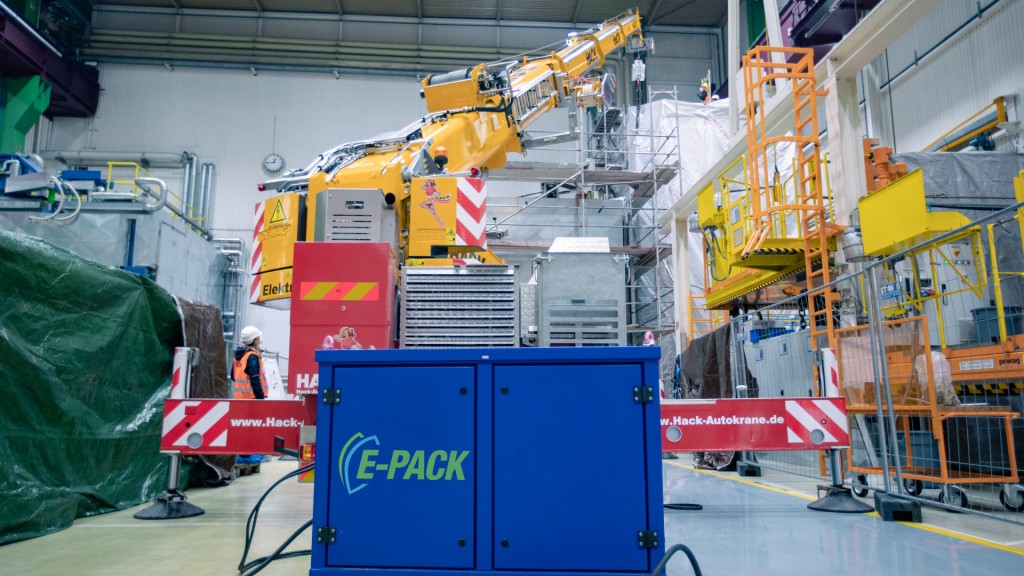
Lifting heavy loads inside a building is a challenge that crane operators face on some jobs. Lifting in a clean room hall is a step up, and for one German contractor required bringing some innovation to the table.
Hack Schwerlastservice GmbH was recently called on to handle heavy equipment lifts in Hitachi Energy Germany's Bad Honnef plant. Thanks to the location within a clean room hall, the job was limited - no internal combustion engine emissions allowed.
So, Hack turned to its Tadano AC 3.045-1 City crane, and paired it with Tadano's E-Pack to tackle the challenging indoor assignment. Compact and maneuverable, the AC 3.045-1 City has a lifting capacity of 45 tonnes. Hack added the machine to its fleet in mid-2022, and the addition of the E-Pack allowing for zero-emission operations indoors has helped the company move forward with its plans for indoor work.
"Without the E-Pack for the AC 3.045-1 City we wouldn't have had a hope of getting this job done," said Udo Hack, managing director of the heavy-transport firm.
On the job site, Hack's team moved the E-Pack directly into the hall, using an electric lift truck, and followed with the crane itself. Moving the crane into position was somewhat more complicated, as the direct route was too tight even for the AC 3.045-1 and its compact dimensions, at just over 11 metres in length and 2.5 metres wide.
Positioning the crane required patience, and a squeeze through a door barely 3 metres wide, but once in place the overall setup was quick and easy. The entire process from start to finish - including connection of the E-Pack - took about 30 minutes.
"The customer originally wanted us to fit the AC 3.045-1 City with a runner, but in the end the compact overall height of the hook block meant we didn't need to," Hack said. That meant that the crane was able to operate in its standard configuration, handling all lifts including those just below ceiling height, safely and securely.
Located in one corner of the hall, the crane did have to telescope in and out for each lift, which resulted in lower lift capacities.
"Some of the components we had to lift, pipes and concrete parts weighing up to 12 tonnes, exceeded the crane's lifting capacity," said Hebert Schellberg, a Hack project manager. To get past that issue, some components being moved had to be dismantled by the Hack team and plant engineers on site before lifting to reduce overall weight.
Working with the E-Pack aided in keeping disruption to a minimum as Hack progressed through the project. Powered through a connection to the grid, the E-Pack transforms the crane it's connected to into a zero-emission and low-noise unit. That means no fuel or diesel exhaust fluid is used, which cuts operating costs significantly. It can be transported to the job site on a trailer towed by the crane itself, or optionally on a transport rack. Either way, the unit does not require separate transport to take it to the job site.
The crane draws only as much electrical energy as it actually requires in order to perform the tasks at hand. This results in lower operating costs in comparison to a diesel system, and in addition reduces the number of operating hours for the latter.
Thanks to the combination of the AC 3.045-1's lifting capabilities and the zero-emission benefits of the E-Pack, Hack was able to complete the job on time and met the customer's requirements.
"With their Tadano crane and its absolutely ingenious E-Pack, the Hack team did a fantastic job. We were most impressed that they could operate a crane electrically and hence without emissions, and still get such great performance out of it," says Frank Urfey, the industrial engineering manager at Hitachi Energy Germany.
For Hack, the E-Pack has proven that it can handle the indoor work the company wants to focus on in future.
"Clearly, our decision to order the Tadano AC 3.045-1 City complete with E-Pack was absolutely the right one. Using the E-Pack is simply the best way to go for production hall jobs like this," Udo Hack said.