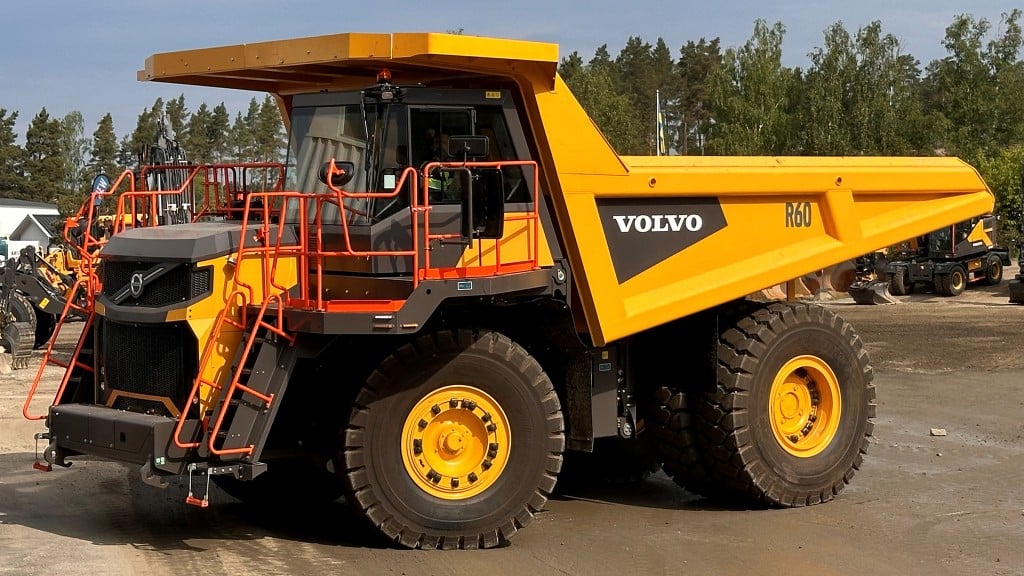
Two new rigid haulers from Volvo Construction Equipment add more payload options for quarry and mine operations while keeping operator comfort and safety in mind.
The R60, with a 55-ton payload, and the 65-ton R70, are designed to reduce total cost of ownership while including comfort and safety in the package. Both are inspired by Volvo's flagship 95-ton R100 rigid hauler and complement the company's articulated hauler range.
Rigid haulers work well in locations with wide, firm haul roads where they can reach speeds of up to 61 km/h and carry material long distances. The R60 can carry a volume of 36.04 cubic metres, while the R70 hauls 42.4 cubic metres. Both have a V-shaped haul body designed for load retention and minimal carryback post-dumping. These haulers feature a fast-tip system for quick dumping, and an optional On-Board Weighing system allows operators to maximize the material carried.
High drive axle multiplication ensures the haulers have plenty of traction, while a high-torque engine is supported by automatic adaptive gear selection offered by Volvo Dynamic Shift Control to help cut fuel use. A selectable Eco mode defaults to the most efficient gear, while the auto engine idle shutdown reduces engine wear.
While moving, the haulers feature gear-dependent speed control and a selectable brake or transmission retarder. The gearbox also has overspeed protection and a neutral coast inhibitor for downhill work. Fail-safe braking and a secondary steering system keep the machine on the right track.
One area brought in from the R100 is the comfortable and safe working environment. Access to the cab from both sides includes anti-slip steps. Inside, a large windscreen and low dashboard combine with a left-positioned operator station for good jobsite views. The 360-degree Volvo Smart View is optional.
An ergonomic seating position and air suspended seat, paired with independent suspension, give operators a smooth ride. Low-effort steering with an adjustable wheel makes driving simpler, and the operator can adjust temperature with a powerful air conditioning system.
Maintenance is eased thanks to 500-hour service intervals, ground-level tagout, and easy-to-reach service points. Common sized bearings make it easier and less costly to keep parts in stock. Onboard service diagnostics and CareTrack telematics aid with identifying potential faults and keep trucks on the road.
The new machines are being made at Volvo CE's Motherwell plant in Scotland, a site that for nearly 75 years has been the global heart of rigid hauler development.