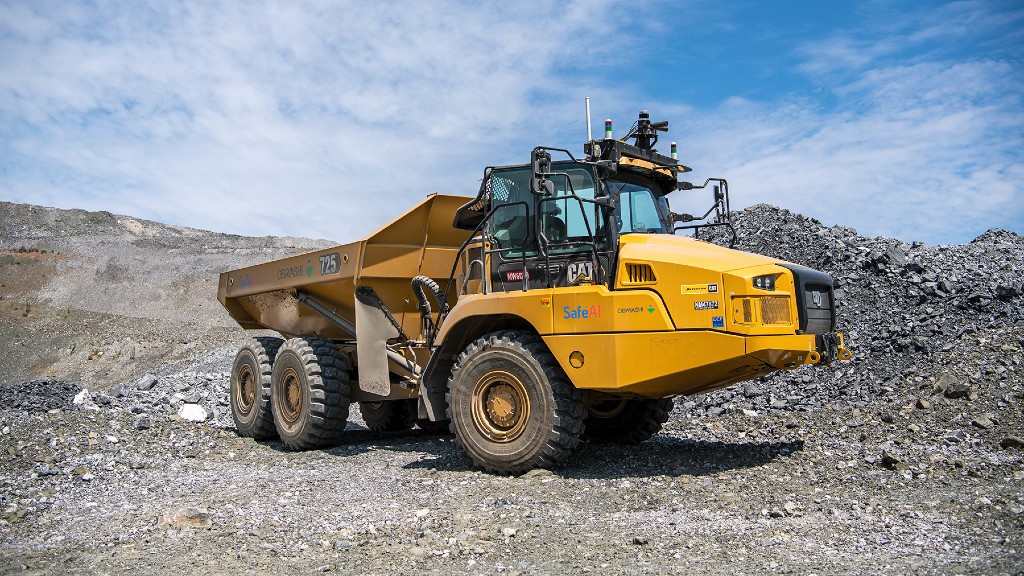
It's hard to ignore the increasing attention autonomous construction equipment is receiving.
Just in the past year SafeAI and Obayashi Corporation demonstrated a retrofitted autonomous Cat 725 articulated truck, Shantui developed an unmanned dozer, SRI International released a video on its prototype robotic excavator, Autonomous Solutions, Inc. (ASI) partnered with Epiroc Drilling Solutions on its Mobius autonomy platform for drills, and Trimble introduced its new automatic steering control for soil compactors.
Will we ever get to the time when humans are rare on a job site? And is that even the point?
The autonomous transition will follow automotive gains
All industries, including construction, have been the beneficiaries of U.S. defence research, says Bibhrajit Halder, founder and CEO of SafeAI. This included the DARPA (or Defense Advanced Research Projects Agency) Grand Challenge in the early 2000s, designed to accelerate autonomous vehicle technologies.
"That was a trigger point," says Halder, whose company concentrates on bringing autonomous solutions to construction and mining. "It was a massive success that really sparked autonomy in this country."
In 2014, the Society of Automotive Engineers established six levels of autonomy, going from Level 0, indicating vehicles with completely manual controls, to Level 5, in which there is zero human interaction in operating a vehicle.
"No one has a true Level 5 system yet," says William Nassauer, manager of product strategy for Komatsu America's autonomous systems and mining technology solutions. That assessment, of course, includes the automotive sector, which, although it is leading the autonomous journey, has had significant bumps along the way.
As it has with cars, construction equipment will transition from assist features to task automation to task autonomy. The now-commonplace operator assists, such as blade and bucket controls, require sensor basics that are steps along the automation journey.
But equipment automation should be considered in the context of total job site autonomy, with several autonomous machines working in concert, says Fred Rio, product manager for construction digital and technology at Caterpillar.
"On a job site," Rio continues, "all machines have a shared mission, and no one machine can accomplish it without the other machines. The true quantum step in value will be when you can get them to all work together."
Retrofitting existing machines to take the operator out of the cab
Several companies – including ASI, Built Robotics, SafeAI, and Teleo – are building retrofit kits that take the operator out of the cab.
ASI defines three different types of operator-out-of-the-cab controls: remote control, where the operator is in line-of-sight of the machine they control; teleoperation, or non-line-of-sight operation that's still one operator operating one machine; and autonomy, in which an operator can remotely oversee the operation of an entire fleet of machines.
Teleo's supervised autonomy retrofit is specifically designed to include operators, according to co-founder and CEO Vinay Shet. "We're combining the best of both worlds – the experience and expertise that their operators have with the advancements in technology," he says. "This is letting their operators do a lot more than previously."
The company, which has partnered with Deere dealer RDO Equipment among others, is now beta testing its system on North American job sites.
How does autonomous technology work?
Today, autonomous machines are propelled by several systems working together.
The SafeAI retrofit system, for example, uses off-the-shelf hardware (LiDAR, camera, drive-by-wire system, radar, computer, and vehicle-to-everything communication) and combines them with its proprietary autonomous vehicle and site operations management software.
This gives the vehicles location, perception, and direction. Working from a cloud-based project model, a staff member generally orchestrates the operation, Halder says.
SafeAI said it's bringing "Autonomy 2.0" to the heavy industry, using a process that doesn't rely completely on GPS and network availability and offers mixed fleet capabilities.
The human element of autonomous technology
"The change management is significant in adopting autonomous machines," Caterpillar's Rio says.
Because of their autonomous experience in mining, Caterpillar, Komatsu, and ASI have developed a structured approach to onboarding the technology to their users.
"Our customers are going to be changing mentalities," Nassauer says. "They've got to maintain their site in a different way, use workers in different ways and transition operators into supervisory roles. There's a lot of learning involved."
Understanding a job site – including what each machine is doing each day – and how the inputs and outputs work is an important step in becoming autonomous, said Michael Gidaspow, Komatsu America's vice president of products. "They'll have to give the machines specific instructions on exactly where and when to go," he says.
To be attractive, autonomy must also be ultimately easier to use, says Wood. "We don't want them to go and hire a whole group of IT specialists; there's no point in it being more complex."
As part of the move towards autonomous, Built Robotics envisions a new job: Robotics Equipment Operator (REO).
"50 percent of this effort is developing the robot and 50 percent is how you deploy and get people to manage it effectively," Ahmed says. "REOs are the people on the front lines. They go through a 30-hour training to run and manage these machines."
The company has partnered with the International Union of Operating Engineers to offer this certification to its members.
Niche machines zero in on specific tasks
In addition to autonomous machine research, some are investigating job-specific robotic units.
For example, ULC Technologies' Robotic Roadworks and Excavation System (RRES) uses a robotic arm on a tracked undercarriage to do a multiplicity of tasks aimed at performing precision bores in complex underground utility repairs.
"It automates this operation, from above-ground scanning and identifying where the underground assets are to reinstating the road when the job is done," says Ali Asmari, director of infrastructure automation and AI at ULC Technologies.
After scanning, the onboard software creates a 3D model of what's underground that guides the rest of the operation. The sensor box is then swapped out for a variety of road cutting, air, vacuum, repair, and backfill tools.
Although the RRES was created for one utility company, its applications are broad, Asmari says. ULC is actively pursuing new opportunities with other companies, including how each of the tools can be used separately.
Will we reach the point where no humans are needed?
Will construction ever see a "no-entry" site where no humans are on the job, or indeed, necessary?
Perhaps, said Halder, but it's still years away. But, there will be a tipping point.
"The moment one contractor completes a $100 million project for $80 million because of autonomy, it's game over," Halder says. "Everybody has to do it because you can't compete anymore."
"The industry is absolutely massive, the pain points are huge, and it's early days for autonomy," Teleo's Shet says. "To be honest, there's not enough companies doing what we're doing."
"There's a huge appetite and interest in autonomy," Ahmed agrees. "Maybe construction needs to develop its own set of autonomy goalposts, ones that are specific to its needs and show that each level is valuable."
Watch SRI International demonstrate its robotic excavator prototype
Company info
1025 Tristar Drive
Mississauga, ON
CA, L5T 1W5
Website:
epiroc.com/en
Phone number:
289 562 0100
Park, No.58, Highway G327
Jining City, Shandong Province,
CN,
Website:
shantui.com/group/en-us