Massive new Komatsu motor grader for haul road work
The GD955-7 is designed for rugged mine and quarry road maintenance needs
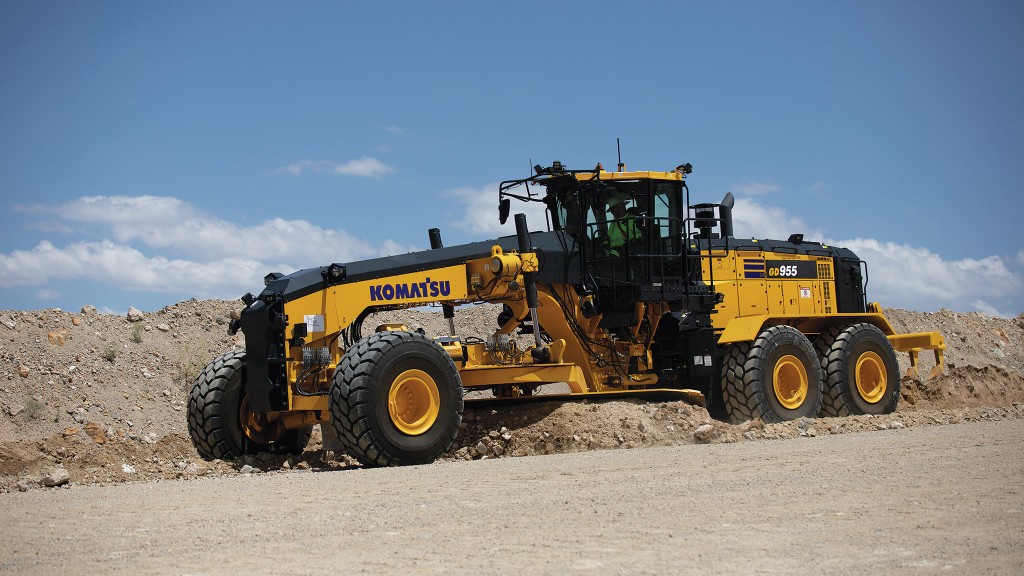
Haul roads at mines and quarries need to be maintained well for efficient use by large trucks. Keeping those roads in good repair requires a big machine that can handle rugged terrain and ensure surfaces are graded smoothly.
Komatsu focused on those needs in developing its new large motor grader. The GD955-7 is big and heavy to ensure efficient grading, while also fast and maneuverable for increased productivity.
Komatsu previously offered the GD825A-2 motor grader for haul road maintenance, but it has been out of the market in North America for some time, according to Product Manager Sebastian Witkowski.
"We've filled that larger motor grader gap with the GD955. While we also offer the GD655, we wanted to scale up and fill those quarry and mining motor grader requirements," he says.
Designed for rugged mine and quarry environments
Komatsu designed the GD955-7 to meet the demands of haul road maintenance. The frame has been developed specifically for mine and quarry environments by using larger gauge, higher-tensile steel, which offers more strength. The operating weight of 104,323 pounds is up 50 percent from the previous model.
Power is provided by a Tier 4 Final-compliant Komatsu engine generating 426 hp, an increase of 48 percent. Operators can use the power mode selection system to pick their engine settings based on working conditions: P mode for full engine output and high productivity, E mode for lighter work handled more economically, and middle-speed mode for operators who want fine travel speed control while working at full throttle.
Those factors give the GD955-7 greater blade downforce which is necessary to dig deeper into hard-packed road surfaces, Witkowski says. New box-type blade lifter brackets handle the increased pressure coming back onto the machine. An 18-foot standard moldboard, which can be swapped for an optional 20-foot moldboard, covers more ground on each pass.
"This machine is specifically designed for applications that are more demanding, some of the harsher conditions, while the blade and moldboard size increases fill a need for larger quarries and mine sites," Witkowski says.
Despite its size, the GD955-7 is maneuverable and capable of making U-turns within the standard width of a 100-ton haul road without the need to fully articulate or cut the wheel.
Bearing-type circle reduces downtime
In rugged environments like mines and quarries, maintenance can be a challenge, so Komatsu designed the new grader to reduce maintenance needs as much as possible. Central to that is the use of a bearing-type circle, which cuts maintenance downtime significantly.
"When you have to stop the machine and manually grease every 50 hours, replace wear plates or make circle play adjustments every 500 hours, that adds up pretty quickly," Witkowski says. "With the adoption of this bearing-type circle, we eliminate the need for those wear plate replacements and circle play adjustments."
The change has led to a 21 percent reduction in maintenance time, he adds.
A Graco auto-lube system is standard on the GD955-7, meaning operators don't lose time greasing individual points before the day's work. A maintenance service point includes fill and evac ports for all vital fluids, providing a central location for daily service.
Fingertip controls reduce hand and arm movements for easier operation
The GD955-7 cab includes air suspension, heated and ventilated seats, and a control layout that gives operators all the controls they need at their fingertips. Rather than the traditional rack across the front of the cab, all the work equipment controls are placed at the end of the armrest, retaining a similar functionality without the reach.
"These operators spend a lot of time in the cab, so we want them to be as comfortable as they can be – a comfortable operator can be more efficient," Witkowski says. "We're seeing up to a 92 percent reduction of hand and arm movements related to the ergonomic position of the fingertip work controls when compared to the traditional antler rack style configuration."
An auto-articulation return to centre feature straightens the machine to a neutral articulation position with the press of a button. When engaged, auto differential lock provides additional traction while managing turning performance, switching the feature off and on when steering input is detected to prevent tire drag.
KomVision, a five-camera vision monitoring system, gives operators bird's-eye visibility to the immediate working area on a dedicated monitor inside the cab and can be paired with an optional rear-view camera on its own monitor for even better views of the work site. A standard LED lighting system includes 14 lamps, along with an LED access lamp and service light, to promote visibility around the machine.
The GD955-7 is equipped with Komtrax telematics, which continually monitors machine health and maintenance and allows fleet managers to review grader conditions remotely, reducing unplanned downtime while providing valuable data to improve operations.
All in all, the GD955-7 is a big, heavy, and powerful motor grader that remains surprisingly maneuverable.
"This ultimately translates into a more productive job site – if haul roads aren't clean and level, those impacts can affect the entire haulage operation," Witkowski says. "Potholes, ruts, and obstructions can impact truck productivity as well, increasing the risk of unplanned maintenance downtime. This grader helps mitigate those challenges while promoting a smooth haulage operation."