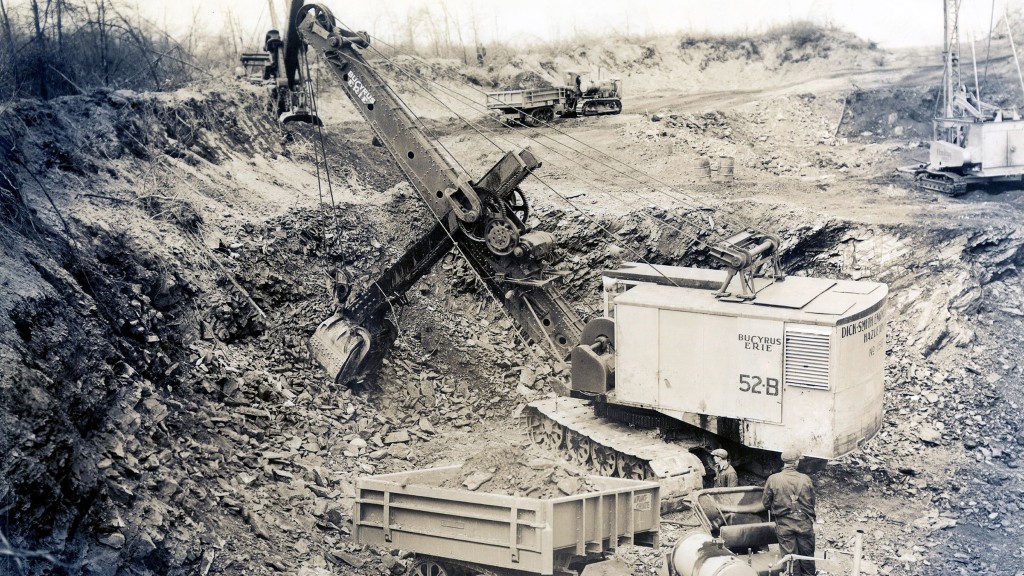
The year - 1893. Only 44 of today's 50 states formed the union, and Grover Cleveland was elected the country's 24th president. College basketball was in its infancy, holding its first official game. The Bucyrus Steam Shovel and Dredge Company opened a new manufacturing facility in South Milwaukee, Wisconsin, U.S.A., to improve and expand its production facilities.
Since this point in history, the management decisions and equipment produced in South Milwaukee have not only changed the construction and mining industries but also the course of history. In the early 1900s, Bucyrus-produced equipment was a major contributor to the monumental excavation projects of the time.
"Dredges were used as part of the California gold rush, and shovels were a part of the vast Mesabi Iron Ranges," recalls Shawn Paap, commercial manager for Cat Electric Rope Shovels (ERS). "The New York State barge canal enlargement project, the largest U.S. earthmoving project between 1902-1912, also used Bucyrus dredges."
The company's 40- to 50-ton steam-powered shovels played a significant role in building the Panama Canal, one of the most exciting projects in human history. Throughout the project, 77 shovels produced in South Milwaukee were used to construct the canal. When combined with the shovels produced by Marion Steam Shovel Company, a Bucyrus heritage company, 101 of the 102 shovels used in the project were from Bucyrus.
World War II saw unprecedented demand for excavators in Europe, and virtually 100% of the company's entire output from 1942 to 1945 was devoted to the war effort. Post-war, the company embarked on a $2 million project to increase plant capacity by 20%. By the middle of the 20th century, Bucyrus was a global company with an expanded product offering, and more than 74,000 Bucyrus machines had been produced and used in over 166 countries.
Important innovations
Central to the strategy of moving production to South Milwaukee was to increase the manufacturing efficiency of its core large machinery, such as rope shovels and draglines. Over the last 130 years, more than 32,000 machines have been produced at this location, and to this day, massive Cat® Electric Rope Shovels are being produced by the plant.
The heritage of today's Cat 7495 and 7495HF models used for the mining industry began as railroad shovels. Between 1882 and 1930, more than 1,850 railroad shovels were produced. Those first models weren't mobile by today's standards, being pushed on rails or rollers. This manual process to move the massive machines didn't meet the efficiency needs of mining.
A series of early innovations originating from the South Milwaukee facility helped to improve rope shovel efficiency and durability. Borrowing Caterpillar's technology of the 1920s, the steam-powered shovels adopted track-style rotating belts to significantly increase mobility. Prior to the 1930s, the entire rope shovel structure was riveted, but those rivets were replaced by welds to improve durability.
A major transition for rope shovels and the industry was the shift from steam power to electric. Bucyrus pioneered the use of electricity as a power source more than 100 years ago, as early as 1917. The advent of a new DC electrical power system in 1919 ushered in the infancy of today's modern ERS design, and the transition from steam power to electric was completed by 1939.
"As today's mining industry increases its focus on the electrification of equipment to reduce carbon emissions and boost efficiency, Caterpillar is proud to be the leader in a product that has been electrified for several decades," says Caterpillar Product Value Stream Manager, Flor Rivas.
Revolutionizing the market for Bucyrus and the industry at large, machine design transitioned to much less complicated AC electric motors from the rudimentary DC drive system. "AC drive motors were simpler, lasted longer, required less maintenance, worked faster and more efficiently, and delivered greater power than DC motors," comments Mike Haws, technical steward for Cat Electric Rope Shovels. "The introduction of insulated gate bipolar transistor (IGBT) fuseless technology led to the evolution into digital gate turnoff (GTO) systems. And a partnership with Siemens in the 1970s put Bucyrus on the cutting edge of AC drive technology, pushing drive system availability upward to 99 percent."
Caterpillar continues its rich history
Since Caterpillar acquired the Bucyrus product line in 2011, an excellent ERS product has been elevated to the next level of safety, productivity, and reliability by making the machines safer, easier to access and maintain, perform better under extreme conditions, efficiently integrate technology, and deliver higher availability.
Caterpillar introduced a liquid-cooled motion regulator cabinet shortly after the acquisition to more efficiently dissipate the heat generated by electrical components. This enabled the global product to reliably operate in extreme temperatures ranging from -40˚ C/F to 50˚ C (120˚ F) and at altitudes reaching 5250 m (17,220 ft) without derating. The company also introduced a faster propel transfer switch to cut lag time by 70%, improving productivity.
After intensely studying the habits of operators with varying skill levels, Caterpillar introduced its first technology advancement package for the Cat 7495 series shovels in 2016, Operator Assist - Enhanced Motion Control (EMC). This innovation delivered machine protection and simplified operation to boost longevity and improve productivity. Protecting the dipper, the software automatically limited swing forces when the operator attempted to swing the dipper through the bank. It also safeguarded the crowd ropes and brake, and it prevented boom jacking situations to improve machine cycle times and productivity.
Today, more ERS technologies to improve efficiency and lower costs are being introduced at a faster pace than ever before. This year, Caterpillar launched two new technology packages for ERS models - the Integrated Technology Package (ITP) and Operator Assist Package (OA).
Eliminating the need for additional in-cab displays from one-off tech packages, ITP, and its modules serve as the foundation for launching current and future technologies. It also provides seamless integration and quicker installation of Cat MineStar Solutions' operational technologies that help to track, monitor, and manage the shovel.
OA offers more advanced machine protection and operating simplicity. It features a LiDAR vision system - similar to the technology found on autonomous mining trucks - to scan the front of the shovel, helping to avoid accidental collisions between the dipper and machine.
Cat ERS models - moving mountains
Since the acquisition, Caterpillar has produced more than 200 of the 120-tonne (134.4-ton) capacity ERS models in South Milwaukee, initially under the Bucyrus name and now as Caterpillar. The average lifespan of today's Cat 7495 shovel is 20 years with machines working in some of the harshest operating conditions around the world, from the subfreezing oil sands of Canada to the arid Chilean deserts where average annual rainfall is less than 24.5 mm (1.0 in).
From 1990 to 2022, roughly 237 machines - both Bucyrus 495 and Cat 7495 series - have moved more than 105 billion tonnes (116 billion tons) of material. If this quantity were moved by the 364-tonne (400-ton) Cat 797 mining truck, it would have resulted in 290.1 million truckloads and have taken over 13.9 million hours to complete, given a 2.88-minute cycle and truck spotting time.
"We are proud of our long heritage in South Milwaukee, the impact the equipment produced at this location has had on the global market over the last 130 years, and the talented and dedicated team continuing the tradition of excellence in the production and support of Cat electric rope shovels and draglines," concludes Jeremy Niedens, facility manager - South Milwaukee for Caterpillar.