Adjustable height design makes Cat reclaimer/stabilizers capable of cross-slope cutting
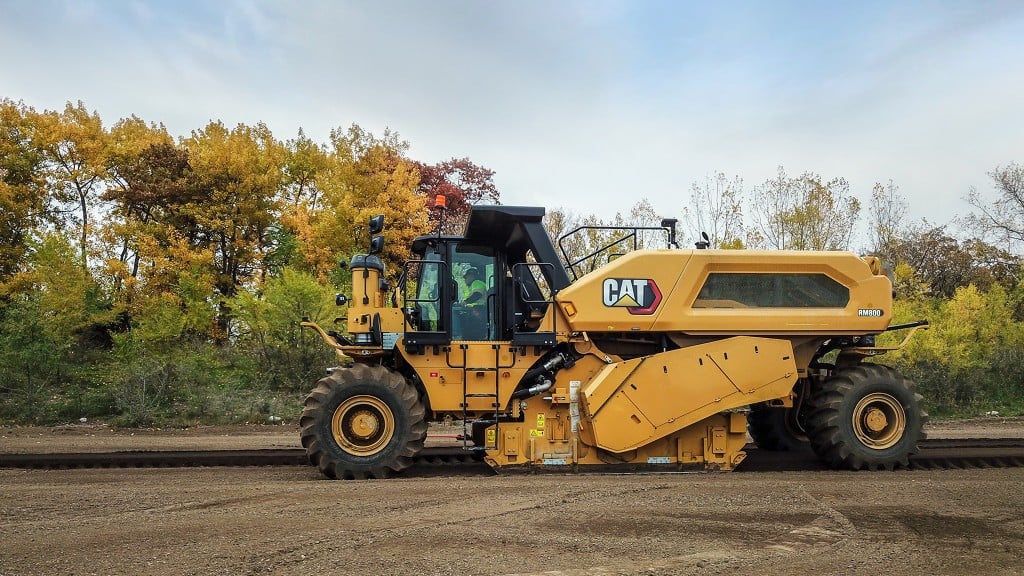
The new Cat RM600 and RM800 reclaimer/stabilizers feature all-new adjustable height design capable of cross-slope cutting. Powered by turbocharged Cat C18 engines, the RM600 provides up to 17 percent more power than the previous RM500B, while the RM800 delivers up to 42 percent more power than the RM500B and up to 23 percent more power than the RM600.
The new models can efficiently cut 2,438 mm (96 inches) wide at up to 508 mm (20 inches) deep. Advanced electronic controls plus automatic load control maintain rotor mixing depth and optimum machine speed to deliver ideal mix quality. Adjusting the front and rear mixing chamber doors enables instant modification of material gradation, and an easy-to-read indicator on the touchscreen display informs the operator of door positions. A rear rotor chamber door float feature simplifies operation by allowing the operator to select the desired down pressure. RM600 and RM800 also offer bi-directional cutting capability.
Key rotor system components from Cat cold planers have been adopted on these reclaimer/stabilizers to ensure dependable cutting and mixing. Featuring a belt-driven rotor drive system, the machine is capable of flush-cutting on the right side. The System K rotor system has been used, featuring fastener-free, dual-taper toolholder and base block components to deliver superior material quality on a range of products. Exit and return-to-cut features simplify operation, save time, and ensure the machine maintains a consistent depth of cut.
The Cat C18 engine's robust cooling system uses cool air intake to maximize fuel efficiency and reduce emissions. Allowing the system to cool more efficiently to extend cleaning and maintenance intervals, automatic cooling fans periodically cycle in reverse to clean the heat exchangers. A single Electronic Control Module (ECM) monitors engine performance and provides diagnostics to the operator.
Front-to-rear weight distribution is optimized for stability in tough cuts. Standard electronically-controlled all-wheel drive maximizes traction and mobility on the new machines. Four height adjustable legs can adjust slope when working on uneven terrain or in challenging soil stabilization applications.
Two high-tensile, six-rib belts with automatic tensioning prevent slippage, while the rotor drive features a hydraulically actuated, heavy-duty clutch that does not require adjustment. Abrasion-resistant, high-strength alloys of the System K rotor can withstand tough, high-power applications, and the cutting tools are strategically placed to deliver ideal material sizing and homogeneous mixing results. The versatile rotor can be configured with bolt-on paddle toolholder protection for full-depth reclamation applications or wedge protection to reduce drag for soil stabilization.
Wheel positioning at the corners lends to a highly maneuverable reclaimer/stabilizer design. The machines can navigate an incredibly small 3.1-m (10.1-foot) inside turning radius. Four steering modes - front only, rear only, crab and coordinated - further improve on-site maneuverability. Offering up to + or - 12.5 percent (8 degrees) of slope on either side when working on uneven terrain or to maintain traction in challenging soil stabilization applications, the four-post, adjustable-height design improves stability and cutting precision.
Controls are grouped by function for quick and easy access. A small handwheel provides precise steering, while the operator easily matches machine speed and functions to gradation specification via the large, 25 cm (10 inch) colour touchscreen displays and pushbutton controls.
Hydraulically sliding side-to-side, the cab is easily positioned to enhance visibility to the front and sides of the machine. Floor-to-ceiling glass and an angle pane on the right-hand side provide a clear view to the work ahead and the leading edge of the cutting chamber. The cab's fully pressurized design with air conditioning and heater/defroster provides a comfortable environment for the operator while keeping noise, dust and the elements out.
Standard and optional cameras augment performance and safety for the new RM600 and RM800. Enhancing fore and aft visibility, standard front- and rear-mounted cameras provide configurable guidelines on the touchscreen display. Two standard cameras mounted above the front and rear mixing chamber doors give operators visibility to obstructions and material gradation. Optional side-mount cameras provide views to each side of the machine.
oil service intervals occur every 500 operating hours. Provided recommended sampling schedules are followed, hydraulic oil service and coolant replacement intervals are extended to 6,000 and 12,000 hours respectively. Accessing maintenance points is easy with daily checkpoints centrally located on a secure platform.
The standard compressed air system can power pneumatic tools and offers two access points to reduce the time for rotor bit changes. Service mode allows the engine to run while the machine is locked out, supplying compressed air so the rotor can be safely serviced. Side service doors provide quick access to inspect or change end ring bits without reaching inside the rotor chamber. Further simplifying rotor maintenance, the rotor can be hydraulically powered to turn in either direction using a control pendant.
The new models feature built-in diagnostics to monitor machine systems, alert the operator of performance issues and simplify troubleshooting. Standard Product Link provides critical machine condition, operating and location data and enables the use of Cat Remote Services.