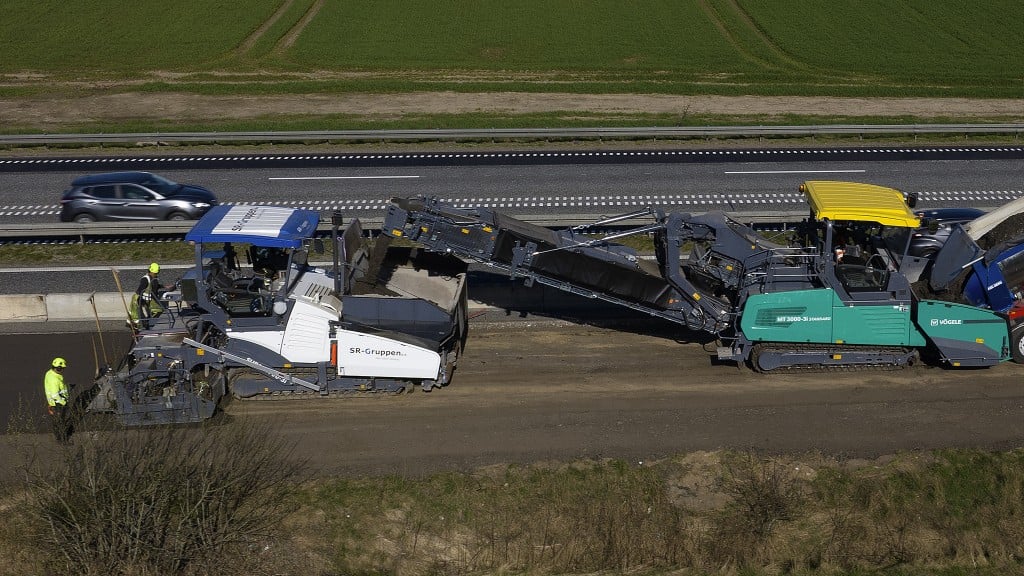
When a 6.5-km stretch of highway in Denmark needed to be renewed, the project called for recycling of material from the existing asphalt pavement. Wirtgen large milling machines and a mobile cold recycling plant proved successful by reducing the project time as well as carbon emissions.
Cold recycling of road surface material is the most sustainable construction method available for structural rehabilitation. The cold mix that is produced with foamed bitumen and which makes up the new base layer is ideal for roads of any traffic level. For the project along Denmark's E45 highway near the famous Legoland, the KMA 240i mobile cold recycling plant paired with W 210i and W 250i large milling machines to work smoothly on a tight deadline.
"We produced up to 300 tons of cold mix per hour with the KMA 240i," reports Morten Wold, Divisional Manager at SR-Gruppen A/S, which was managing the project.
The E 45 was milled at a width of between 3.15 and 5.9 metres and a depth of 28 cm. Milled material was transported to the KMA 240i milling plant nearby. The mobile cold mixing plant enables the contractor to stay close to the asphalt removal and paving location, minimizing material transport and significantly reducing the overall CO2 emissions of the project.
A suitability test was carried out on the reclaimed asphalt pavement (RAP) before the start of the construction phase. The ideal mix formula included 2.2 foamed bitumen, 6 percent lime, and 0.8 percent cement.
The mix was then loaded into an impact crusher and reduced to a kernel size of 0-32 mm, loaded by wheel loader into the KMA 240i's large capacity receiving hopper and fed into the twin-shaft continuous mixer. Two feed augers with a double-trough system and precision weighing took care of the separate addition of lime and cement binding agents.
Wirtgen expanded the capabilities of the KMA 240i on the spot by installing an additional feed auger. The continuous weighing system ensured that the additives were precisely dosed. The foamed bitumen was added using the integrated, microprocess-steered dosing system.
The stabilized bituminous cold mix was loaded directly into large 36.5-ton trucks and transported immediately to the job site. Graders and Hamm rollers prepared and compacted the frost protection layer beneath the milled off asphalt pavement as a stable roadway for the pavers and trucks following on behind.
A MT 3000-2i mobile feeder from Vogele ensured smooth and seamless material flow on the construction site. The unit makes it possible to stockpile large amounts of cold mix. Transport logistics were challenging as no complete road closures were allowed during the project. The MT 3000-2i provided flexibility to rehabilitate two lanes of highway without complete road closure.
A Vogele SUPER 1900-3i paver laid down the material true to grade and slope, creating a 20-cm base layer of cold mix as the new highway foundation. A Hamm HD 120i tandem roller with an operating weight of more than 12 tonnes provided the necessary compaction, while a Hamm GRW 280i pneumatic-tire roller handled the final surface treatment.
In two days, a binder course and surface layer with a thickness of 8 cm was laid. An asphalt modified with polymers that suits the requirements of the high-traffic trucking lane and complements the base layer was selected.
Company info
6030 Dana Way
Antioch, TN
US, 37013
Website:
wirtgen-group.com/en-us
Phone number:
615-501-0600