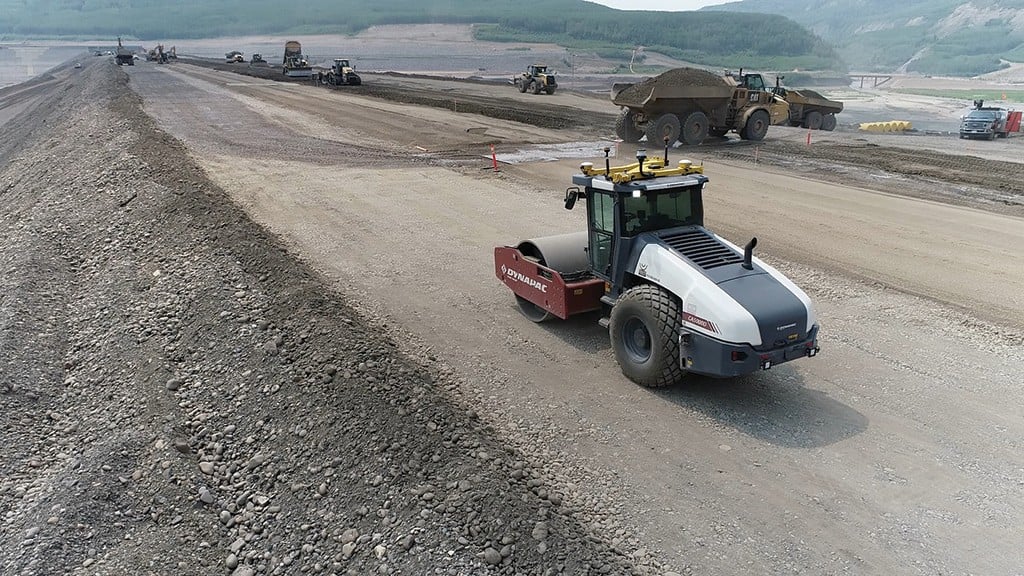
In the remote wilderness of northeast British Columbia, Trimble has tested its Earthworks Grade Control Platform for Autonomous Compactors on a Dynapac CA 5000 soil compactor on the Site C Clean Energy Project.
Located on the Peace River, the Site C megaproject is an ideal proving ground for autonomous equipment: the job site is remote and transporting labour to and from the area is a challenge. Work areas are not complicated, and soil compaction is a repetitive, straightforward task.
"The Site C test piece was very monumental for us," says Cameron Clark, earthmoving industry director for Trimble's civil infrastructure solutions. "It was the first time we've taken an autonomous compactor running on a real job site, but not only just a real job site, a live, active job site. And it was actually helping contribute to the construction and compaction on the dam."
Why test full autonomy for soil compaction?
There are unique safety challenges on these types of projects, and there are processes that could be safer and more efficient with the use of fully autonomous equipment.
When building a dam, the edges of the area need to be properly compacted, but edges need to be overbuilt to ensure that operators aren't getting too close to the edge. An autonomous machine could reduce the extra work that is currently necessary to ensure the safety of human operators.
For now, fully autonomous equipment is best suited to repetitive tasks within clearly defined boundaries – such as quarries, mines, and other remote work areas.
"We chose the compactor because it's very repetitive, it's very mundane, and it's a workflow that typically the lesser-skilled people are running," says Clark. "There's a lot of waste at the moment because it's hard to steer and there are extra overlaps. But, when you look at what you need to make it do, it's very repeatable. They're doing the same thing and not actually moving material."
How Trimble carries out autonomy tests
Alongside a mixed fleet of human-operated machines, the autonomous compactor completed 37 hours of work. When Trimble tests fully autonomous equipment, a person is always watching the machine and has e-stop capability if it does something it's not supposed to. If radar and lidar sensors on the machine detect a problem, it will also stop. A geofence is also activated.
In the future, when fully autonomous equipment operates in this type of application, it will be part of the workflow of other equipment on the site. For example, an operator in a motor grader or dozer will have the autonomous soil compactor follow behind and that dozer or motor grader operator will send instructions to the compactor.
According to Clark, there are a number of factors that need to come together when deploying a fully autonomous machine: mission planning, safety, and mechanisms to send tasks to the machine. These factors are common across different types of equipment, so Trimble can learn from the soil compactor and apply those learnings to other machines, such as asphalt rollers, that could benefit from autonomy in the future.
Trimble plans to take what it learned from Site C and apply it to more testing on more real job sites in 2024. The autonomous machine needs to run through multiple scenarios and different compaction patterns to ensure that it can carry out a variety of workflows. Ultimately, the job carried out by the autonomous machine needs to look like expert work.