Simpler autonomous hauler integration delivers cost and safety benefits for smaller sites
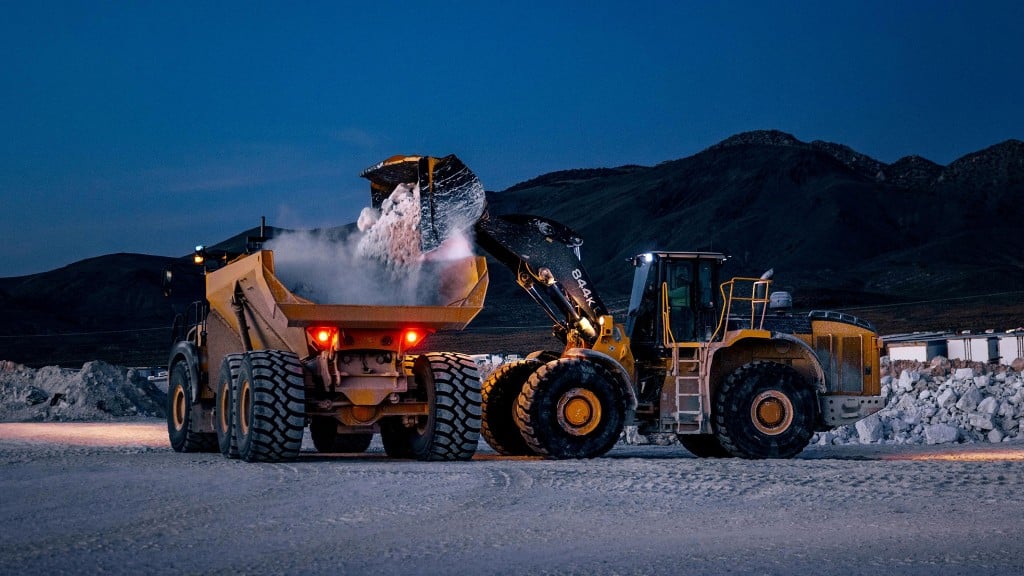
Autonomous haulage systems (AHS) are increasingly being deployed globally at large mining sites with measurable impact on productivity and cost savings. Today, this technology has become available for smaller sites as well.
Autonomous systems have helped many large operations improve efficiency and safety while reducing the need to put humans in undesirable or dangerous environments. Though the value of AHS is recognized, it has remained largely out of reach for smaller fleets in terms of payload, number of trucks, or both.
Autonomy changes the math for which trucks are most efficient. Instead of relying on larger haul trucks, smaller and more fuel-efficient trucks can now be deployed to run autonomously and continuously. New AHS solutions coming to market are designed for ease of deployment to provide users with a faster return on investment.
The benefits of AHS
Recent advancements in the development of autonomous technology have shown that integrating autonomy can be simple, affordable, and efficient. As the adoption of AHS systems grows, the benefits are becoming clearer, including improved safety and productivity cost savings and greater access to data for flexible decision-making.
Increased safety. Autonomous hauling systems eliminate the need for human operators in the cab of a truck, which can reduce the risk of accidents and injuries. AHS-enabled trucks can also be equipped with sensors and other technologies that detect hazards and can respond more quickly than a human operator can.
Improved productivity. AHS-enabled vehicles can operate 24/7 without needing rest breaks, shift changes, or other interruptions. They also can operate with greater precision than humans. Off-loading standard routes and other haulage activities to automated systems allows human operators to focus on more complex, higher value tasks.
Reduced costs. Autonomous hauling systems can reduce labour costs by eliminating the need for as many human operators, which can help to ease the effects of the chronic shortage of skilled labour. They also can cut the cost of maintenance because they operate more efficiently and can detect potential issues before they spiral into something that needs major repairs.
Analytic insight. AHS-enabled systems run on - and collect - massive volumes of data and transmit it to operators in real-time, providing valuable insights into equipment performance and overall operations. This data can then be used to optimize processes, improve safety, and reduce costs over time.
Autonomous systems retrofitted onto existing fleets
As mining sites consider their investment into AHS, among the first conversations should be around how to maximize the investment of existing fleets. Bell Trucks America (BTA), the master distributor of Bell Equipment's haulage vehicles in the United States, partnered with Pronto to develop and deploy autonomous systems for quarries and mines across North America.
Available for newly purchased vehicles as well as ones that are currently deployed, Bell Trucks operators with AHS can now operate their vehicles remotely, including monitoring and supervising activity on a mobile app on their smartphones.
The Pronto AHS solution for Bell provides authorized personnel the secure notifications, performance and location monitoring, and source and destination selection for vehicle movements while accurately capturing measurements such as fuel payload and utilization at the individual truck level. These metrics can be reported at the site level for an overview of the mine's operation.
What to look for in an AHS
When evaluating an advanced AHS platform, site managers should first consider evaluating systems that have technology that is fully cognizant of its surroundings, regardless of environmental conditions such as weather or visibility. Additionally, it's encouraged to find advanced AHS platforms that use cameras and the global navigation satellite system (GNSS) only.
Finally, site managers must consider the costs associated with change management for any new system, and seek an AHS that is simple to deploy, minimizes training time, and ultimately maximizes the benefits of the AHS integration. AHS systems available today are OEM-agnostic, providing owners with the ability to maximize existing investments in their fleets or purchase the best equipment available to fulfill their requirements.
Just as it has for larger global operations, AHS deployments have the potential to greatly improve operations for small- and mid-size mining firms, to achieve the same, if not better, successes in productivity, safety, and cost savings.
Cat Culkin is CTO with Pronto.