Full-scale carbon capture, utilization, and storage plant moving forward at Alberta cement facility
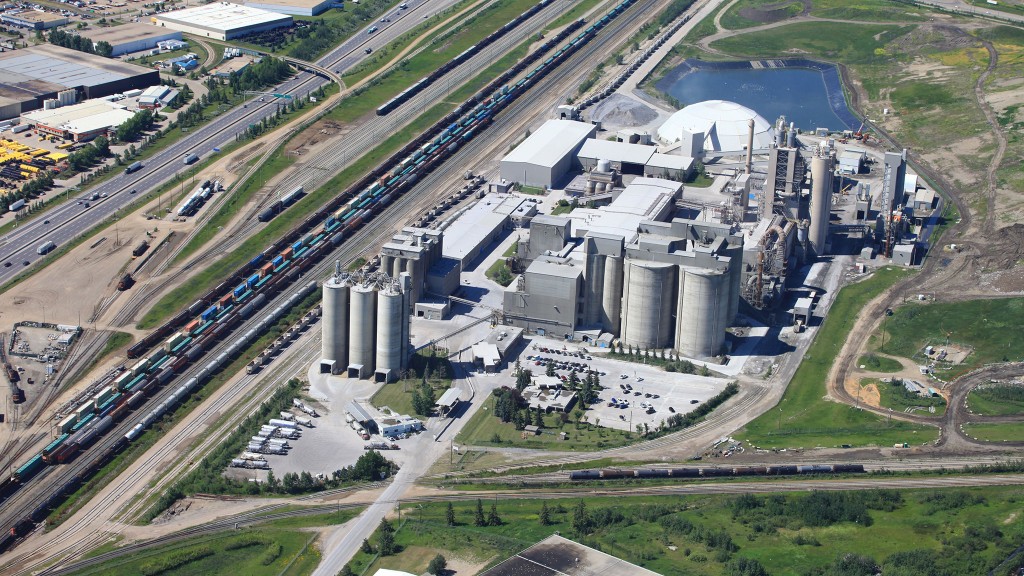
Heidelberg Materials announced that Mitsubishi Heavy Industries, Ltd. (MHI) has delivered and installed a "CO2MPACT" compact CO2 pilot capture system at its cement plant in Edmonton, Alberta.
Through a partnership between Heidelberg Materials, the Government of Canada, and the Government of Alberta, the facility is expected to become the first full-scale carbon capture, utilization, and storage (CCUS) solution for the cement industry globally. The new facility, which Heidelberg Materials anticipates being operational by late 2026, will capture more than 1 million tonnes of CO2 annually from its Edmonton cement plant and the combined heat and power facility that is integrated with the capture process.
Alberta Minister of Environment and Protected Areas, Rebecca Schulz, joined the Heidelberg Materials and MHI teams at the Edmonton cement plant to formally initiate operations of the pilot CO2 capture system. "Alberta is widely recognized as a leader in developing CCUS technology thanks in large part to industry trailblazers like Heidelberg Materials," said Schulz. "Our province has invested billions of dollars to help industry cut emissions and will continue to support practical innovations that create jobs and grow the economy. We look forward to seeing this exciting Alberta success story continue in the years ahead."
This project supports Heidelberg Materials' vision of leading the decarbonization of the cement industry. Actively contributing to the development of the new 1.5 degree C framework, Heidelberg Materials was the first company in the cement sector to have its targets endorsed by the Science Based Targets Initiative (SBTi) in 2019.
"Today is a substantial milestone in our journey to building the world's first full-scale carbon capture project in the cement industry ," said Joerg Nixdorf, Vice President Cement Operations, Northwest Region for Heidelberg Materials North America. "This initiative focuses the cement industry's decarbonization efforts on the Province of Alberta, and we are encouraged by this significant step to lead the sector in CCUS."
The Edmonton cement plant will leverage MHI's proprietary Advanced KM CDR Process using the KS-21 solvent (jointly developed with The Kansai Electric Power Co., Inc.) and will initially pilot the technology by testing different fuel sources and various plant operating modes. The pilot plant will enable Heidelberg Materials to validate the effectiveness of MHI's technology on its specific flue gas as part of a two-stage competitive process that is currently underway to inform the final design. At full operation, captured CO2 will be transported via pipeline and permanently sequestered. MHI's involvement also includes providing remote support services for the facility, using its proprietary remote monitoring system.
"MHI Group is proud to collaborate with Heidelberg Materials as an innovative solution provider for decarbonization of the cement sector, which is still a new frontier for CCUS and excited to contribute to the effort on carbon neutrality in the Province of Alberta," said Kenji Terasawa, CEO and Head of Engineering Solutions.
MHI has been developing the KM CDR Process (Kansai Mitsubishi Carbon Dioxide Recovery Process) and Advanced KM CDR Process in collaboration with Kansai Electric Power since 1990. As of August 2023, the Company has delivered 15 plants adopting the KM CDR Process, and three more are currently under construction. The Advanced KM CDR Process uses KS-21, which incorporates technological improvements over the amine-based KS-1 solvent adopted at all 15 of the commercial CO2 capture plants MHI has delivered to date. The advanced version offers superior regeneration efficiency and lower deterioration than the KS-1, and it has been verified to provide excellent energy-saving performance, reduce operating costs, and result in low amine emissions.