Safer drilling: robotic rod handler keeps crew away from danger zones
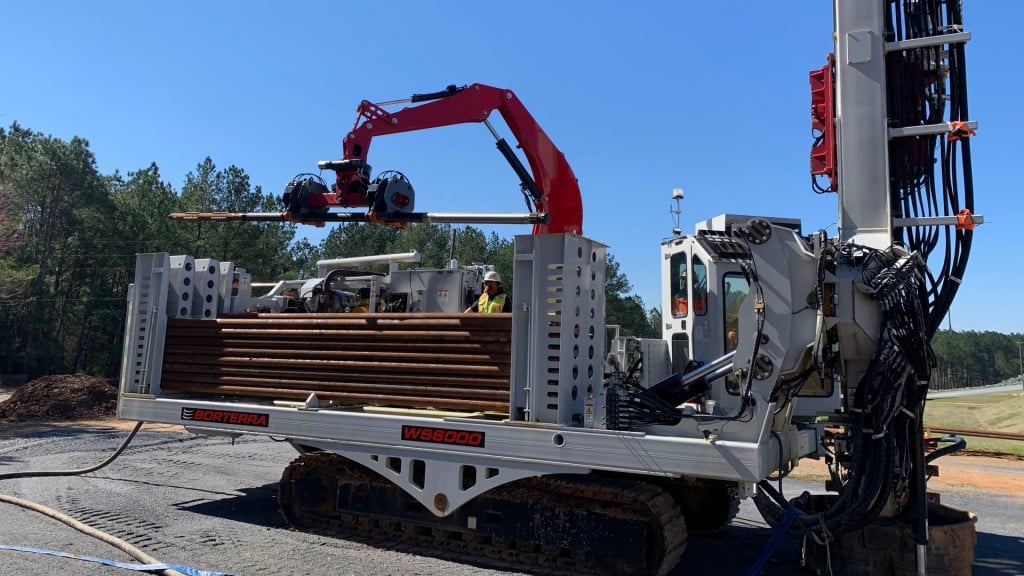
Rod handling in drilling operations can be a dangerous job, and moving crew members away from that task generally improves safety. A new robotic system is designed to reduce the number of people needed on the drill rig while also providing increased productivity.
RodBot, created by MEDATech's Borterra drilling division, is a hydraulic, robotic pipe handler for loading and unloading drill rods and casing in mining, construction, and oil & gas operations. It can be adapted to work on virtually any piece of drilling equipment.
When mounted to a rig, pipe truck or on a skid, the RodBot tool is easy for operators to work with, as it is computer-assisted and includes collision avoidance capabilities.
Rod and casing handling is one of the more dangerous parts of a drilling operation. According to MEDATech, this part of the process is responsible for more than 90 percent of drilling-related injuries. This manual work - inserting and extracting rod and casing - usually requires a crew of two or three, moving heavy metal cylinders from rack to drill head, or vice-versa.
"Moving drill pipe in and out of the mast can be the bottleneck in the drilling process," said Scott Dalrymple, MEDATech Senior Design Engineer & Product Manager for Borterra. "Until now, there has been no mechanized system that can do it as quickly as people can. But the very nature of the job makes it fraught with potential for injury."
RodBot picks up pipe and casing or puts it into the cradle with a grapple that is precision-controlled. Once the operator has manually steered the pipe or casing to or from the mast, they can essentially hit ‘repeat' and the unit adds or removes rod or casing as needed. It has three control modes: Full Manual, where the operator controls the movement every step of the way, to Autonomous Control with Collision Avoidance.
In the latter case, RodBot is programmed with "go" and "no-go" areas - zones that are safe to operate and others where it is not. The operator can program a start point and end point, and the robot will calculate the most efficient path, including navigating around defined obstacles using built-in collision avoidance software.
RodBot can be retrofitted onto most rig configurations.