What is the connected job site?
How technology connects people, machines, and materials for a total overview of the job site from bid to execution
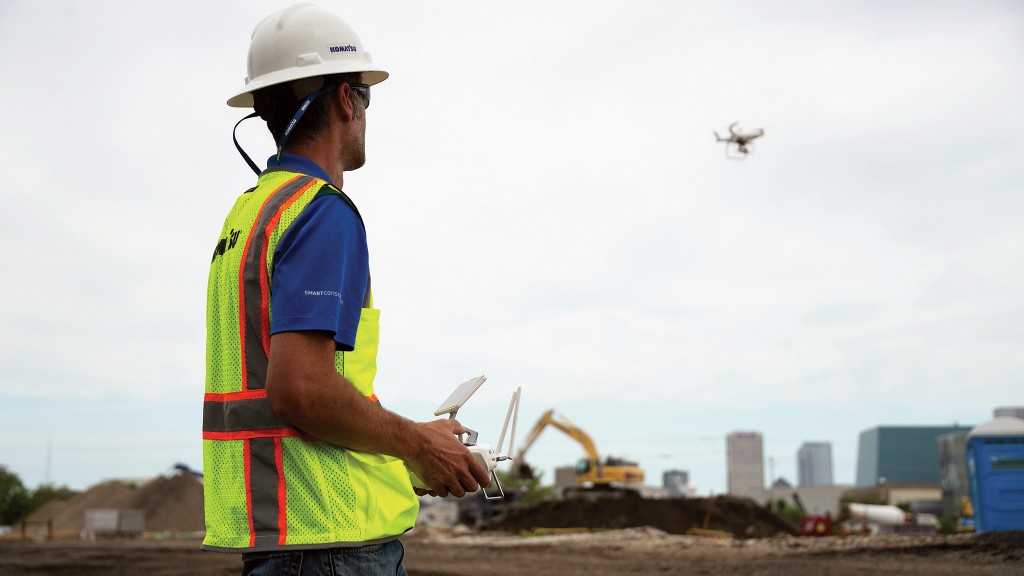
As contractors have to do more with less, adopting new technology can be anxiety-provoking – and complexity is often assumed. In reality, connected job site tools are designed to gather all job site information in one place, which simplifies processes for contractors and delivers deep insight into the day-to-day progress of their projects while eliminating information silos. Komatsu is one manufacturer that has expanded into this technology service with its Smart Construction platform. Let's demystify what the connected job site is and explore Komatsu's Smart Construction.
What is the connected job site?
The connected job site consists of data gathering and tracking of machines, materials, and people to plan, optimize, and execute a construction project from surveying and design to completion with ability to continuously monitor progress and analyze for efficiency and actionable insights. The connected job site combines surveying data from total stations and drones, machine control, payload measuring, and daily job site activities of workers for a comprehensive real-time record of the project that can inform day-to-day decision making. These technology solutions connect the job site with the office to provide comprehensive insight into the project.
These tools aren't just for the biggest contractors. Ron Schwieters, senior product manager at Komatsu, says that a key market is small- and medium-sized contractors who don't already have extensive connectivity capability in-house. Komatsu's Smart Construction cloud-based technology simplifies data and collection for these customers through a range of different modules that fall under the Smart Construction umbrella. With these modules, customers can link processes to optimize their fleet deployment, manage people, track materials, track machines, monitor project progress, and more all in one ecosystem. These tools enable contractors to manage the project from the bid process to planning to execution in one place.
The connected job site builds out from machine control
Connected job site tools start with the data that flows from machine control on heavy iron.
Machine control is intended to deliver productivity increases – but sometimes projections don't fully materialize. With a more comprehensive connected job site, a contractor can see where efficiency is lost. For example, perhaps an excavator operator is hitting their targets, but the trucks intended to meet that excavator aren't matching its pace. Flowing all data into one dashboard can provide insight into where and why a job site is and isn't efficient.
In a connected job site ecosystem, that data doesn't just have to come from heavy iron, trucks, and total stations – drones provide valuable overview and tracking of a project's progress in conjunction with the data that flows from earthmoving machines.
"If you fly a drone over a site, you've got a great understanding of where your site is today," says Schwieters. "But after two hours of bulldozers and excavators working, that data is out of date already if you don't have [machine control] data flowing back to your dashboard. So, combining drone and machine data can give you the most accurate view of your job site."
Komatsu's Dashboard, the hub application for reviewing Smart Construction data in the office, is designed to combine the drone data with machine data for review of volumetric production measurements that compare different phases of the project, 3D design data, stockpile measurements, cut/fill colour mapping, and more.
Seamlessly connect to equipment from the office
With Smart Construction Remote, customers can send 3D files to their machines from the office – but that equipment doesn't have to be a Komatsu iMC (intelligent Machine Control) machine. This technology will work with all of the major machine control providers, including Trimble, Topcon, and Leica, and Schwieters emphasizes that Komatsu's Smart Construction ecosystem is compatible with mixed fleets.
In addition to sending files, end-users can remotely troubleshoot equipment from the office with a view of the operator's interface and have the ability to take control of the interface remotely. Schwieters says that Komatsu's Remote capability is its most utilized Smart Construction tool right now because it is easy to implement and ties in with the popularity of machine control.
Humans, machines, and materials connected in the field
Komatsu's Smart Construction Field module has many functions, but at its core it connects human, machine, and material data for analysis. Workers can clock in and clock out via Field, and those hours can be associated with specific tasks. This information is transmitted back to the office, where the record of historical data can be used to track hours spent on a job against the bid time.
This platform also captures daily weather reports that can be tied into production tracking. For example, says Schwieters, if progress hasn't met expected benchmarks, you can review historical data to see if a day was particularly rainy or extra cold which may contribute to a drop in productivity.
Machine inspection tools are situated within the Smart Construction Field module as well. The operator can use the app on their phone to document service issues and, via the app, can check fuel readings and other machine parameters.
Ultimately, Schwieters says, Smart Construction Field is designed to target specific pain points for customers who haven't previously digitized some of these processes. It eliminates paper and ties different types of data together to deliver a greater overall understanding of what happens on the job site day to day.
"The grander vision is to be able to compare [the data] versus how they bid the project and their progress and be able to say, okay, we're on track or we're behind track and what's causing the delays," he says. Contractors can now have all of this actionable information available quickly in one place.
Connected job site tools can be adopted gradually
The end user does not have to adopt all of this technology at once – connected job site tools are additive, so contractors can expand their adoption with the products and pace that makes sense for them.
"We're seeing a lot of customer demand in this area – a little bit more than we expected," says Schwieters. He thought customers would have to be convinced to adopt the technology, but finds that customers are pushing Komatsu for it, and once customers get excited, developments move faster.
"As the economy tightens up, [contractors] have to do more with the same amount, and they can't move quickly and worry about inefficiencies later," he adds. "Now they have to look at everything because everything is so tight and the costs are rising – you can't be wasteful."