Komatsu hybrid excavator excels at truck loading
Electric assist boosts digging and dump speed
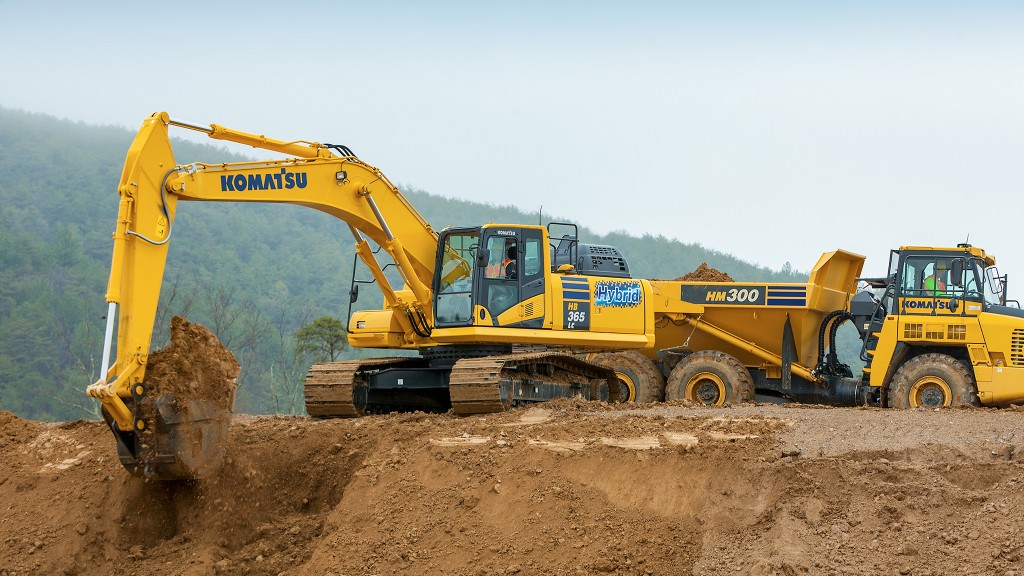
Hybrid excavators have been part of Komatsu's line for more than a decade. Today, the HB365LC-3, Komatsu's third-generation electric hybrid excavator, provides contractors whose excavators spend time in truck loading or similar applications with an option that reduces fuel use while ensuring quick and responsive performance.
Komatsu started its hybrid excavator program with 20-ton machines and got bigger over time. The HB365LC-3 is a 36-ton excavator that can handle many jobs while remaining small enough for easy transport between job sites. It uses an electric system connected to the swing to capture and return energy when the machine is turning, freeing up hydraulic power that speeds up boom, arm, and bucket response.
This is different from a hydraulic hybrid, which uses an accumulator to collect hydraulic energy during swing deceleration or lowering the boom, then puts that energy back into the hydraulic system. Komatsu's electric hybrid system is entirely independent of the hydraulics. The electric motor collects energy as the swing slows and provides a boost when the excavator turns again. This means that the swing action uses no hydraulic power, explained Kurt Moncini, Komatsu senior product manager.
"What's interesting about that is we can now be very selfish because the power that would normally have been pulled from the engine and hydraulic system to initiate the swing can go 100 percent to the boom, arm, and bucket - the working end of the excavator. It is now all about performance. People will get off that machine and say ‘Wow, this is the fastest 360 I've ever run.'"
Electric swing is ideal for truck loading
The HB365LC-3's improved swing cycles make it ideal for truck loading and similar applications, according to Taimoor Khan, business development manager, carbon-neutral products, for Komatsu. Hydraulic effort is used the most when the machine digs out a bucket, lifts that material, and extends the arm. If the swing action moving the machine from pile to truck is done using hydraulics, then the digging, lifting, and extension actions are slowed as energy is shared with the swing. On the HB365LC-3, all the hydraulic power goes into lifting and loading while the swing is handled electrically.
"Any application with greater than 90-degree truck loading will result in improved cycle performance while reducing fuel consumption and carbon footprint," Khan said.
The additional hydraulic effort explains why operators describe the machine as "snappy," Moncini added – the electric motor takes one function out of those being handled by the hydraulics and improves performance at all points of the machine's movement. More lifting power moves dirt more responsively for the operator.
Efficiency boost pairs with emissions reduction
Hybrid operation also has solid results on the bottom line. Compared to similar Komatsu diesel machines, the HB365LC-3 is 20 percent more fuel efficient, 15 percent more productive, and generates 20 percent lower CO2 emissions. It is also 2 decibels quieter than its diesel counterparts.
The hybrid only has four additional components compared to standard machines: a generator on the engine, a generator on the swing system, a capacitor, and an inverter. The system adds very little maintenance requirements over the diesel machine. Moncini said that Komatsu extended special warranty terms on the hybrid to reduce any concerns about the electrical componentry.
Komatsu makes the HB365LC-3 available with the same features and options as its diesel counterpart. A unit shown at CONEXPO-CON/AGG 2023 featured Smart Construction Retrofit, Komatsu's guidance kit which provides access to 3D design and payload data to help add accuracy, control load volumes, and improve operations.