermal data processing in Scout, for the first time ever Boston Dynamics is releasing a Scout API. The Scout web API allows users, developers, and integration partners to access data from any Autowalk mission or manual operation session run through Scout. This new API provides methods for querying the data collected by a site's Spot fleet over time. It can be used to filter and sort results by a number of fields, including mission name, robot name, time, and mission result. These querying capabilities of the API can be leveraged to create targeted reports, such as reports on specific assets. Users can also use the API to export data from Scout to another system, such as their preferred enterprise asset management system, in order to further integrate Spot into their data workflow.
Improved data collection
Not only has Boston Dynamics added data processing with Release 3.2, but they've also made data collection with Spot easier through some new autonomy features.
Arm inspections
The Spot Arm gripper camera is available as an additional inspection tool. The arm and its 4k camera can help users get a better look at inspection points that are higher up or hidden behind other objects. Arm inspections can be performed manually or as part of an autonomous mission.
Area callbacks
Boston Dynamics has added the option to trigger an action when Spot walks through specified areas on its mission map. In areas where certain checks or actions must be performed for the robot to navigate safely, Area Callbacks provide a new option to ensure actions are always performed at the correct place during autonomous navigation. The action will be performed in the area regardless of the actual sequence of events that caused the robot to end up travelling that route (normal operation, rerouting due to a blocked path, returning to a dock to charge the battery, etc.). Area Callbacks can trigger actions such as waiting at a factory crosswalk until it's safe to cross, flashing lights or playing sounds, and more.
Strict path following
Users can now set Spot Autowalk missions to use a strict path following mode. When this mode is active, the robot will follow the recorded path closely during Autowalk replay and will not deviate from the path to walk around obstacles. This mode is for users who want Spot to stay within a tightly constrained path, such as a pedestrian walkway in a factory that also includes vehicle traffic (e.g. forklifts) or other hazards. This mode is also intended for users operating Spot in an environment – for example, a nuclear power plant – where deviating from the path could present safety risks.
Ground clutter avoidance
Ground clutter avoidance is an optional feature that restricts Spot from stepping on or over new objects or people on the ground during mission playback. This feature is designed for sites where sensitive equipment may appear on Spot's inspection route.
Enhanced operator experience
Operating Spot and getting support should be easy. In this release, Boston Dynamics has added automatic stairs registration and refined our support systems for logs and licenses.
Automatic stairs mode
Spot can now automatically detect stairs and switch itself into stair mode during both manual operation and Autowalk. Operators will no longer need to manually switch the robot into stairs mode.
Connected logging and licensing
When Spot detects an issue, the robot logs data on its performance. With 3.2, users can identify and directly upload small event logs to Boston Dynamics for faster and more streamlined support and assistance. The updated system includes:
- Smaller log file sizes for easier handling and faster transfer
- One single log file for each issue the robot encounters
- Optional direct upload to Boston Dynamics
A network-connected Spot can also fetch its annual license. Spot users are able to update to release 3.2 now.